信化工有限公司合成氨生产能力为 180kt/a,有新、老两套工艺流程基本相同的气体净化系统,包括:常压脱硫、中温变换、变换脱硫、中压脱碳四个工序。近年来,该公司针对净化系统运行中暴露出的部分设备或工艺问题,通过采用新技术、新材料、新工艺或新设备进行相应改造,取得了可喜的效果。
1 应用精密微孔过滤技术改造脱碳液过滤
1.1 改造前情况
金信公司的气体脱碳工序采用改良DEA循环脱碳工艺。其脱碳液成分为:K20 210 g/L。, KV03 8g/L,DEA 22g/L;循环量:520m3/h;温度:≤110℃;杂质粒度<50μm,杂质含量<5g/L。脱碳液吸收CO2后,经过再生处理成为脱碳再生液(亦简称脱碳液),再生液在投入脱碳系统使用前必须过滤。原装置采用传统的活性炭吸附提纯,脱碳效果不好、效率较低,制约了系统生产的稳定和净化能力的提高。
1.2 改造概况
为解决脱碳液过滤的问题,经过技术招标,采用了浙江温州东瓯微孔过滤有限公司提出的改造方案,即以精密微孔过滤工艺取代原活性炭过滤。该精密微孔过滤器的关键元件微孔管是聚乙烯管经活化、改性、复合等特殊工艺制成。其管径通常为φ(30~80)mm,管壁上均匀布满了超细微孔(可达0.3~1.0μm),工作原理如下。
脱碳液进入过滤器后,依靠压力差,迫使滤液流向微孔管。此时,粒度小于微孔的物质穿越管壁后汇集到过滤液出口流出,大于微孔的杂质被阻挡在管外,由渣料出口定期排出,从而实现溶液的过滤分离。微孔管工作一段时间后,可从反向冲洗口或正向冲洗白通人冲洗物,将微孔管反向或正向冲洗(反向冲洗为主),以去除附着物,使微孔管再生,以确保过滤效果。
过滤改造后的工艺流程见图1。该流程为旁路过滤方式,脱碳液处理量只占系统流量的一部分。微孔过滤参数通过脱碳液过滤特性试验确定。由于介质温度达110℃,为延长微孔管使用寿命,采用先冷却再过滤方案。为克服阻力并提供过滤液压差,设计、配置了管道泵及空气、软水接口,再生时用空气或软水分别反吹(洗)或正吹(洗)。
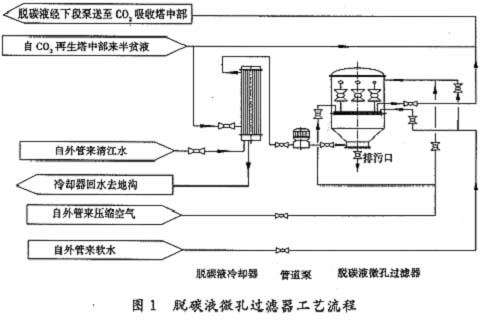
1.3 改造结果
(1)过滤效果好,过滤精度达0.3~0.5μm,分离效率可达90%以上,脱碳液能在较短时间达到清澈透明。系统运行情况参见表1。

(2)操作方便,系统生产稳定。该过滤属物理过滤,不改变溶液原有成分,也不存在吸附损耗问题,且过滤管再生操作简单、快捷,再生后的脱碳效果可恢复如初,因此避免了活性炭过滤易饱和失效的问题;同时,过滤渣料可及时排出,保持了系统生产(能力)的连续稳定;此外,关键部件——微孔管虽然为易损件,但具有较好的耐腐蚀性及抗老化特性,装置投运3a多,尚未作任何检修,使用寿命较长。
(3)经济性较好。由于微孔过滤效果明显优于活性炭,系统中脱碳液杂质含量可以快速降低并持续保持在较低值,因此大大地提高了脱碳液工作时的吸收效果,在确保系统稳定的同时,提高了气体处理能力。经测算,该技术的应用可提高生产能力1%,加上每年可节约活性炭6t,年新增收益在26万元以上,不到1a可收回投资。
2 开发新型折流杆式薄管板净化气水冷器
2.1 原净化气水冷器存在的问题及原因
净化气水冷器(简称水冷器)的作用是降低 CO2吸收塔出口的净化气温度,以利分离器除沫,从而保证出系统净化气合格。原1#(DNl 000)水冷器为典型的立式管壳式换热器,水走管程,净化气走壳程,进出口设置有外导流筒,折流板为盘、环式。该换热器运行不到1 a就开始内漏,主要为管板与换热管之间的焊缝裂纹泄漏;使用2 a后,换热管开始穿孔内漏,且频次越来越高。分析认为,管板与换热管焊缝开裂是由于温差交变应力和管束振动共同作用下焊接缺陷扩展的结果;造成换热管穿孔的原因是折流板设置不当,出现管束振动,使管子不断撞击折流板,产生腐蚀穿孔而泄漏。
2.2 设计新型高效水冷却器
为解决原水冷器存在的问题,参考国内外换热器设计的最新成果与经验,设计了如图2的新型水冷器。
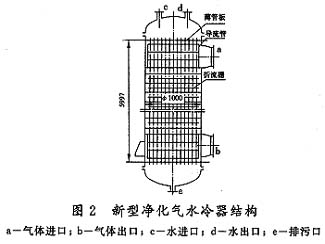
(1)管壳程介质不变。因用户冷却水水质较差,为便于清污除垢,仍安排水走管程,但将原单管程改为双程,以增加流速,减少污垢沉积,提高了传热效率。
(2)管束采用折流杆(栅)支承。折流栅由交叉垂直的折流杆和环板组焊而成,能有效减轻诱导振动,降低管束磨损,延长设备使用寿命,换热器壳程阻力较普通型换热器降低30%左右。
(3)薄管板设计。该型换热器在国内已有相当的设计经验,由于其固定作用好、管束振动小,十分安全、可靠。为避免法兰力矩对管板的影响,且便于制造,薄管板采用焊入式。
(4)设置简易导流筒。原导流筒与壳体对接,属承压元件,既复杂成本又高。本设计将管束的拉杆放在最外圈,利用折流栅环板所占的环隙空间设置厚度为3mm的简易导筒,既简单又经济。
(5)合理选用管、壳程材料。温度较高的壳程选用碳钢,温度较低的管程则用不锈钢。利用不锈钢和碳钢线膨胀系数的差别,较好地避免了因管、壳程膨胀差引起的温差应力,不再设置膨胀节,降低了制造成本。
(6)换热管采用横纹槽管。由于横纹槽管可产生“二次流”和“边界层分离”效应,因此不仅可强化传热(传热系数可达光管的2倍以上),而且抗污性能高于光滑管。
2.3 应用效果
第一台新净化气水冷器于2001年4月投入系统运行。经测定,气体出口温度比以前下降了 10℃,至今未发生内漏和管束振动现象。第二台 DN 1 400净化气水冷器投用后,也取得了同样满意的效果。该新型换热器不仅能抵御流体振动的破坏,大大提高使用寿命,而且还具有高效、不易结垢的特点,为净化系统的经济运行创造了条件。
3 以填料-旋流板复合内件改造变换气脱硫塔
3.1 原脱硫塔使、用状况
金信公司净化老系统原有两台变换气脱硫塔,塔径2 600mm,高24m,内装塑料阶梯环,采用ADA吸收法。在填料使用初期,脱硫效率较高,但随着硫堵现象的加剧,塔内压差增大,最高达25kPa,且脱硫效率平均不到85%,每年因此而停车清塔2~4次,严重影响了系统的长周期运行和后续工序生产,加上该塔已使用多年,腐蚀严重、塔壁有裂纹出现。为确保安全生产,特别是解决硫堵问题,2000年该公司对变脱塔进行了更新改造。
3.2 改造概况
近年来旋流板技术应用于传质和除沫已有大量报道。用该技术改造变脱塔,具有开孔面积大、阻力小等优点,能较好地解决硫堵问题;缺点是脱硫效率较低。为扬长避短,金信公司设计了一种以填料—旋流板复合内件的新型变脱塔,并将塔径缩小到2 200mm。
改造后的变脱塔结构见图3,其特点如下。
(1)塔底部切向进气,并配置气体分布筒和筛液板,以增加气、液接触,提高脱硫效果。
(2)由于塔径较大,传质旋流塔板采用了双程叶片结构,提高了开孔均匀度,使气液分布均匀、接触良好。
(3)溢流装置采用新型螺旋叶片结构,它相当于半块旋流板,增加了气液接触机会,提高了脱硫效率,也提高了塔板的空间利用率。
(4)塔上部仍设置一段填料层,利用填料脱硫效率高的优势,减轻了旋流板负荷,提高了整个塔的操作弹性和脱硫效率。
(5)在顶层,液体喷淋采用易检修又防堵的宝塔型喷头取代阻力大、易堵且分布不均的螺旋喷头。
(6)塔顶除采用旋流板除沫、喇叭管阻液外,通过合理设计气体出口高度,达到了较好的除雾效果,减轻了塔后分离负担。
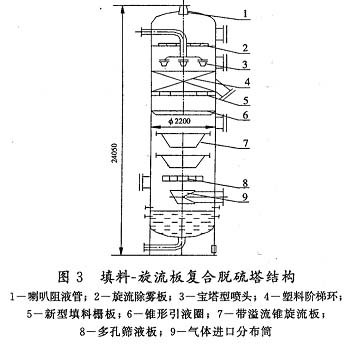
3.3 改造效果
(1)平均脱硫效率由改造前的不足85%提高到93%以上。出塔H2S含量由40mg/m3降到了15 mg/m3以下,大大减轻了后续工序的压力。
(2)生产能力得到了大大的提高。变换气处理量由原来的30 000m3/h提高到34 000m3/h;
系统提压到2.1MPa后,处理量可提高到41 000m3/h。
(3)塔阻力降低,最高阻力由原来的25kPa下降到4.0kPa。
(4)硫堵现象大为减轻,原来每年需停车检修清洗2~4次,改造后两年不需清洗、检修,为系统的长周期运行创造了条件。
(5)本项改造年综合效益在90万元以上。
4 新型安全熔硫釜的设计与应用
4.1 原熔硫釜基本情况
净化系统原有2台相同型号的间歇式熔硫釜,其任务是将系统脱硫而析出的膏状单质硫熔融成硫磺产品。原设计利用硫膏在140~180℃的熔融状态下其杂质可以悬浮分离的特性,将低压蒸汽(P≤0.4MPa,t≈150℃)作为热源引入到熔硫釜内,熔炼硫磺。两台设备在此条件下安全、正常运行了7a多,由于热媒温度与硫膏下限温度接近,因此熔炼时间较长,并且易造成杂质分离不彻底。将热媒改为过热蒸汽(p=0.5MPa, t≈250℃)后,釜内温度可达180℃,熔融时间大为缩短,同时产品质量明显改善。但热源改变后,熔硫釜上封头部位却逐渐变形,入料口接管与上封头结合处呈喇叭形向外扩张,并伴有封头鼓涨,至2001年3月因变形严重而停用。
4.2 失效原因分析
在排除了设计、制造、安装环节原因后,根据计算,确定引起上封头屈服失效的压力最小值为2.6MPa,说明操作条件的更改也不是失效因素(180℃的蒸汽压约为1.0MPa)。那么,如此高的破坏性压力源自何处呢?
经过调查、分析发现,失效的原因在于热源改造后的满釜操作:硫膏原料充满容器,在满釜操作下,不断加热的硫磺膨胀所需的体积有时会大于间歇排汽所留下的体积,这种情况一旦发生,釜内物料体积不断增大和膨胀,有可能形成大于 2.6MPa的膨胀压,从而引起釜体屈服失效。改热媒前,熔硫效率较低,不会满釜操作,不会超压,故能安全运行;改后由于满釜运行,导致了上封头(最薄弱部位)屈服失效。
4.3 重新设计新型安全熔硫釜
新设计的熔硫釜如图4。
为确保压力容器的安全,设计上进行了如下改进。
(1)新设料位自限装置。为防止熔硫釜满釜运行,即必须有效控制物料的加入量,为此,在封头部位特别设计了料位自限装置,确保装置安全运行。
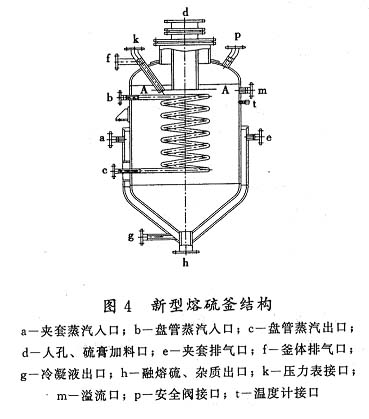
(2)配合设置溢流装置。在A—A面配对设置溢流排放口,当釜内料位处于A—A临界面时,打开溢流口,可迅速排料到位,并能消除f管口积料堵管;
(3)设置压力、温度指示。
(4)增设安全阀,成为熔硫釜最后一道安全
新型安全熔硫釜于2001年7月投入系统使用后,运行正常,操作简便,彻底消除了安全隐患,不仅硫磺质量良好,而且熔硫效率较高,达到了用户设计要求。原熔硫釜月产硫磺50t左右,新装置平均月产70t,最高时达100t,同时硫磺产品的一、优等品率也有所提高。
5 结 语
金信化工有限公司针对合成氨净化系统的部分设备或工艺存在的问题,分别进行了技术创新改造,取得了圆满的成功,展示了科技创新在企业技术进步、效益提高中的旺盛生机。
