斯塔米卡邦是尿素技术的全球领航者。在此背景下,领航同时也意味着责任。作为工艺许可方,我们将这种责任视作源源不断的努力,以保证我们的工艺装置设计满足我们的客户的需求。在此,我们自豪地展示我们的最新成果:目前可申请许可证的最新装置原理。
我们频繁接触客户、倾听他们的要求,以使我们设定的最新装置原理的目标紧密贴近客户的需求。
• 尽量减少新装置所需资本支出(CAPEX)。
• 尽量减少新装置所需运营支出(OPEX)。
• 确保产品的高质量、低排放和长运转周期。
• 装置免维护。
基于我们在研发上的投资和改建项目上取得的经验,已通过以下方式实现这些目标。
• 低位布置合成设备:尽量减少资本支出。
• 汽提效率的优化选择意味着尽量减少蒸汽消耗并由此尽量减少运营支出。
• 通过使用Safurex®结构材料,实现零氧进入合成工段。这种方式为实现装置的内在安全和免维护进一步铺平了道路,并从下列各个方面进一步简化了工艺设计:
• 淘汰了除氢环节;
• 省去了高压洗涤塔;
• 简化了装置的尾气处理部分。
2 Safurex®和零氧
自从尿素工艺工业化以来,须解决的非常重要的问题便是极端合成工艺条件下应用材料的耐腐蚀性。当将奥氏体不锈钢材料用作制造材料后,需要连续对其进行钝化处理。连续钝化处理通常通过向合成工段添加空气实现,这样做,在反应转化率和工艺安全方面,可对工艺产生不利影响。
但Safurex®制造材料优良的耐腐蚀性为合成工段的改进铺平了道路,采用这种材料后,不再需要进行钝化处理。Safurex®材料这种独一无二的特性经实验室以及在实际合成条件下得到了验证。
在实验室将Safurex®材料与BC.05 (25.22.2)以及尿素级不锈钢材料BC.01 (316L UG)的耐腐蚀性在无氧甲铵溶液中在通常的极端合成条件下进行比较。在此条件下,Safurex®材料并未变得活化,而奥氏体不锈钢材料受到严重腐蚀甚至消失(图1)。
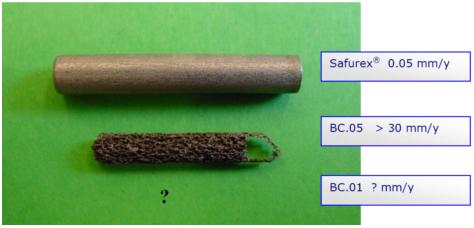
图1 183℃合成条件下在高压釜中进行75天零氧测试
实验室试验证明,合成工艺条件下(开发该材料的设定前提),无氧甲铵环境中的Safurex®材料可耐活性腐蚀。经过多年实践,我们还证实Safurex®满足进行Safurex®开发设定的所有要求。正如您从论文2中了解到的一样,该材料从未显示任何活性腐蚀迹象:Safurex®;这不是梦想。这使斯塔米卡邦完全有信心设计一种尿素装置,在这种装置中采用提供空气使材料钝化的方法已成为历史。
无需钝化处理合成工段中应用材料的尿素装具有以下优点:• 更低的投资成本
• 内在安全的工艺
• 最小化的氨气排放
更低的投资成本
如果取消供给二氧化碳原料的空气源,则可减少合成工段中的惰性气体。因此降低了该装置的投资成本,因:
• 简化了惰性排放气洗涤系统;
• 设计设备更少且更小。
因省去了作为钝化剂的空气,因此也无需燃烧二氧化碳原料中的氢,进一步大大减少了合成工段中惰性气体的量。因此,在低压吸收塔中净化惰性蒸汽前,用减压运行的简单洗涤塔系统替代了通常采用的高压洗涤塔(包括相关设备和管线)。若干装置已论证了减压运行的洗涤塔系统,如本次技术年会的论文3中所示印度芒格洛尔市化学品和化肥公司。斯塔米卡邦新装置理念中,因不再需要换热部分,该洗涤塔系统甚至更为简化。
与需要钝化空气的装置相比,无需钝化空气气源简化了惰性气洗涤系统, 从而使设备更少。
以下设备已废弃;
• 空气鼓风机
• 氢气转换器
• 高压洗涤塔,包括有关调节冷却水系统
• 高压氨喷射器
此外,高压二氧化碳压缩机和废水处理工段更为紧凑,这进一步降低了零氧装置所需投资成本。
内在安全的工艺
无需钝化空气使尿素工艺实现内在安全,因无氧气存在,因此也无易燃混合物存在。零氧装置中无需通过燃烧氢气降低易燃混合物的发生频率,也无需设置泄压空间以尽量减少爆炸影响,这些措施已成为多余。
最小化的氨气排放
因无需钝化空气致使系统中惰性气体减少,排放的惰性气体的量明显减少,由此将氨气排放降至最低。所以,无需钝化空气也使零氧装置具有环境优势。这已经伊朗设拉子石化公司进行的低氧试验成功得到验证(另见2006年AIChE技术年会的出版物)。
3 高位合成装置
自60年代斯塔米卡邦尿素装置采用高压二氧化碳汽提塔以来,合成工段的尿素溶液直接送入所谓的低压循环工段。那时,这算是一种创新,因为在那之前,通常需要包括纯氨循环的管内中压循环工段,且产生的合成尿素溶液可从该中压段送入低压循环工段。只有斯塔米卡邦二氧化碳汽提塔的高汽提效率,特别是针对氨,才可省去该中压循环和氨循环工段[1 管内中压循环工段,接收来自高压汽提塔的尿素溶液,并不会与附加中压循环工段混淆。汽提装置中的附加中压循环直接接收合成塔中的原料气,因此使高压汽提塔和高压甲铵冷凝器卸除了荷载,经斯塔米卡邦证实这是一种非常强大的改造工具。]1。
除了斯塔米卡邦装置,各类型的尿素装置现也通过各种方式使用高压汽提塔。但这些汽提塔既不使用二氧化碳作为汽提剂,也不在相对高的压力下运行,限制了可达到的最大汽提效率使自汽提塔的溶液仍需进入管内中压循环段,常伴随氨循环。
因斯塔米卡邦在相对较低的压力下(约145巴)使用了二氧化碳作为汽提剂,可达到的最大汽提效率较高,就氨和二氧化碳而言,汽提效率通常能达到80%。为此,将合成工段的尿素溶液直接送入低压循环段仍旧仅能用于斯塔米卡邦尿素熔融装置,其具有以下优点:
• 循环工段投资成本更低;
• 因装置设计简单,更容易操作;
• 循环工段维护成本更低;
另一方面,80%的汽提效率以汽提塔中的中压蒸汽消耗为代价,导致在甲铵冷凝器内产生量相对多的过多低压蒸汽(约4.5 - 5.5 巴)。寻找有效利用这些过量低压蒸汽的途径是一个挑战。一种典型的应用是用于二氧化碳压缩机的蒸汽涡轮驱动机中,此种情况下,可替换并减少涡轮中的高压蒸汽消耗。但也并不经常这样做。在低压蒸汽过量的情况下,过低汽提效率降低了尿素装置的整体中压蒸汽消耗(也见本论文附件,其中讨论了优化汽提效率这一主题)。
斯塔米卡邦二氧化碳汽提装置的另一个主要特点在于,内部合成循环仅依靠重力流。这仍旧是一个主要优点,因为重力是100%可靠的。然而,到目前为止,合成回路重力流仍需要提高尿素合成塔的高度。
另一方面,斯塔米卡邦希望能提供一种低高度装置原理以进一步降低投资和维护成本。问题之一便是如何使足够蒸汽进入合成塔而不必过多消耗用于汽提的二氧化碳。
所以,斯塔米卡邦的挑战是如何设计一种尿素合成工段,使合成塔立在地面,而其主要合成循环仍能够依赖重力流,且仍能将汽提塔的尿素溶液直接排放至低压循环工段。
3.1 斯塔米卡邦尿素装置高度的布置
合成工段须始终垂直布置,以能够利用重力取代旋转设备。显然,重力100%可靠且不会磨损。
早期的二氧化碳汽提装置(1967~1969)的高压甲铵冷凝器(在其中氨和二氧化碳被冷凝)被安装在尿素合成塔顶上(图2)。
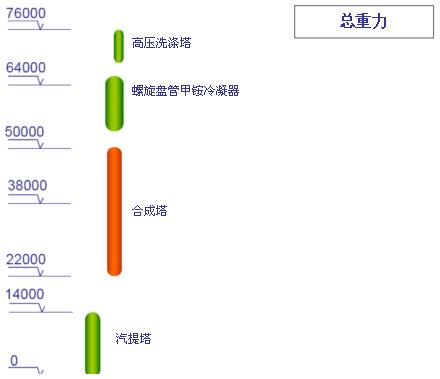
图2 合成塔顶上的高压甲铵冷凝器
这样做是为了允许冷凝甲铵受重力作用流到合成塔。高压洗涤塔建在高压甲铵冷凝器上以使冷凝甲铵在受重力作用流到冷凝器。尽管甲铵冷凝器为紧凑螺旋盘管型(比降膜冷凝器更短),但这种布置仍须高强钢结构。随着装置能力变大,用壳管降膜式高压甲铵冷凝器取代了螺旋盘管高压甲铵冷凝器。该冷凝器不能再安装于合成塔顶上,而将安装高度降低到了合成塔底部,但仍充分利用了重力流。因此高压洗涤塔的液位就能降低至之前的高压甲铵冷凝器(图3)的液位。
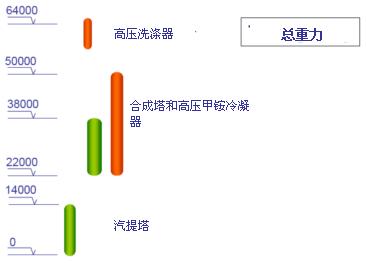
图3 合成塔顶上的高压洗涤器
1970年左右,汽提工艺中引进了高压氨喷射器,利用氨作为驱动力将甲铵从高压洗涤塔运送至高压甲铵冷凝器。运送的甲铵量相当小,且与其它工艺相比,尽管因高压洗涤塔现在能安装在与合成塔底相同的位置,极大程度上降低了其结构高度,斯塔米卡邦汽提工艺仍旧是一种‘重力驱动’工艺(图4)。
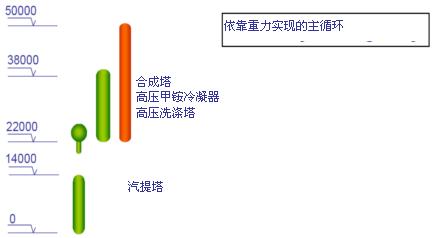
图4 合成塔底位置的高压洗涤塔
由于将高压洗涤塔重新定位至合成塔底部位置,须通过合成塔的高度来规定合成高度。近年来,池式冷凝器和池式合成塔的发展进一步降低了合成塔的高度,因此也降低了合成高度(图5)。
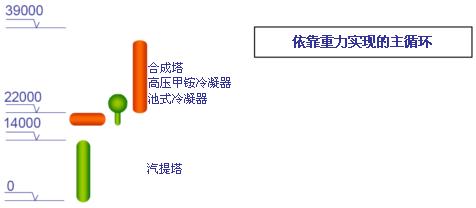
图5 替代降膜式甲铵冷凝器的池式冷凝器
池式冷凝器是针对立式壳/管高压甲铵冷凝器的一种改进。从根本上说,这是一种卧式、浸没式高压甲铵冷凝器,其产生的尿素量相对较大。在立式尿素合成塔下游完成尿素合成。因尿素的形成主要发生在池式冷凝器中,下游的尿素合成塔合成量明显减少,降低了装置高度。
池式冷凝器理念的成功随之而来的是池式合成塔的发展,现由两家所有人经营:DSM和土库曼斯坦化肥和化学品公司(第三套池式合成塔装置还在建造中),即巴基斯坦法蒂玛化肥公司。池式合成塔是一种集成高压甲铵冷凝器功能并在其上若干米位置安装了高压洗涤塔的卧式合成塔(图6)。因此,池式合成塔理念中同时除去了立式合成塔,再次降低了装置高度。可省去输送从高压洗涤塔回收甲铵的喷射器,使整个合成回路仅通过重力运行。
池式冷凝器是针对立式壳/管高压甲铵冷凝器的一种改进。从根本上说,这是一种卧式、浸没式高压甲铵冷凝器,其产生的尿素量相对较大。在立式尿素合成塔下游完成尿素合成。因尿素的形成主要发生在池式冷凝器中,下游的尿素合成塔合成量明显减少,降低了装置高度。
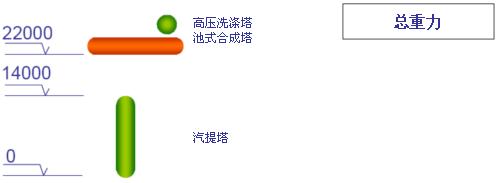
图6 取代立式合成塔和高压甲铵冷凝器的池式合成塔
如上所述,斯塔米卡邦二氧化碳汽提工艺有效期内,存在以下五种主要合成布置方式,高度历年递减(图7)。
1. 完全依靠重力:位于合成塔顶上的高压冷凝器。2. 完全依靠重力:位于合成塔之上的高压洗涤塔。
3. 通过重力实现的主循环:高压洗涤塔位于合成塔底部位置。
4. 通过重力实现的主循环:用池式冷凝器取代降膜式高压甲铵冷凝器。
5. 完全依靠重力:用池式合成塔取代立式合成塔和高压甲铵冷凝器。
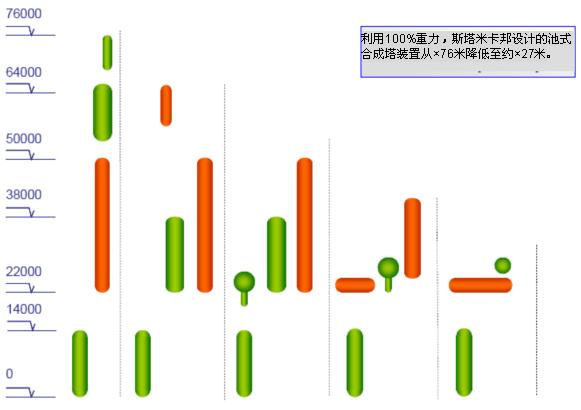
图7: 现在斯塔米卡邦尿素合成系统布置的发展
在不牺牲合成工段的重力流并维持简单循环设计的情况下,斯塔米卡邦已成功将池式合成塔装的塔顶位置从76米降低至27米,并将池式冷凝器装置的顶部位置降低至39米,同时,单套设备能力从200公吨/天增加至3700公吨/天(已是目前的最大运转能力)。
3.2 池式合成塔设计理念的最大能力在不牺牲合成工段的重力流并维持简单循环设计的情况下,斯塔米卡邦已成功将池式合成塔装的塔顶位置从76米降低至27米,并将池式冷凝器装置的顶部位置降低至39米,同时,单套设备能力从200公吨/天增加至3700公吨/天(已是目前的最大运转能力)。
池式合成塔实际上是一种低高度尿素装置。然而,将冷凝器和合成塔结合在一个容器限制了扩容并受到运输约束,从而导致装置能力的限制。池式合成塔理念符合装置能力最大2300公吨/天的斯塔米卡邦标准。
目前为止,设计的池式合成塔装置的最大装置能力为1500公吨/天。然而,现今的尿素装置能力无一例外地超出3000公吨/天。对于这样的装置能力,不会考虑选择池式合成塔理念,至少目前不能。对于2300公吨/天以上的能力,池式冷凝器理念符合斯塔米卡邦标准。该理念中,除了决定合成塔规定总合成高度的池式冷凝器外,还具有立式合成塔。
3.3 进一步降低池式冷凝器尿素合成工段的高度
目前为止,已突出斯塔米卡邦汽提装置的两大优势。
1. 如本论文引言中所解释,无管内中压循环工段。
2. 使合成工段,至少是主循环,依靠重力流流动(第二循环将输送高压洗涤塔中的甲铵至合成中作进一步处理)。
在保持这些优势的同时解释斯塔米卡邦如何进一步降低池式冷凝器装置高度前,将讨论改造尿素装置在这方面的相关经验。
3.3.1 科威特石化工业公司科威特装置的改造
多年来,斯塔米卡邦已经积累了采用将合成塔安装在地面,改造尿素装置的经验。大约10年前,科威特石化工业公司科威特的传统斯塔米卡邦尿素装置曾被改造成二氧化碳汽提工艺(图8)。
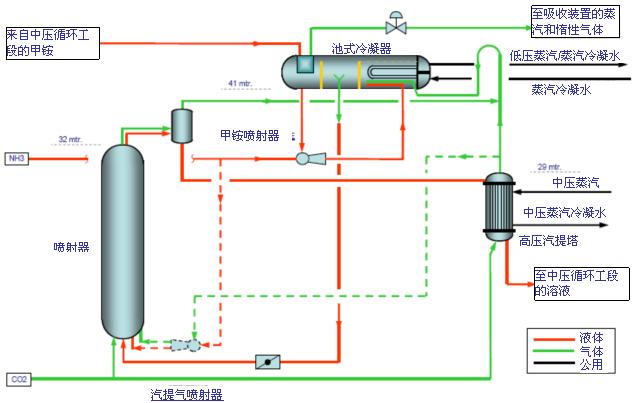
图8 改造后科威特石化工业公司科威特装置的尿素合成工段
改造理念即是将装置(1050公吨/天)改造成设计能力为1750公吨/天的二氧化碳汽提装置。这样做当然需要通过增加二氧化碳汽提塔和增加池式冷凝器(在一个容器中增加合成塔体积和高压冷凝能力)来实现。如所有传统尿素工艺一样,尿素合成塔是安装在地面上的,但这一理念并不使用高压液体喷射器将池式冷凝器的溶液送入合成塔(利用重力流优势)。
这可通过将池式冷凝器安装于现有合成塔顶上实现。
图8显示,高压汽提塔位置相对提高,事实上应尽可能高,使合成塔/顶部分离容器的尿素溶液能流入汽提塔中。因池式冷凝器的结构已经固定,汽提塔位置高能降低高压管道成本。
自科威特石化工业公司装置具有管内中压循环工段以来,在装置改造中采用了这种方案,以在改造中降低高压设备成本。这意味着所用改造理念是基于相对低的汽提效率的。
因此,直接来自压缩机的二氧化碳可用作蒸汽源向合成塔提供热量[2 因尿素生成反应为吸热反应,需要二氧化碳或NH3/CO2蒸汽进料以通过甲铵生成向合成塔提供热量,此为放热反应。旨在防止合成塔温度过低。]2。起初,这仅仅是用作蒸汽源。
如2004年斯塔米卡邦技术年会所提出的一样,因可疑的机械故障,中压冷凝器表现出过低能力。提出的解决方案是安装一个直接向合成塔输送汽提气的液氨驱动汽提气喷射器,留出空间以减少送至合成塔的二氧化碳的量。在2004年的技术年会上该喷射器还未投入运行,但现在已经成功。因此,多余的二氧化碳可用于汽提,增加了汽提效率,弥补了中压甲铵冷凝器性能表现的不佳。
今天,就科威特石化工业公司而言,最初的合成塔相对较长,约27米,为此,池式冷凝器的高度须相对较高。另一方面,若合成塔较短,池式冷凝器将位于较低高度,汽提塔的高度也同样降低。最终,这一理念中,池式冷凝器可安装于二氧化碳汽提装置中斯塔米卡邦池式冷凝器的正常高度,约22米,而汽提塔安装于地面,也为斯塔米卡邦汽提塔的正常高度。
这是此次改造的重要方面,有助于斯塔米卡邦新理念的发展。
3.3.2 池式冷凝器装置中位于地面上的合成塔
基于以上讨论的例子,很清楚,在商业化规模上证明可以使二氧化碳汽提装置中的合成塔位于地面上,同时维持合成回路中的重力流。这可以通过将池式冷凝器安装于立式合成塔顶上实现。
如前所述,斯塔米卡邦在池式冷凝器方面已经非常成功,其将高压甲铵冷凝器和尿素合成塔的功能结合在一个容器中。到目前为止,设计尿素装置时,下游合成塔位于池式冷凝器上,也能使池式冷凝器塔顶蒸汽进入合成塔。目前,斯塔米卡邦进一步采用这一举措发展出新的合成理念。该理念中,合成塔位于地面,池式冷凝器仍位于相同高度,但目前其位于合成塔之上。
这意味着池式冷凝器的塔顶蒸汽不能再进入合成塔。因此,将直接来自压缩机的二氧化碳用作向合成塔提供热量的蒸汽源。
然而,因池式冷凝器中产生大量尿素这一事实,立式合成塔中形成的尿素量有限,所需二氧化碳的量可保持低水平。此处一个重要特点是,池式冷凝器伴随绝热反应部分,降低了立式合成塔所需反应量。这方面在斯塔米卡邦的池式合成塔装置中证明是成功的。
池式冷凝器的塔顶蒸汽排放至简单中压吸收塔。多亏了零氧概念,因塔顶流量小,这可能实现。
新合成理念如图9所示。
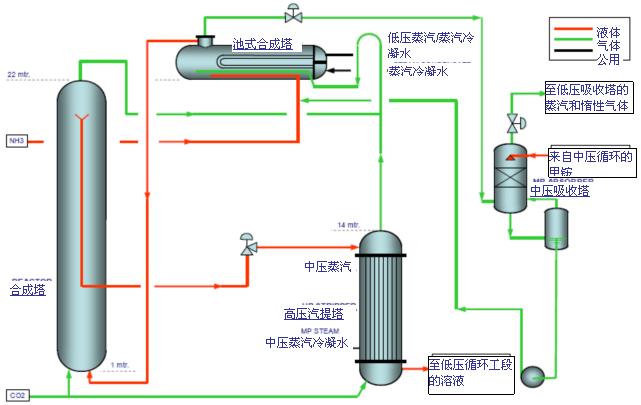
图9 斯塔米卡邦的新合成理念
因为合成塔加热所需二氧化碳的量有限,斯塔米卡邦新装置理念中可达到的汽提效率仍非常高,足以将汽提塔的液体排放至低压运行的循环工段,因此不需要管内中压循环工段。根据图9,池式冷凝器和合成塔与容器直接连通,因此池式冷凝器仅需位于合成塔之上几米以使池式冷凝器向合成塔溢流。第二依据是,合成塔顶部位置比汽提塔液体入口足够高,以使合成塔向汽提塔溢流。
在这一点上,很清楚,利用斯塔米卡邦的新合成理念满足本章引言中提出的挑战。
- 合成塔位于地面上(降低了总合成高度)。
- 主合成循环依赖重力流进行。
- 汽提塔的尿素溶液直接排放至低压循环工段。
图10显示了斯塔米卡邦装置历史上出现过的最高点轮廓线的延伸。
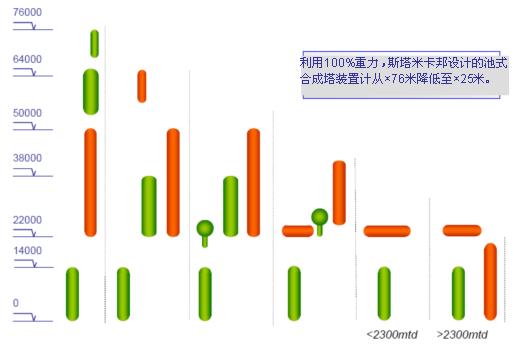
图10: 斯塔米卡邦合成高度再次进一步降低
利用新理念,斯塔米卡邦池式冷凝器合成工段的高度从39米下降至25米。
3.3.3 低位置合成装置总结斯塔米卡邦已经发展了低高度合成理念。这一理念具有以下特点。
• 合成塔安装于地面上。
• 池式冷凝器约保持最初高度。
• 汽提效率仍足够高至能将汽提塔的液体排放至低压运行的循环工段。
• 主合成循环仍依赖重力流实现。
4 全 图
结合本论文两个主题——零氧合成运行和低位置合成装置布置的效果,我们总结出斯塔米卡邦的新装置理念有以下几个特点。
使用最少的设备
- 省去了空气鼓风机。
- 省去了氢气转换器。
- 用简单中压吸收塔代替了高压洗涤塔和有关冷却系统。
- 省去了高压喷射器。
维护方便
- Safurex材料免维护。
- 合成塔安装于地面上。
- 所有设备易于接近。
运行可靠,运转周期最长。
- 合成循环依赖重力流进行。
- 装置下游、低压部分未改变工艺流程图。
- 内在安全的装置。
总的中压蒸汽消耗等于之前装置设计理念的蒸汽消耗,但为满足现场要求,可根据最佳汽提效率进一步减少。本论文附件中讨论了优化汽提效率这一主题。新装置理念中,如果使用了科威特石化工业公司改造项目中验证过的汽提气喷射器,汽提效率的优化必定是有空间的。建议在各具体基层尿素装置项目中宜进行汽提效率优化。
由于省去所需设备且合成位置低,再次降低了新斯塔米卡邦尿素装置理念的投资成本。
5 总 结
我们不断努力改善尿素装置的性能,现在斯塔米卡邦已经开发出低高度装置的理念,同时维持合成工段内主循环无故障重力流的理念。该新装置理念所用的所有工艺元素都在改造工程中得到了验证。
通过使用Safurex®结构材料,可进一步简化工艺设计,因为合成结构材料的钝化作用已成历史。因此,新装置理念是内在安全且免维护的装置理念。
总的来说,可得出这样的结论,通过这些新的工艺发展,斯塔米卡邦再次显示出其对尿素工艺设计发展的贡献——把客户需要放在首要位置。
• 低资本支出:不要为你的装置支付需支付费用以外的费用。
• 低运营支出:不要为你的装置支付需支付能量以外的能量。
• 高产品质量:保证客户无故障验收产品。
• 高安全标准:不存在氧气,无爆炸危险。
• 长运转周期:避免因非计划生产中断所致的生产损失。
• 低排放标准:确保您的“运营许可证”,与邻居保持友好关系!
附件:优化汽提效率
降低尿素装置的能耗咋看之下似乎并不困难。如果我们看到了图13中呈现的简化物料平衡和热量平衡图,我们需要做的便是降低流向高压汽提塔的中压蒸汽流,这会导致汽提效率更低。
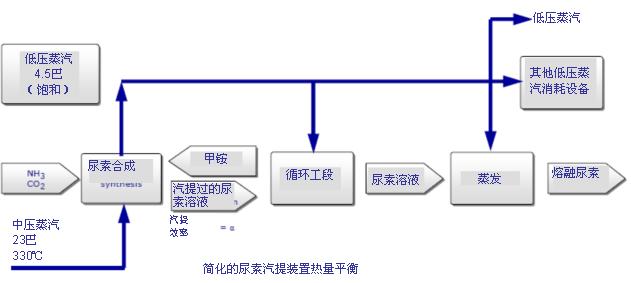
图13: 斯塔米卡邦尿素工艺简化的物料平衡和热量平衡
让我们更详细地观察一下,如以中压蒸汽形式引入合成工段的热量降低,比如1000 kW,会发生什么情况。因所需浓缩熔融尿素(至最后浓缩阶段)的总热量相同(作为第一近似值),因此,提供给循环工段的热量须增加至1000 kW。而且应观察到,因高压汽提塔中产生的汽提气的量减少了1000 kW,尿素合成工段中产生的低压蒸汽的量减少了相当于1000 kW的热量。因此,作为最终结果,尿素装置中输出的低压蒸汽的量将减少2000 kW(少产生1000 kW,多消耗1000 kW)。则存在副效应:如汽提效率降低,则甲铵循环增加。这对合成塔中可实现的转换具有不利影响。这将增加高压汽提塔中的中压蒸汽需求,部分抵消了最初减少的1000 kW等效中压蒸汽。而且,增加的甲铵循环将导致蒸发工段蒸发更多水,因此增加了该工段的低压蒸汽需求。作为整体结果,降低至汽提塔的热量输入(以1000 kW中压蒸汽形式)将导致尿素装置输出的低压蒸汽净减少(相当于2500-3000kW的热量)。
这是否为一种好办法得取决于现场的中压蒸汽与低压蒸汽的相对量。
许多装置设计中使用的低压蒸汽输出的一般去向是将低压蒸汽输入驱动二氧化碳压缩机的涡轮(图14)。
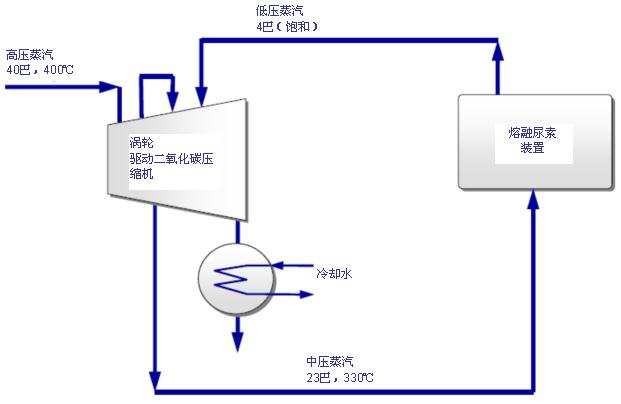
图14 用于二氧化碳压缩机涡轮的低压蒸汽
该理念中,使用高压蒸汽(通常为40巴,400℃蒸汽)驱动涡轮。压力级为23巴时,熔融尿素装置所需中压蒸汽从该涡轮获得。熔融尿素装置中产生的低压蒸汽进入该涡轮后端。通过向真空中排放部分高压蒸汽以平衡涡轮所需总能量。对于以大幅度减少低压蒸汽的产生量为代价来减少送到尿素装置的中压蒸汽,这是否为一种好办法,在该方案中不易检验。
这非常取决于若干边界条件,这边界条件仅能依靠涡轮制造商的配合密切才能界定,例如:
- 涡轮不同工段的效率。
- 涡轮的外形尺寸只允许有限量的低压蒸汽进入其后端。
- 因抽汽和进汽流量由熔融尿素装置决定,为涡轮实际速度控制留下的唯一参数为排至真空的高压蒸汽的量。为了能够对蒸汽速度进行恰当控制,该流量不可过低。
- 低压蒸汽进入涡轮后端影响到涡轮尺寸和真空冷凝器所需尺寸。因此,优化工艺中也应考虑到资本投资。
作为最终结论,我们声明,优化基层装置的汽提效率,仔细对经济参数进行仔细评估,并需要考虑技术限制。只有终端用户、工艺许可方、工程承包商和涡轮供应商的密切配合才能实现上述优化。达成一般性结论是不可能的;某些装置中优化出现‘高’汽提效率,而其他情况中‘低’汽提效率也许对装置运行公司更有利,这完全可能。