0 前 言
热钾碱脱碳工艺中溶液是关键,脱碳效率不仅与溶液的成分有关,而且还与溶液中机械杂质含量及溶液中各物质的稳定状态有关。实际生产过程中,由于溶液中的V5+常常被还原为低价钒,导致溶液中V5+浓度急剧下降,而一旦溶液中的n(V5+)/n(V4+)≤1,会造成系统的腐蚀。腐蚀后系统中的铁离子浓度急剧上升,形成钒铁共沉淀,导致管道和设备堵塞,使系统无法正常运行;还会出现溶液发泡,再生塔、碱洗塔拦液、带液,机泵打量不好等现象;同时溶液中的腐蚀杂质增多也会造成塔内填料、冷换设备结垢等。为了确保脱碳系统长周期满负荷运行,在调整好脱碳溶液组分的前提下,必须对相关的技术指标(如总铁、钒比、二乙醇胺等)进行严格控制,也就是对溶液进行强质过滤、氧化。现将我公司热钾碱脱碳溶液过滤、氧化部分近期的改造情况总结如下。
1 改造前的情况
原溶液过滤、氧化流程见图1。再生塔部分溶液(约5 m3/h)依靠位差进入水冷器,冷却后的溶液经过滤泵加压后进入过滤器顶部,过滤后的溶液返回再生塔。从再生塔底部通入一定量的工艺空气以氧化溶液。
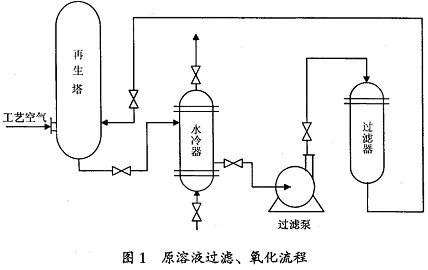
过滤器在运行中存在以下问题:由于溶液中杂质颗粒非常小,过滤效果差,过滤器出入口杂质含量变化不是很明显;清洗滤布时需要将过滤器大封头拆卸,工作强度大。该装置持续运行一段时间后,由于原料路线改变使得工艺条件发生了根本变化,停用了脱硫系统,气体带入溶液中的杂质减少了,故停用了机械过滤装置,改为静态沉淀,即每周将系统中10m3左右的溶液压入贮槽,静置1周后再打入系统。由于溶液中杂质颗粒小,沉淀效果差,加之脱碳系统只有2个贮槽可供溶液沉淀,无法定期进行清理,沉淀时间也有限,故沉淀后溶液中的机械杂质含量仍然较高。
再生塔加工艺空气氧化钒后,虽然系统腐蚀得到了缓解,但又出现了新的问题:再生二氧化碳气纯度下降,由原来的98%以上降为96.5%左右;再生气中氧含量增加,溶液脱氢能力增大,再生二氧化碳气中氢气、氮气等含量增加,造成尿素系统惰性气放空量增大,安全风险成倍增加;二乙醇胺快速降解[NH(CH2CH2OH)2+O2=4HCHO+NH3],使脱碳原材料消耗增加。
2 改造情况
2.1 改造方案
为彻底解决溶液系统的问题,经多方技术调研和技术论证,决定选用溶液微孔过滤、塔外低温氧化流程。
微孔过滤器由浙江温州东瓯微孔过滤有限公司提供,其关键元件微孔管是一种特殊塑料管,以超高分子量的聚乙烯塑料作为主要材料,再配以多种添加剂,经活化、改性、复合等特殊工艺制成。微孔管管径为38mm,管壁上均匀布满了超细微孔(孔径0.3~1.0 μm)。脱碳液进入过滤器后,依靠压力差迫使滤液流向微孔管。粒径小于微孔的物质穿越管壁后汇集到过滤液出口流出,粒径大于微孔的杂质被阻挡在管外,由渣料出口定期排出,从而实现溶液的过滤分离。微孔管工作一段时间后,管外壁上附着许多滤渣,导致阻力增大,过滤效率降低,此时可从反向冲洗口通入冲洗物(工艺空气或软水)反向冲洗,去除附着物,使微孔管得到再生。
该流程为旁路过滤方式,脱碳液处理量只占系统溶液量的3%左右,连续循环即可满足生产要求。微孔过滤也属机械过滤,不改变溶液原有成分,过滤管再生操作简单、快捷,过滤渣料可及时排出,能保证系统的连续稳定运行。
在高温下通入空气氧化会造成二乙醇胺降解。采用塔外低温氧化,在氧化槽内溶液温度由 110℃降为50℃后再通入空气氧化,溶液氧化效果好,二乙醇胺不易降解,氧化后的释放气直接放空,不带入生产系统。
2.2 实施情况
公司先对A套二次溶液增设塔外低温氧化、微孔过滤系统。改造后溶液过滤、氧化流程如图2。
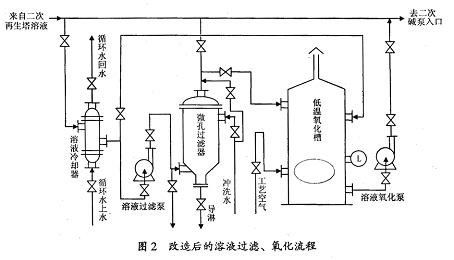
二次再生塔出口部分溶液(二次溶液总循环量的2%~3%)经溶液冷却器冷却、溶液过滤泵加压后进入微孔过滤器。过滤后的溶液一部分直接送往碱泵入口管;另一部分至氧化槽。氧化槽内液面维持在一定高度,工艺空气直接通入氧化槽内的空气分布器进行溶液氧化,氧化释放气经氧化槽顶部放空,氧化好的溶液经氧化泵送往碱泵入口。
微孔过滤器 PGK-60C型,P型微孔管,微孔过滤面积50m2,操作压力0.2MPa,操作温度<110℃,过滤量10 m3/h,过滤器直径 1200 mm,过滤器高度4100mm。
低温氧化槽 φ2200mm×12mm,高度 6000mm,空气分布器由φ38mm管制作,直径1200mm,管上钻φ3mm的孔,孔间距为35mm。
溶液冷却器 入口溶液温度105~110℃,出口溶液温度≤50℃,压力≤0.25MPa,换热面积12m2。
3 改造后的运行效果
(1)微孔管过滤器操作温度虽小于110℃,入过滤器溶液温度降为50℃后,过滤泵、过滤器运行周期延长,过滤效果更佳。
(2)塔外低温氧化、过滤系统投运后,二次溶液颜色恢复正常,钒及二乙醇胺的消耗明显减少,溶液中总铁含量降低,二次再生气纯度大幅提高。
改造前后部分参数对比见表1。
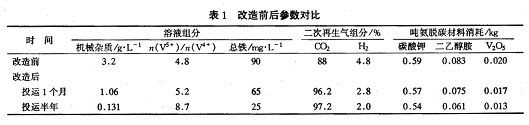
4 结 语
半年多的运行情况表明,脱碳溶液采用塔外低温氧化、微孔过滤流程能保证脱碳系统长周期满负荷生产,且脱碳材料消耗大大降低。1套低温氧化、过滤装置投资约15万元,仅减少脱碳材料消耗一项,2a内就可收回投资成本;并且装置投运后带来的隐形效益亦非常可观。我公司决定对A套一次溶液及B套溶液系统也增设塔外低温氧化、过滤装置,以彻底解决脱碳溶液系统存在的隐患。笔者认为:塔外低温氧化、微孔过滤装置值得在合成氨净化技术改造中推广。