1 高分子微孔精密过滤技术概述
1.1 液体精密过滤及其存在的问题
化工生产很多场合涉及液固分离,包括沉降和过滤分离两大类。由于前者要求液固两相必须有一定的密度差,而后者不受限制,因此过滤分离应用较广。液固过滤分为粗级过滤(>100μm)、亚精密过滤(100~10μm)、精密过滤(10~1μm)、超精密过滤(1~0.1μm)、超滤、纳滤及反渗透(<0.1μm)。对于大多数化工液体而言,须要进行精密过滤。
目前,对大于10μm的粗级过滤与亚精密过滤,采用非金属、金属滤布或滤网作过滤介质的间歇或连续过滤机可满足要求。精度要求小于1μm的液体过滤,采用有机或无机微孔膜也可获得较好效果。但应用最广泛的精密过滤却存在如下问题,而成为最薄弱的过滤操作。
10~1μm的液体精密过滤,包括可形成滤饼层的“液体精密滤饼过滤”和不形成滤饼层的“液体精密澄清过滤”。当前,精密滤饼过滤的介质大多采用整体型的用作亚精密过滤的滤布、滤网或滤毡。它存在两大不足:(1)过滤前期,小于10μm的微粒会穿漏,只有进行反复循环,待10μm左右的微粒形成一定厚度的滤饼,过滤精度才逐渐达到要求,即过滤效率较低;(2)由于滤布或滤网为非刚性,对较黏细颗粒形成的滤饼难以简便卸除。作为精密澄清过滤的介质,分为整体型和分散型两类。整体型一般是较厚的烛型滤芯、滤毡或滤板,它们常因难以有效再生而需要频繁更换,由于消耗大量的滤材,成本较高。分散型滤材有颗粒与长纤维两种,它们均可再生而反复使用,但也存在两大不足,一是其孔隙内易产生板结现象,导致过滤时产生沟流,严重影响过滤效率;二是由于过滤介质的孔隙率大,细颗粒很容易穿滤出去,因而过滤质量不稳定。
1.2 新型高分子微孔精密过滤技术
为解决液体精密过滤存在的不足,我国科技工作者开发了以刚性高分子材料为过滤介质的微孔过滤技术,目前已形成硬件(高分子微孔烧结过滤管及精密过滤机的制造)与软件(过滤物料的性能测试、过滤设计计算)都比较成熟的新型液体精密过滤技术。
该技术的核心元件——过滤介质,是一种以烧结聚乙烯为原料的高分子微孔管, 经过活化、改性、复合等特殊工艺而制成,其管壁上充满了毛细小孔,平均孔径为2~140μm,过滤精度为0.5~1μm。微孔管具有刚性,可耐外压0.2~0.5MPa,耐内压0.4~1MPa。
高分子微孔精密过滤的基本原理是:利用微孔管正向过滤,反向冲洗、再生(见图1)。工作时,待过滤物流向微孔管,其中的固体杂质微粒被微孔管捕捉,在管外形成滤渣定期排出;过滤液穿越微孔管后,汇集到出料口流出,从而实现溶液的过滤分离。当微孔管堵塞严重时,可暂停过滤,从反向冲洗口或正向冲洗口通入清洗物,将其冲洗(反向冲洗为主),微孔管再生后继续过滤……
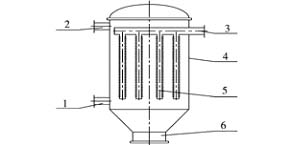
图1 刚性高分子微孔精密过滤原理
1—过滤液进口;2—正向冲洗入口;3—过滤液出口(反向冲洗入口);4—过滤机外壳;5—微孔管;6—渣料出口
1.3 高分子微孔精密过滤的特点
它的主要优点如下。
(1)过滤效率高。最小可过滤0.5μm微粒,过滤效率可大于99.9%。
(2)卸除滤饼简便。对滤饼进行快速反吹,可很方便地、轻松地卸除。
(3)再生效率高。应用反吹法可对微孔管进行高效、简单的物理再生,微孔管可长期使用。
(4)耐腐蚀性能好。微孔管耐酸、碱、盐及大部分有机溶剂。
(5)维护检修方便。过滤机结构较简单,微孔管相对密度小,维护与检修容易。
(6)动力消耗小。过滤压差小于0.3MPa,动力泵消耗较低。
(7)占地面积少。大部分过滤机为立式,单位过滤面积占地较少。
(8)自动化程度较高。过滤机如配以自动阀门与控制装置,可以达到全自动或半自动操作。
(9)适应性广。PG型微孔过滤机已有多种结构系列,可适应各种工况的液体精密过滤。
(10)工作环境好。过滤为密闭操作,生产场地清洁、卫生。
新型高分子精密过滤的主要缺点有:(1) 微孔管不耐高温,最高不超过120℃(但大量的化工液体过滤时不超过100℃);(2)滤饼干度不及板框式压滤机与三足式离心机。
1.4 过滤工程的基本设计计算
为了正常发挥新型液体精密过滤技术的功效,应用前必须进行物料过滤性能测试与物料平均滤速的计算。按照宋显洪[1]等提出的计算公式,计算方法如下:
(一)液体精密滤饼过滤的平均滤速按公式(1)~(3)计算
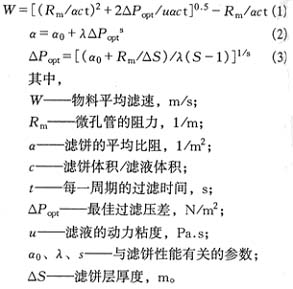
求得平均滤速W,再根据工程所需的过滤液流量,即可算出所需的过滤面积。由滤液流量、过滤面积、最大滤饼厚度等即可确定微孔精密滤饼过滤机的各种参数及相关尺寸。
(二)液体精密澄清过滤的平均滤速按公式(4)计算
W=b/(t-a) (4)
式中, t——每一周期内的过滤时间,s;
a、b——与物料内微粒性质、浓度及t值有关的参数,可通过小型试验测定。
同理(一),得出物料平均滤速后,即可由流量计算所需过滤面积,再选取微孔精密澄清过滤机相应的规格参数。
2 合成氨净化系统采用高分子精密澄清过滤技术改造
2.1 应用微孔精密过滤技术改造脱碳液过滤系统
湖南金信公司年产合成氨180kt。其气体净化系统的脱碳工序采用改良DEA循环脱碳工艺,该脱碳液的主要技术参数为:①成分:K2O 210g/L,KVO3 8g/L,DEA 22g/L;②循环量:520m3/h;③温度:≤120℃;④杂质粒度:<50μm;⑤杂质含量:<5g/L。原装置对于脱碳液吸收CO2再生后的杂质精密过滤,采用传统的活性炭介质吸附提纯的工艺。活性炭规格为φ2~3mm,长10mm左右的小颗粒,属于分散型过滤介质的精密澄清过滤,存在的弊端如下。
①过滤效果不佳,效率较低。由于活性炭介质经一定时间的过滤后,孔隙内截留了相当数量的精细微粒,此时活性炭颗粒介质容易产生板结或结块现象,导致过滤时发生沟流,严重影响过滤效率,其平均杂质去除率通常在70%左右。
②过滤质量不稳定。由于活性炭深层过滤介质的孔隙率较大,且不均匀,细颗粒杂质如硫、尘埃、催化剂粉末、腐蚀铁屑等很容易穿滤出去,它们易造成脱碳液表面活性能力降低,引起溶液发泡,严重时导致CO2吸收塔带液、泛塔的事故,致使脱碳工序不稳定。
③易饱和失效。活性炭吸附杂质后,1年左右就饱和失效。由于有效使用时间较短,填料更换频繁,不仅检修和更换费工、费时、不方便,而且由于专用活性炭填料价格较贵,增加了系统运行成本,故经济性差。
④制约系统生产。由于活性炭过滤效果较低,质量不稳定,很难达到工艺要求,系统脱碳液杂质含量长期维持在较高值,导致CO2吸收塔的工作效率较低,制约了净化系统的气体处理能力,不能与压缩机系统的出气量相适应。
为解决活性炭法过滤脱碳液存在的问题,金信公司经过技术招标,采用了高分子微孔精密过滤工艺取代原活性炭过滤工艺。过滤改造后的工艺流程见图2。该流程为旁路过滤方式,设计过滤流量为12m3/h,即逐步完成系统脱碳液的清洁工艺;改造中,根据脱碳液过滤特性试验、计算,选取了合适的微孔管及过滤机型;因工艺脱碳液温度接近120℃,虽然采用了耐高温的PA型微孔管,为延长其使用寿命仍采用了先将脱碳液冷却到100℃再过滤的方案(因旁路过滤量很小,对系统脱碳液温度影响可以忽略);为提供过滤液压差,配置了小型管道泵;设计了空气和软水接口,以满足微孔管再生需要。
脱碳液过滤改造取得了良好的效果,主要表现在以下几个方面。
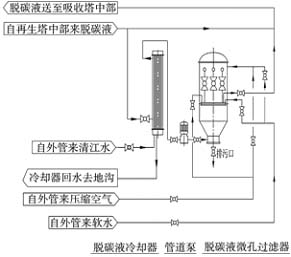
图2 脱碳液高分子微孔精密过滤工艺流程示意
①微孔过滤效果很好。过滤精度达0.3~0.5μm,分离效果可达97%以上,能满足脱碳液澄清过滤的要求。投运后,系统脱碳液能在较短时间达到清彻透明的理想状态。其运行情况见表1。
②操作方便,系统生产稳定。该过滤属于物理过滤,不改变溶液成分,也不存在吸附损耗,且过滤管再生操作简单、快捷,再生效果可恢复如初,因此有效地解决了活性炭过滤易饱和失效的难题;由于脱碳液过滤后,品质好、质量稳定,满足了澄清过滤要求,杂质得到有效去除,消除了脱碳液发泡现象,避免了吸收塔带液、泛塔的事故,并且再生操作就地处理、简单快捷,过滤物渣料可及时排出,因此保持了系统生产的连续稳定,为净化系统的长周期运行创造了重要条件;此外,关键部件——微孔管虽然为易损件,但具有较好的耐腐蚀性及抗老化特性,精密微孔过滤机投运三年多以来,尚未作任何检修,表明其使用寿命较长。
表1 脱碳液过滤效果、效率对比(新、老系统统计平均值)

③经济性较好。由于微孔过滤效果明显优于活性炭,系统中脱碳液杂质含量可以快速降低并持续保持在较低值,因此大大地提高了脱碳液工作时的吸收效果,在确保系统稳定的同时,提高了气体处理能力。改造后,脱碳工序的气体处理能力提高了1%以上,分别达到了与合成氨气体压缩系统出气量43000m3/h、47000m3/h相适应。加上每年可节约活性炭6t,经测算,年新增收益在26万元以上,不到一年即可收回投资。
2.2 采用微孔精密过滤器改造铜氨液过滤系统
金信公司合成氨原料气体中的CO等杂质,经中压变换、甲醇合成吸收后,最后在净化系统铜洗工序的铜洗塔内由铜氨液循环洗涤、吸收去除。铜氨液的主要工艺技术参数为:①成分Cu 2.2~2.5mol/L,NH3 10~13mol/L,HAc 2.2~2.5mol/L;②温度≤40℃;③循环量54m3/h;④杂质粒度<50μm;⑤杂质含量<5g/L。原装置对于铜氨液吸收CO还原、再生后的杂质精密过滤,采用丝瓜络作为过滤介质,也属于分散型过滤介质的精密澄清过滤,存在的弊端如下。
①过滤效果较差、效率较低。进铜洗塔铜氨液的品质长期不能达到铜洗系统对铜氨液的要求,因此严重制约了铜氨液对气体杂质的吸收效果,即限制了该系统的气体净化处理量。
②易引发事故。在丝瓜络使用初期,因其中含有较多的灰尘,加剧了铜氨液污染的程度。铜氨液不干净,除了降低铜洗塔的吸收效果外,还易引起铜氨液发泡:一方面,如系统操作不理想,将引起铜氨液再生不完全,当铜氨液循环进入铜洗塔工作时,会使吸收效果更差;另一方面,铜氨液发泡易发生出铜洗塔净化气带液的现象,已多次引发压缩系统的设备毁坏、氨合成系统的催化剂寿命缩短、氨产品产量降低、质量下降等严重事故。
③使用寿命较短、更换很不方便。丝瓜络使用较久后,大量的油渍附在其表面上,既造成饱和失效,又使阻力大增,故每年必须更换丝瓜络。由于更换时必须停车、开罐,并手工取装,不仅费力费时,而且检修现场卫生状况很差。
④过滤效果不能适应铜洗塔内件改造后的要求。原铜洗塔内件为鲍尔环散堆填料,由于传质效率较低,导致铜氨液流量大,能耗高,气体处理能力受限,为节能降耗、提高铜洗系统生产能力,该公司于2003年将铜洗塔内件改造成了新型、高效规整填料。因为规整填料的波纹板片之间的间隔较小,如铜氨液较脏,很容易发生堵塞现象,使气体偏流,造成铜氨液吸收率下降、系统阻力增加。虽然铜洗塔改造后的铜氨液分布器具有较好的自过滤、沉积杂质的能力,但要使规整填料不被堵塞并长周期运行,进塔铜氨液质量指标要求必须远高于散堆填料,而丝瓜络过滤器很难达到要求。
为克服丝瓜络过滤的严重不足,金信公司经过技术招标,采用了温州东瓯微孔过滤有限公司提出的改造方案,即将原丝瓜络过滤器更换成高分子微孔精密过滤器,过滤改造后的工艺流程见图3。该工艺也采用了旁路过滤,设计过滤流量为5m3/h,以逐步完成系统铜氨液的清洁;根据铜氨液特性试验选取了合适的微孔管及其过滤机;为提供过滤压差,配设了小扬程管道泵;还配置了空气和稀氨水接口,用于再生微孔管。
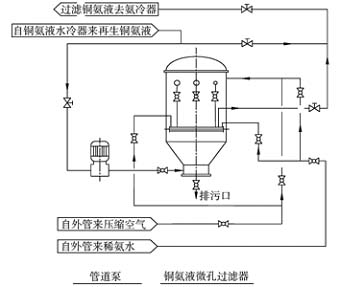
图3 铜氨液高分子精密微孔过滤工艺流程示意
1、2#铜氨液过滤器与铜洗塔改造同步配套完成,总投资42万元(其中过滤器16万元), 改造效果显著,如下所述。
①过滤效果好,效率高(见表2)。微孔管过滤粒度可达0.3~0.5μm,分离效果可达90%以上,系统杂质含量下降明显加快,满足了铜洗塔规整填料改造后对铜氨液更高的品质要求,为提高铜洗塔的吸收效果、增加其气体净化能力创造了重要的条件。
②出口铜氨液不发泡。由于微孔过滤后铜氨液非常清洁,未再引发铜洗塔带液和再生系统运行不正常的事故,消除了安全隐患。
③操作方便。过滤管再生时就地处理,不需拆卸设备,方便快捷、操作简单,经过再生处理后,过滤效果可恢复如初。与此同时,过滤物渣料可及时排出,能保持系统生产的连续稳定。
④使用寿命较长。由于不需更换过滤材料,且关键部件——微孔管已运行3年多尚不必更换,故检修周期明显增长。
⑤经济效益好。该改造与铜洗塔规整填料改造同步竣工后,由于进铜洗塔铜氨液质量和铜洗塔传质效率的大幅提高,使铜氨液吸收CO效率也显著提高(表3),在提高了铜洗系统生产能力的同时,取得了显著的节能降耗效益,每年直接效益达220万元,不到3个月即收回了改造投资。
表2 铜氨液过滤效果、效率对比(1、2#系统平均值)

表3 φ1000mm铜洗塔改造前(2001年5月)、后(2004年5月)工艺统计数据对比

3 总结
新型刚性高分子微孔液体精密过滤技术,是对传统的精密过滤技术的重大革新。其过滤效率高,过滤管再生方便,操作简单,使用寿命长,在合成氨净化系统中应用,只要选型适当、设计合理、操作规范,可取得良好的节能降耗效果。
