湖南金信化工有限公司年产合成氨180kt,新、老两套的气体净化系统基本相同。它们将来自造气系统的半水煤气经过常压脱硫、中温变换、变换脱硫、中压脱碳四个工序净化后,再送回氢、氮压缩机四段。由于该系统的部分设备或工艺在运行中暴露出了一些不足,该公司近年来采用新技术、新材料、新工艺或新设备,分别进行了相应的改造,取得了可喜的效果。
1 以填料—旋流板改造变换气脱硫塔
1.1 问题的提出
金信公司净化老系统原有两台变换气脱硫塔,塔径2600mm,高24m,内装塑料阶梯环,采用ADA吸收法。在填料使用初期,脱硫效率较高,但随着硫堵现象的加剧,塔内压差增大,最高达25kPa,且脱硫效率平均不到85%。为此,每年不得不停车清塔2~4次,严重影响了系统长周期运行和后续工序生产。加上该塔已使用多年,腐蚀严重、塔壁出现裂纹,为确保安全生产,特别是解决硫堵问题,2001年公司决定对变脱塔进行更新改造。
1.2 改造概况
近年来旋流板技术应用于传质和除沫已有大量报道。经过技术考察,获知变脱塔采用旋流板脱硫,由于其开孔面积较大,阻力较小,能较好地解决硫堵问题,脱硫效率较低。为扬长避短,公司设计了一种以填料—旋流板为复合内件的新型变脱塔,并将塔径降到了2200mm。
新型变脱塔的结构见图1。塔下部为气体进入、分布装置;中部为三组双程传质旋流板及锥形溢流装置;塔上部设有一段塑料环填料;塔顶分别为ADA喷淋装置、单块除雾旋流板等。它们的主要作用如下:
①塔底部切向进气,并配置气体分布筒和筛液板,以增加气、液接触,提高脱硫效率;②由于塔径较大,旋流塔板采用了双程叶片结构,提高了开孔均匀度,使气液分布均匀、接触良好;③溢流装置采用新型螺旋叶片结构,它相当于半块旋流板,增加了气、液接触的机会,提高了脱硫效率,也提高了塔板的空间利用率;④塔上部仍设置一段填料层,利用填料脱硫效率高的优势,减轻了旋流板负荷,提高了整个塔的操作弹性和脱硫效率;⑤在顶层,液体喷淋采用易检修又防堵的宝塔型喷头,取代了阻力大、易堵又分布不均的螺旋喷头;⑥塔顶除采用旋流板除沫、喇叭管阻液外,合理选取了气体出口高度,达到了较好的除雾效果,减轻了塔后分离负担。
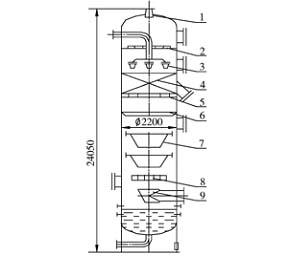
图1 填料—旋流板复合脱硫塔结构示意
1—喇叭阻液管;2—旋流除雾板;3—宝塔型喷头;4—塑料阶梯环;5—新型填料栅板;6—锥形引液圈;7—带溢流锥旋流板;8—多孔筛液板;9—气体进口分布筒
1.3 改造效果
①平均脱硫效率由改造前的不足85%提高到93%以上,出塔H2S含量由40mg/m3降到了15mg/m3以下,大大减轻了后续工序的压力;②生产能力得到大大提高,变换气处理量由原来的30000m3/h提高到34000m3/h,系统提压到2.1MPa后则提高到41000m3/h;③塔阻力降低,最高阻力由原来的25kPa下降到4.0kPa。④硫堵现象大为减轻,原来每年需停车检修清洗2~4次,改造后达到了两年尚不需清洗、检修,为系统的长周期运行创造了良好条件;⑤经测算,本项改造年综合效益为90万元以上。
2 新型安全熔硫釜的设计与应用
2.1 原熔硫釜基本情况
净化系统原有2台相同型号的间歇式熔硫釜,它们将系统脱硫而析出的膏状单质硫熔融成硫磺产品。原设计利用硫膏在140~180℃的熔融状态下,其杂质可以悬浮分离的特性,将低压蒸汽(P≤0.4MPa,T≈150℃)作为热源,引入到熔硫釜内,熔炼硫磺。两台设备在此条件下安全、正常运行了7年多。由于热媒温度与硫膏下限温度接近,致使熔炼时间较长,并且易造成杂质分离不彻底。为此,公司将热媒改造为过热蒸汽(P=0.5MPa,T≈250℃)。改革后,釜内温度可达180℃,熔融时间大为缩短,同时产品质量明显改善。
但是,热源改造后,熔硫釜上封头部位却因变形,使入料口接管在与上封头结合处呈喇叭形向外扩张,并伴有封头鼓涨。至2002年3月,因变形相当严重而不得不停用熔硫釜。
2.2 失效原因分析
在排除了设计、制造、安装环节的过失而引起熔硫釜失效后,根据计算得知,引起上封头屈服失效的压力最小值为2.6MPa,故操作条件的更改也不是失效原因(180℃的蒸汽压约为1.0MPa)。那么,如此高的破坏性压力源自何处呢?
经过调查、分析,发现失效的原因在于热源改造后的满釜操作,即硫膏原料充满容器。因为满釜操作下,不断加热的硫磺膨胀所需的体积有时会大于间歇排汽所留下的体积,这种情况一旦发生,釜内物料体积不断增大和膨胀,将有可能形成大于2.6MPa的膨胀压,从而引起釜体屈服失效。由于釜体上封头部位存在最大开孔(Dg400),且依靠封头壁厚补强,因此该最薄弱部位首先失效。同时热媒改革前熔硫效率较低,不会满釜操作,不产生超压,故能安全运行。
2.3 新型安全熔硫釜的设计
全新设计的熔硫釜见图2。为确保压力容器的安全,作如下结构设计。
(1)新设料位自限装置。从分析可知,要防止熔硫釜的屈服变形,必须禁止满釜操作,即必须有效控制物料的加入量。为此,特别设计了如图2上封头部位的料位自限装置。
进料时,打开管口f排气,硫膏从管口d进入;当料位到达A-A面时,其上部空间被空气占领,液位不再上升,如果此时熔硫釜原料贮斗内还剩有物料,它将由d管口流入f管口,直至排出。这样,实现了物料加入量的自动限定。
熔硫时,关闭d、f管口,随着温度升高,釜内压力增加,适时打开f管口排气。只要限位空间(即料位高度)设计适当,因空气和部分水的排出而留下的空间,将足以包容硫膏膨胀所增长的体积,以避免超压失效,从而确保设备安全运行。
(2)配合设置溢流装置。在A-A面配对设置溢流排放口,当釜内料位处于A-A临界面时,打开溢流口,可迅速排料到位,并能消除f管口积料堵管;
(3)设置压力、温度指示。该设计在进料时若管口k、p等密封失效,而出现假料位自动控制的危险工况时,作用更大。
(4)增设安全阀,成为熔硫釜最后一道安全屏障。
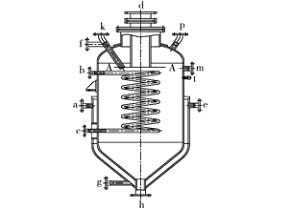
图2 新型熔硫釜结构示意
a—夹套蒸汽入口;b—盘管蒸汽入口;c—盘管蒸汽出口;d—人孔、硫膏加料口;e—夹套排气口;f—釜体排气口;g—冷凝液出口;h—熔融硫、杂质出口;k—压力表接口;m—溢流口;p—安全阀接口;t—温度计接口
2.4 应用效果
开发设计的新型安全熔硫釜于2002年7月投入系统使用。该装置运行正常,操作简便,不仅彻底消除了安全隐患,而且硫磺质量良好、熔硫效率较高,达到了公司设计要求。原熔硫釜月产硫磺50t左右,新装置平均月产70t,最高时达100t,同时硫磺产品的一、优等品率也有所提高。
3 脱碳液采用高分子微孔精密过滤
3.1 改造前基本情况
金信公司的气体脱碳工序采用改良DEA循环脱碳工艺。其脱碳液的主要技术参数为:①成分 K2O 210g/L、KVO3 8g/L,DEA 22g/L;②循环量 520m3/h;③温度 ≤110℃;④杂质粒度 <50μm;⑤杂质含量 <5g/L。
脱碳液吸收CO2后,经过再生处理成为脱碳再生液(亦简称脱碳液),再投入脱碳系统使用前,必须过滤。原装置采用传统的活性炭吸附提纯,它存在三大不足:①过滤效果不佳、效率较低,且易饱和失效,因而填料更换频繁(每年必须更换一次);②在新填料使用初期,脱碳系统易出现不稳定现象;③受过滤能力限制,净化系统气体处理量受到制约。总之,脱碳液采用活性炭过滤,工作时脱碳效果不好、效率较低,制约系统生产的稳定和净化能力的提高。
3.2 改造概况
为解决脱碳液过滤的问题,该公司经过技术招标,采用了浙江温州东瓯微孔过滤有限公司提出的改造方案,即以刚性高分子微孔精密过滤工艺取代原活性炭过滤。
刚性高分子微孔精密过滤的关键元件——过滤介质,是一种微孔管,它是一种聚乙烯管,经活化、改性、复合等特殊工艺而制成。其管径通常为φ30~80mm,管壁上均匀布满了超细微孔(可达0.3~1.0μm)。工作时,脱碳液进入过滤器,依靠压力差,迫使滤液流向微孔管此时,粒度小于管孔的物质穿越管壁后汇集到过滤液出口流出,大于管孔的杂质被阻挡在管外由渣料出口定期排出,从而实现溶液的过滤分离。微孔管工作一段时间后,其管外壁上将附着许多滤渣,为稳定过滤效果,可从反向冲洗口或正向冲洗口通入冲洗物,将微孔管反向或正向冲洗(反向冲洗为主),以去除附着物,使微孔管再生。再生后,又可进行溶液过滤,如此循环……
该流程为旁路过滤方式,脱碳液处理量只占系统流量的一部分;改造中,根据脱碳液过滤特性试验选取了合适的微孔过滤参数;由于介质温度达110℃,为延长微孔管使用寿命,采用先冷却再过滤方案;为克服阻力,并提供过滤液压差,配置了管道泵;设计了空气和软水接口,当微孔管需要再生时,用空气或软水分别反吹(洗)或正吹(洗),使其再生。
3.3 改造结果
(1)微孔管过滤效果很好。经测试,过滤精度达0.3~0.5μm,而且均匀、稳定;杂质分离率可达97%以上,比活性炭高出20%以上;系统杂质平均下降速度是活性炭的3倍多。它们完全能满足脱碳液澄清过滤的要求,投运后系统脱碳液能在较短时间达到清彻透明的理想状态。
(2)操作方便,系统生产稳定。该过滤属于物理过滤,不改变溶液原有成分,也不存在吸附损耗问题,且过滤管再生操作简单、快捷,再生效果可恢复如初,因此避免了活性炭过滤易饱和失效的难题;同时,过滤物渣料可及时排出,保持了系统生产(能力)的连续稳定;此外,关键部件——微孔管虽然为易损件,但具有较好的耐腐蚀性及抗老化特性。装置投运三年多以来,尚未作任何检修,表明其使用寿命较长。
(3)经济性较好。由于微孔过滤效果明显优于活性炭,系统中脱碳液杂质含量可以快速降低并持续保持在较低值,因此大大地提高了脱碳液工作时的吸收效果,在确保系统稳定的同时,提高了气体处理能力。经测算,该技术的应用可提高生产能力1%,加上每年可节约活性炭6t,则年新增收益在26万元以上,不到一年可收回投资。
4 开发折流杆式薄管板净化气水冷器
4.1 原净化气水冷器的概况
净化气水冷器(简称水冷器)的作用是降低CO2吸收塔出口的净化气温度,以利分离器除沫,从而保证出系统净化气合格。原1#水冷器为典型的立式管壳式换热器,DN1000,水走管程,净化气走壳程,并在进、出口处设置外导流筒,折流板为盘环式。该型换热器往往运行不到1年就开始内漏,主要表现为管板与换热管之间的焊缝裂纹泄漏;使用2年之后,换热管开始穿孔内漏,且频次越来越高。它们除造成频繁的停车检修外,还流失了大量的净化气。
4.2 水冷器泄漏的原因分析
分析认为,管板与换热管焊缝开裂,是由于温差交变应力和管束振动的共同作用导致焊接缺陷扩展的结果。该换热器管板为25#钢,可焊性较差,易出现焊接缺陷;而壳体与换热管温差较大,2个外导流筒难以补偿其膨胀差;加上使用中,频繁的开停车、负荷波动以及管束振动导致焊缝开裂而泄漏。
根据考察及计算得知,造成换热管穿孔的原因是由于折流板设置不当,出现管束振动,使管子不断撞击折流板,产生腐蚀穿孔而泄漏。
4.3 设计新型高效水冷却器
为解决原水冷器存在的问题,参考国内外换热器设计的最新成果与经验,针对性地设计了新型水冷器(见图3),它具有以下结构特点。
(1)管壳程介质不变。因用户冷却水水质较差,为便于清污除垢,仍安排水走管程,但将原单管程改为双程,以增加流速,减少污垢沉积,并提高传热系数。
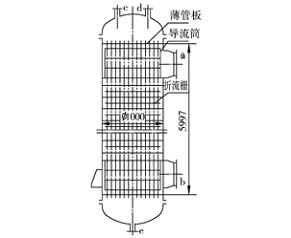
图3 新型净化气水冷器示意
a—气体进口;b—气体出口;c—水进口;d—水出口;e—排污口
(2)管束采用折流杆(栅)支承。折流栅由交叉垂直的折流杆和环板组焊而成,它能有效减轻诱导振动、降低管束磨损、延长设备使用寿命。此外,折流杆换热器的壳程阻力降比普通型减少30%左右。
(3)薄管板设计。该型换热器在国已有相当的设计经验,对于折流杆支承的换热器,由于其固定作用好、管束振动小,采用薄管板十分安全、可靠。为避免法兰力矩对管板的影响,并便于制造,本薄管板采用焊入式。
(4)设置简易导流筒。原导流筒与壳体对接,属承压元件,较为复杂,成本较高。本设计将管束的拉杆放在最外圈,利用折流栅环板所占的环隙空间设置δ=3的简易导筒,既简单又经济。
(5)合理选用管、壳程材质。设计中,温度较高的壳程选用碳钢,较低的管程则用不锈钢,利用不锈钢和碳钢线膨胀系数的差别,较好地避免了因管、壳程膨胀差引起的温差应力,并不再设置膨胀节。既满足了使用要求,又降低了制造成本。
(6)换热管采用横纹槽管。由于横纹槽管可产生“二次流”和“边界层分离”效应,因此不仅可强化传热(传热系数可达光管的2倍以上),而且其抗污性能高于光滑管。
4.4 应用效果
开发设计的第一台以折流杆、薄管板、横纹槽管、简易导流筒等为特征的净化气水冷器于2003年4月投入系统运行,经测定气体出口温度比以前下降了10℃,至今未发生内漏和管束振动现象。不久,第二台DN1400净化气水冷器,也取得了同样满意的应用效果。它表明这种新型的换热器不仅成功抵御了流体振动的破坏,大大提高使用寿命,而且具有高效、不易结垢的特点,为净化系统的经济运行创造了重要条件。
5 总结
针对合成氨净化系统的部分设备或工艺存在的问题,分别进行的创新改造,取得了圆满成功,它展示了科技创新在企业技术进步、效益提高中的旺盛生机。
