1 改造前基本情况
湖南金信化工有限公司合成氨生产能力为 18万t/a,有2套相对独立、流程相同的装置。由压缩机五段来的净化气,经甲醇塔反应除去部分CO后,尚有少量CO、CO2、O2、H2S、油污、甲醇等有害杂质,其体积分数中:CO≈3.0%, CO2≈0.6%。净化气的精炼由铜洗系统完成。经水洗、铜洗、氨洗后,杂质总含量<30×10-6的精炼气返回压缩机六段,加压到31.4MPa,再送到氨合成塔合成氨。
铜洗系统曾是金信公司合成氨生产的“瓶颈”,主要表现为:①原料气通量不能满足压缩系统(共9机)的负荷,使气体净化能力不足;②系统生产不稳定,操作弹性小。当进入系统的原料气杂质含量超标时,调节能力非常有限,经常引起氨合成系统不能正常运行。为此,金信公司从2000年起,逐步完成了铜洗系统1#、2#装置的综合改造。
2 铜洗系统的综合改造措施
2.1 规整填料改造铜塔
2.1.1 改造方案
铜塔是系统吸收CO、CO2的关键设备,其内件为鲍尔环散堆填料。由于该填料传质效果欠佳,操作弹性小,导致铜塔吸收效果和效率较差,气体处理能力不足,系统生产不稳定。操作中,为提高铜液吸收效果,常采取加大铜液循环量的办法,6台铜液泵全部投入运行,造成铜泵的维护管理无序。同时,铜液量加得过大,易引起铜塔带液事故。因此,需采用高效填料改善铜塔现状。
经过技术招标,选定了天津天大天久公司的改造方案。该方案为:①采用规整填料更换原鲍尔环填料;②塔体外壳及管口大小、方位维持现状(见图1);③铜塔内共装设两段规整填料,总高度与原塔一致;④在上、下段填料顶部分别设置液体分布和再分布装置;⑤在气体进、出口分别设置分布装置和除沫装置;⑥塔内件不与塔壁焊接,依靠再分布器和稍加改制的原填料支架支撑上、下段填料;⑦塔内原气体和液体进口分别与新内件焊接或法兰连接。
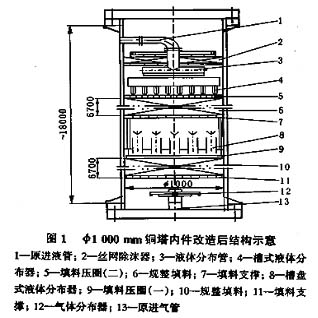
2.1.2 技术措施
为使铜塔达到吸收(传质)的高效性及良好的工艺操作性能,改造中采取了以下技术措施:
(1)采用JKB250-Y型规整板波纹填料。与散堆鲍尔环填料相比,该填料具有优良的传质效率、压降性能和操作弹性(见表1)。同时该填料具有较好的自分布作用,消除了散堆填料易造成的偏流、沟流等弊端,有效地提高了吸收效率。
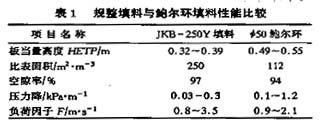
(2)采用二级槽式液体分布器。在保证填料顶端具有满意的铜液初始分布、较大的气相通道、操作弹性和较小阻力的同时,还具有较好的过滤铜液、防堵和不易造成雾沫夹带、泡沫的性能,为发挥填料的高效吸收作用创造良好条件。
(3)采用液体自分布填料,可有效地减少和防止铜液壁流,并改善塔内液体的分布,使填料保持较高的吸收效率。
(4)采用专利技术的槽盘式液体再分布器,具有较好液体再分布和气体再分布性能,为上、下段填料的功能发挥提供了有利条件。
(5)采用与液体分布器相配的填料压圈,既可以固定填料,又可以使吸收液最大限度地达到均匀分布的状态。
(6)采用特制的气体分布器,使气体进铜塔后初始分布均匀,降低了因气体分布不均匀产生的液体偏流。
2.1.3 改造效果
(1)运行状况 1#、2#铜塔改造后的运行状况良好(见表2),满足了生产工艺要求,为氨合成系统的正常运行提供了良好的条件。主要表现在:①经受了各种低、高负荷工况,气体通量分别达到了最大47 500、43 500m3/h的系统要求;②在最大工况下,单系统开2台铜泵即可使微量达到正常,铜液循环量降低了1/3。如果CO、 CO2偏离工艺指标,开3台铜泵(铜液量为54 m3/h)也可正常运行。
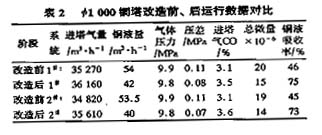
(2)节能降耗 改造后,减少了铜液循环量,年节支铜泵运行电费36万元;铜液再生时系统的蒸汽消耗下降了1.35t/h,全年节约蒸汽消耗96万元;铜液再生后所需的氨冷冻量减少约 167.5万kJ/h,减少冰机电耗约240kW·h/h,系统全年节支约87万元。铜塔改造后,每年可获直接效益约219万元,其投资回收期为:25/219=0.11(年)。
2.2 铜液过滤改用微孔管技术
2.2.1存在的问题
由于出铜塔的铜液再生后,含有微量悬浮物杂质,原系统一直沿用丝瓜络作为过滤材料以去除其杂质。该法存在以下弊端:
(1)过滤效果较差、效率较低,进铜塔铜液 长期不能达到铜洗系统的要求,制约了铜液对气体杂质的吸收效果,限制了系统的气体处理量。
(2)易引发事故。丝瓜络在使用初期,因其中含有较多灰尘,加剧了铜液的污染,不仅降低了铜塔的吸收效果,还易引起铜液发泡。
(3)使用寿命较短、更换不方便。丝瓜络使用较久后,大量的油渍附在其表面上,既造成饱和失效,又增加阻力,故每年必须更换丝瓜络。
(4)过滤效果不能适应铜塔内件改造后的要求。由于规整填料的波纹板片之间的间隔较小,如果铜液较脏,很容易发生堵塞现象,使气体偏流。要使规整填料不被堵塞并长周期运行,进塔铜液质量指标要求必须远高于散堆填料,而丝瓜络过滤器很难达到要求。
2.2.2 改造措施
针对以上问题,铜液过滤改用了微孔过滤新技术,将原丝瓜络过滤器更换成微孔管过滤器。该改造总投资为16万元,改造方案由温州东瓯微孔过滤器公司提出,过滤原理见图2。改造采用了旁路过滤,即逐步完成系统铜液清洁处理的工艺流程(见图3)。
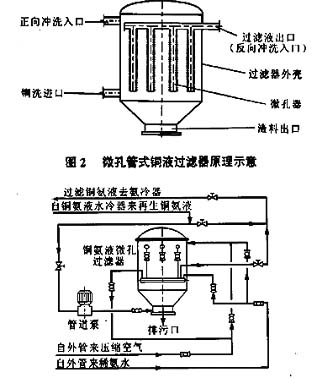
微孔过滤的关键元件是微孔管,工作时,铜液从过滤液进口进入,由于压力差的存在,迫使铜液流向微孔管。此时,微孔管管壁上的超细小孔起筛网作用,铜液穿越管壁后汇集到过滤溶液出料口流出,杂质被阻挡在管外形成滤渣,由渣料出口定期排出,从而实现铜液过滤分离。微孔管工作一段时间后,其管外壁上附着的滤渣使阻力增大,过滤效率急剧降低,此时,通过反向或正向冲洗使微孔管再生后,又可继续过滤。
2.2.3 改造效果
(1)过滤效果好,效率高(见表3)。微孔管过滤粒度达0.3~0.5μm,分离效果可达90%以上,由于改造中根据用户铜液特性试验选取了合适的微孔管及其过滤器,因此过滤效果完全满足铜塔规整填料改造后对铜液更高的品质要求。
(2)出口铜液不发泡。由于微孔过滤后铜液非常清洁,铜塔带液和再生系统运行不正常的事故再未发生,消除了安全隐患。
(3)操作方便。过滤管再生时就地处理,不需拆卸设备,方便快捷、操作简单,经过再生处理后,过滤效果可恢复如初。与此同时,过滤物渣料可及时排出,能保持系统生产的连续稳定。
(4)使用寿命长。该过滤法属于物理过滤,不改变溶液原有成分,避免了易饱和失效的难题。由于不需更换过滤材料,微孔管使用寿命可达3~5年,因此检修周期明显增长。
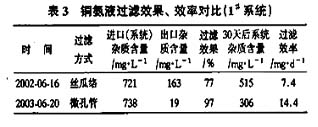
2.3 开辟再生系统新热源
铜洗再生系统自投产以来,铜液还原、再生所需的热源一直采用热电锅炉系统生产的低压过饱和蒸汽(0.2MPa,200~250℃),虽然能有效地保证再生系统所需的热量,但由于蒸汽耗量较大(8~10t/h),成本较高。合成氨系统3#甲醇塔投产后,其副产的中置锅炉蒸汽供铜洗系统使用,但仍需消耗低压蒸汽8t/h左右,再生系统成本仍然偏高。
为降低成本,将尿素系统三饱蒸汽引作再生系统热源。虽然该温度相对较低(0.3MPa,140℃),但由于再生系统工作温度(73~80℃)远低于三饱蒸汽温度,因此引接三饱蒸汽可以满足要求。废热蒸汽引用后,可节约低压蒸汽1t/h按装置年运行330天,低压蒸汽45元/t计,该改造 每年可节约成本35万元。
2.4 铜液再生器的气相腐蚀问题
该设备为卧式容器,碳钢材质,在1#、2#系统2套装置的运行中均出现同样的问题:与再生气气相空间接触的容器上部内壁腐蚀速率较大,而与铜液接触的下部内壁基本上不腐蚀。为此,每次大修期间对其腐蚀严重的部位采取挖补措施。长年的挖补,已危及系统的正常运行。
引起设备上部腐蚀的主要原因是容器上部长期存在较浓的CO2、碳酸与氧气共存条件下构成碳钢的严重腐蚀环境。由于再生气中含有CO2 (12%)、O2(1%)和微量水蒸气,因此与上部器壁接触的还有少量碳酸。查阅文献可知,较浓的CO2和碳酸在有氧条件下可构成碳钢的严重腐蚀源。因此改造设计中,将与气相接触的壳体材料改为耐酸不锈钢结构,其余仍然采用碳钢,既解决了腐蚀问题,又节约了改造投资。
2.5 铜液水冷系统冷却效果
在夏季,铜液水冷器的出口温度高达54℃,与工艺指标值(≤40℃)偏离较大。为降低入铜塔铜液温度,需加大铜液水冷后的铜液氨冷器的负担,相应地也加重了冰机的负荷,不利于系统经济运行。
为改变铜液水冷系统的被动状况,将闲置的原冰机板式换热器修复,与列管式铜液水冷器并联使用。由于板式换热器运行效果良好,在炎热环境中也能控制铜液温度在45℃,替代了原列管水冷器。
2.6 更新改造2#吸氨塔
再生气吸氨装置中,2#吸氨塔存在的问题:
(1)局部腐蚀严重 该塔材质为16MnR,其底部设计了高1.5m的入塔再生气缓冲空间,再生气吸氨处理后产生的稀氨水在缓冲空间顶侧流出。该装置运行不到7年,塔器底部的缓冲区出现了严重腐蚀和泄漏现象。由于该段简体内壁虽然与干气相的再生气接触,但其顶部的稀氨水造成内壁为湿性环境,因此腐蚀的主要原因是该部位较浓的CO2和碳酸在有氧条件下构成碳钢的严重腐蚀环境所引起。
(2)气体通量受限 该塔在高负荷工况下,尽管加大了喷淋水量,塔壁温度还是较高,而且吸氨效果不理想。主要原因是由于塔径(¢700 mm)太小,填料装填量较少所致。
在2#吸氨塔改造中,采取的措施为:①减少缓冲区;②防止浓CO2和碳酸在有氧条件下构成碳钢的严重腐蚀环境产生;③塔底材料改为耐酸不锈钢;④适当放大了塔径,并增加填料高度。
改造后,运行效果良好,既消除了安全隐患,制止了严重的浪费,又使该设备与系统配套。
3 结语
铜洗系统实施综合改造后,有效解决了原系统2套装置中存在的问题,并使该系统对合成氨原料气的精炼能力与气体压缩系统的最大出气量相适应,消除了合成氨装置的“瓶颈”,实现了装置生产的经济运行,取得了显著的节能、降耗效果。
