湖南安淳高新技术有限公司从上世纪80年代中期开始进行氨合成系统及甲醇系统的开发研究工作,在研究了国内外各种技术的基础上,创造性地提出了氨合成塔分流工艺。发明了ⅢJ系列合成塔技术,该技术曾获得国家科技进步二等奖,在全国推广达400多台套。
近年来,通过总结ⅢJ系列内件在全国合成氨行业近400多台次和厂家的运行经验,汲取20世纪90年代以来国际国内先进技术以及国内引进的大型氨厂合成塔运行经验,对氨及甲醇合成塔进入大型化、配套的系统进入大型化、单套生产能力更大等方面进行了广泛的研究和技术对比后,开发了DN2400、DN2200、DN2000、DN1800等系列氨合成系统;开发了DN2800、DN2200、DN2000等系列单醇和联醇的大合成系统。
甲醇或氨合成系统技术相继在山东瑞星化学工业集团公司、山东德齐龙化工有限公司、河南心连心化工有限公司、江苏新沂恒盛化工有限公司、山东华鲁恒升化工有限公司、山西晋城天脊集团、山西晋丰集团、福建三明化工有限公司等厂先后投入使用或进行设计。
本文就安淳公司的技术进行介绍。以利于了解本技术,对选择本技术及产品提供参考。
1 氨(醇)合成塔内件的研究
氨(醇)合成系统中的合成塔内件是氨(醇)厂生产中最重要的设备之一,我们调研了国内外各种不同类型内件的设计及使用情况后,于1986年研究设计了一种新型内件,其中DN600-ⅢJ型氨合成塔内件于1988年投入运行,投产后,立刻在全国同行业大面积推广。先后获得多项国家专利,1990年通过化工部科技鉴定,鉴定认为:“该内件工艺思想及技术为国内外首创,主要技术指标取得了突破性进展,达到国际先进水平。”该技术多次为国家级重大科技成果重点推广项目,技术成果参加过维也纳、吉隆坡国际新技术新产品展览,获国家级新产品称号、1995年获国家科技进步二等奖(迄今为止,国内合成塔内件的最高奖励)、中国专利技术金奖、湖南省科技进步一等奖。现在有近400多家合成氨厂使用该技术及产品。该型塔的显著特点是氨净值高(氨净值一般在15%以上),单塔生产能力大。湖南衡阳市氮肥厂、山东新泰化肥厂、湖北荆门一化、河南商水化肥厂等厂φ600mm塔日产平均达100t氨以上;φ800mm合成塔在安徽涡阳化肥厂、天津碱厂、河南新野化肥厂、湖南汩罗氮肥厂等厂日合成氨产量达140~170t,氨净值约16%;后来经过改进,又设计制造了ⅢJ-99(A)、ⅢJ-99(B)、ⅢJ-99(C)等三种φ1000mm合成塔内件和ⅢJ-99φ1200mm合成塔内件,催化剂装填量分别为5.8m3、6.8m3、7.8m3和11.4m3,年合成氨设计能力分别为60kt、80kt、100kt和120kt。在成都化肥厂、重庆潼南化工总厂、山东鲁西化工集团公司、湖南临湘氮肥厂、四川美丰化工股份有限公司、大乘资氮集团、福建永安智胜化工联合公司、山东瑞星化工集团公司、山东峄山化工集团公司、山东寿光联盟化工集团公司、山东明水化肥厂等厂投产后效果都很理想。
近年来开发的φ2200mm、φ2000mm、φ1800mm、φ1600mm、φ1400mm等系列ⅢJ型大直径氨(醇)合成塔内件,正是上述成功经验的总结和技术升华。它既是原技术思想的总结和优化,也是多年合成系统开发研究的成果发展。
1.1 内件研究的指导思想
氨合成反应是一个可逆放热反应,必须在高压、适宜的温度和催化剂条件下才能进行。作为反应器的内件结构设计,必须从理论上、实用上、经济上系统地、全方位辩证地进行考虑,尽量做到以下几点:
(1)容积利用系数要高;
(2)催化剂利用系数要高反应氨净值高;
(3)催化剂升温还原要容易;
(4)操作弹性要好;
(5)内件结构要简单可靠;
(6)内件的催化剂床层阻力要小;
(7)热回收率要高;
(8)装卸催化剂要容易。
以上8个方面要全部满足,有一定的难度,因为其间存在着一些互相制约的条件,关键是如何调解制约因素,采用辩证思维达到整体最佳的目标。ⅢJ系列内件正是在这些相互约束条件下,综合优化考虑进行设计的。
1.2 氨(醇)合成塔内件三种基本形式评述
氨(醇)合成内件的型式很多,就其共性而言,任何形式的可逆放热反应器,开始都是绝热反应,直至达到催化剂的热点温度为止,此时的氨含量有7%~8%。即只占全塔反应量的35%~38%。要继续进行反应,必须移走反应热,降低反应温度。
甲醇反应器除了少量诸如利用高温水来调节床层温度的等温式合成反应器外,绝大部分的合成反应器为气固反应床层的反应器。一般设有多段反应床,中间设移走热量的机构。
就其反应热移走的方式来评述,有段间换热移热方式、内部换热移热方式、冷激移热方式等三种基本型式,目前在用的主流内件均是这三种形式的组合或变形。这三种型式,如用上述8项标准来评价,各有优缺点。
1.2.1 段间换热式
即在催化床层间设置间接换热器,绝热反应一次,温度升高,在换热器内冷却,再绝热反应。它的优点是在段数多的情况下,反应接近最适宜温度曲线。段数越多,反应曲线越接近最适宜温度曲线,并且反应速度越快,氨净值越高。但它的缺点是换热器占了一定空间,催化剂装填量将减少,且段数越多,催化剂越少;段数越多,内件越复杂,维修装配越难。例如一个采用三段段间换热型的内件,比其他型式的三段式内件要少装15%~25%的催化剂。
1.2.2 冷激式
即气体在催化剂筐中绝热反应一次,温度升高后,便用未反应的冷气体为已反应的高温气体直接混合降温,再反应,再直接降温。冷激式最大优点是结构简单(国内目前一种推广面较多命名为“轴径向型”的塔主要为冷激式降温),催化床层内每段除了冷热气混合分布器之外,没有其他部件;第二个优点是催化剂装得多,例如以同样的φ600mm塔配的四段冷激内件,催化剂装填量为1.55m3,冷激式最大缺点是每冷激一次,混合气体中氨稀释一次,故氨净值降低了,也带来了同样产量下循环量增大的问题,而循环量增大将直接造成热回量减少。这也是冷激式塔型的热回收率量低于其他塔型的原因之一。
对于小型塔来说,冷激式的花板和分布器装拆困难,催化剂装卸也困难,且段数越多,装拆越困难。塔的操作弹性也小,总气量,冷激气量,温度,氨含量关联太密切,太灵敏,以致操作调节的速度难于跟上温度变化速度。
1.2.3 内部换热式(内冷式)
将一定数量管子埋在催化床层内,氨合成反应一边进行,热不断被管内冷气(间接传热)移去。它适应于可逆放热反应的特点。随着反应的进行,氨含量增加,放出的热量不断被移走,使温度下降。内冷式相当于“无级”的段间换热式,因此它的最大优点为反应温度最为接近最适宜反应温度曲线,氨净值较高。ⅢJ系列内件氨净值最高达16%。内冷式的缺点是结构比冷激式复杂,冷管占据了部分空间,催化剂装填量少。用上述相同的φ600mm塔,一般只装催化剂1.3~1.38m3,较好的装1.46~1.58m3。其次有管壁效应,冷管直通床层底部,一部分气体沿着管壁流下,致使这部分气体未达到较高的合成率而流出去了,还有在管壁处附近的催化剂由于还原时温度指标无法达到要求,使此部分催化剂还原不彻底。因此旧式冷管内件,实际氨净值却不高。旧式冷管内件管子太长,又是与筒体或中心管连接的,在温度变化时,冷管容易拉裂。
ⅢJ型为改良的内冷式内件,采用了改良冷管式结构,综合了上述三种形式冷却方式的优点,克服了传统内冷式内件的缺点,使氨净值达到15%~16%,冷管不断裂,升温还原关闭冷气,冷却器周围无过冷现象。
由上综合评述,内冷式通过改良,不失为一种良好形式,有许多优点;冷激式有其优点,但存在缺点相对较多,例如Topsφe的S-200内件为两段冷激式,由于段数少,氨净值只有13.36%。Casale为我国φ1000 塔提出的改造方案,采用两段冷激式,其氨净值也只有14%。例如 Unde公司帮助 IGSAS工厂将原三段冷激式改为三段间冷式,出口氨浓度由16.3%增加到18.7%(进口氨3%)。国内在φ800mm和φ600mm塔上用过三段间冷式,中间装二个列管换热器,第三段的催化剂装卸很困难。实际氨净值也不理想。
1.3 合成塔选择中几个问题的讨论
我们是很早在注重合成塔内件的同时,注重进行合成系统开发的公司。我们认为氨合成系统高压圈中,特别是合成塔内件为系统的关键设备,因而设计和选择显得非常重要。但系统是保证热回收、冷回收、能量节约和内件催化剂效率发挥不可或缺的重要因素。
我们结合多年来从事合成塔设计的经验,在确定了合成系统总规模和配套系统的情况下,合成塔及合成系统的选择有下列问题可供讨论。
1.3.1 高径比的选择
我国目前中、小合成氨厂的合成塔受我国早期国内高压容器制造技术和制造能力的限制,往往将合成塔做成“瘦高型”(高径比达15以上),这种塔型几乎占据了全国中、小型合成氨厂的合成工段,也给使用和设计者造成了一种“思维定势”。近年来随着国外技术的引进,设备制造业的进步,国内大型合成塔的制造工艺和材料的问题得到了解决,因而新上的合成塔较多地选择低高径比(高径比小于10)的塔型,这样有利于将合成塔阻力降,由传统型塔的催化剂床层阻力1.0~1.8MPa降至仅有0.2~0.6MPa。
1.3.2 径向筐的设置
改变高温反应气在内件中的流动方向,设置催化剂床层径向筐,以利于降低阻力,也是目前运用较多的技术。但如果径向筐设置过长,也有运行操作弹性差、气体分布不易控制、催化剂利用系数低、有效高压容器利用系数小等缺点。只有合理地设置径向筐和径向分布器才能带来优势。我公司近十年来径向合成塔推广了近二百个塔和厂家,积累了一些经验,目前径向气体分布技术已相当成熟。本方案采用大直径的合成塔更有利于采用径向流技术。现已经将DN2200、DN2000、DN1800、DN1600或DN1400塔设置的径向段高度占总床层高度在65%以上,较多地运用“一轴三径”、“二轴三径”、“二轴二径”等塔型式,部分塔型的径向筐设置为全部径向型的塔。
1.3.3 催化剂生产强度的选择
目前我国中、小合成氨厂的合成塔催化剂生产强度大部分厂家达40~50 t/(m3·d),少数厂曾经高达60~70 t/(m3·d)。使每m3催化剂的平均寿命在20kt氨左右,这样势必造成频繁换催化剂,运行的空速也很大,系统及内件的阻力也很高,这是一种高产、高消耗、低效益、“拚设备”的老生产模式。这种作法在小塔型、小能力的合成氨厂短期内尚可有短期的效益,但大型塔和新制设备、大能力的厂家应杜绝此方式。国外引进的15~22MPa级的合成氨装置催化剂生产强度只有15~20 t/(m3·d),一个内件、一炉催化剂可连续运行8年以上,每1m3催化剂生产氨达50kt左右。30MPa级的合成压力,催化剂生产强度定位在25 t/(m3·d),较符合国际先进的节能思维模式。选择大直径、小的高径比、多装催化剂的塔方案正是基于此考虑。
1.3.4 空速的确定
低空速运行有利于降低系统阻力,提高氨净值,节约电耗。目前大化肥厂的合成塔运行空速在8000 h-1左右(15~22MPa压力级)。ⅢJ系统方案空速定位尽量小。计算得知,如果氨净值在14%,较多的场合,运行空速在9000 ~12000h-1范围较为合适。
1.3.5 合成塔内件阻力降
多装催化剂、装相对小颗粒的催化剂有利于提高反应效率,降低空速。但装颗粒过小的催化剂,容易堵塞径向筐小孔,反而使阻力升高。应谨慎选择催化剂的装填粒度。合成塔的“高径比”是一重要影响参数,理论和实践证实,当内件的高径比大于11时,不多设径向筐,要将内件阻力降至0.6MPa以下较为困难。ⅢJ方案选择大塔、小高径比、多径向段、低空速的催化剂筐也正是为这一目的。
1.3.6 根据催化剂配套设计
需催化反应的任何工业装置,反应器的设计均应和催化剂的特性相匹配,高活性、宽耐温区、高强度、低阻力的催化剂是催化剂研究设计者所追求的,也是合成塔内件设计者所希望的。ⅢJ方案考虑配套选用345~495℃的宽温区内活性均高抗毒性强的强化磨角型催化剂。据此而设计内件、将各段床层的高度分配进行优化。
基于上述三种型式内件优劣的分析和内件选择的讨论,又考虑到国内外使用这三种内件以及由此派生的冷激—间冷内件的实际效果,我们研制ⅢJ型氨合成塔内件。其总体工艺及设备的构思如下。
用一个独立导入冷气的冷却组合元件来代替多个间冷换热器(大直径的塔型这个段间换热器可以使气体实现径向流),催化剂床层由上绝热层—第二绝热层—第三绝热层—内冷层—下绝热层组成;它是一个既有无级间冷,又有冷激内冷组成、气体流向大部分采用径向流动方式(一轴三径、三轴一径、二轴二径或二轴三径等床层)的反应床层。它充分发挥了三种换热形式的优点,克服了他们各自的缺点,成为一种低空速、高净值、低阻力、高产量、节能、结构简单可靠的较理想内件。
1.4 内件的主要特点(图1)
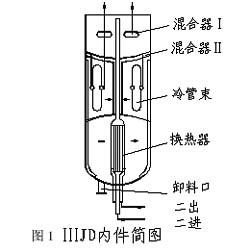
1.4.1 一个独立的气体冷却组合器构成四段或五段反应器
对于氨合成这样可逆放热反应,如果要求其合成率较高,或一定催化剂量条件下,生产能力较大,必须采用多段反应,且段数越多,合成率越高。但段数越多,结构越复杂。ⅢJ-99和ⅢJ内件在催化床内只安排一个类似冷管换热方式的冷却组合器,即构成一个包含有上绝热层—第二绝热层—第三绝热层(四段塔无此层)—内冷层—下绝热层等五段的反应器。反应温度能比较逼近理想曲线。冷却组合件结构简单,与内件筒体无焊接点,可以自由放进和拉出。随着温度的变化,可以自由伸缩。组装、拆卸容易,比组装多段冷激式内件的各段冷激分布器还要方便简单。
1.4.2 分流工艺
传统的氨合成塔内件,冷管内的未反应气体100%都是经过了下部换热器加热之后再进入冷管束的。ⅢJ内件则完全不同,未反应的气体是分成两股,分别并流进入下部换热器和冷管束。这样带来很多的好处。
① 冷管束内冷气温度很低, 50~180℃,传热温差很大,一定的热负荷下需要的冷管面积大幅度减少。加之冷管段安排在第三或第四段,单位催化剂反应量减少,反应放出热量少,需要的冷管面积更少。因此,冷管根数少,冷管短,占用床层空间少,催化剂装填量多。
②下部换热器热负荷减轻。传统的工艺是100%未反应冷气,通过下部换热器加热。而ⅢJ-99和ⅢJ-2000内件经过此处的未反应冷气只有50%~60%。需要的换热器面积减少,相对地催化剂筐体积加大,装填催化剂量增加。其次,热气体因被冷却程度减少,出塔温度高,有利于多产高品位蒸汽。
③分流进气,气体阻力减少。特别是进入中心管的气体只有循环机出口总气量的50%~60%,在中心管内的阻力显著减少。
1.4.3 多种形式轴径向的组合式
径向塔的优点是气体流经路线短,阻力小,适应于小颗粒催化剂,节能效果好。然而小直径径向塔,由于路程太短,气体分布不均匀;一些分段式径向筐,由于催化剂还原后收缩,在径向筐上部形成自由空间,造成气体短路,部分气体没有反应。使氨净值低,生产能力小。
在ⅢJ型内件设计中,采用了多种型式的轴径向组合式塔,如二轴三径(或二轴二径、一轴三径)的型式,视产量要求情形,上部设一段或二段反应床为轴向,下部均为径向流的结构,既保证反应效果,又降低了阻力,特别是内冷段的间接换热器采用了径向流的结构,对降低阻力有显著效果。
1.4.4 多气腔式多层分布型径向气体分布器
为保证径向催化床层气体分布均匀,径向筒采用了喷射小孔和多混合腔结构,并有防止粉化催化剂阻塞的作用。
1.4.5 段间换热冷却段气体流向为径向流
传统的冷管型氨(醇)合成塔,冷管部分均为气体只能走轴向(冷管内气体从上到下流向,冷管处气体也从上到下流),由于冷管段占用了催化剂的空间,也减少了横截面积,造成了冷管段的阻力大,传统的方式是此部这分装粗颗粒的催化剂,这样更易造成沟流等气体走短路的现象,这也是冷管效应的一种表现。我们设计的段间换热器冷管,采用管内气走径向管外气体亦径向流动的方式,克服了此层阻力大的缺陷,使内件完全可实现全径向的气体流的方式。
1.4.6 催化剂床层完全直通式
传统的多段式内件,各段之间大多有隔板将其分开。装、卸催化剂时,从底层开始,装一层盖一层;有些内件装卸催化剂时,需将内件筒体切割或焊接,十分繁琐复杂。
φ1400mm、φ1600mm、φ1800mmⅢJ内件虽然有五段,且第四、五段是径向筐,由于采用了菱形混合器、菱形集气器和带有卸料管的锥形底径向筐,既严格保证了工艺上的分段,又可以使催化剂由上直通下部。所以催化剂的装填,更换均可从底部尾管自卸出来,而不要吊出内件倾泻,检修十分方便。
1.4.7 直形异径折流径向冷却器
ⅢJ内件设计采用直形异径冷却器。传统冷管束中的冷管,和上、下环连接处,两端均加工为弯形与环管径向对接,弯曲的冷却管有很大的弯曲应力,在受热膨胀和降温收缩时,弯曲处容易断裂,这是有冷管束以来一直存在的老大难问题。我们采用扁形直管与上下环切线焊接的方式,既便于加工制造,又避免了弯曲应力。从1991年起投运直形冷却器200多台,至今无一损坏,彻底解决冷管断裂严重影响生产的难题。ⅢJ型内件,在原来直型冷管基础上,又发展为由直形折流径向冷却板块组成的间冷器,解决了冷管径向传热问题。
1.4.8 长形、横纹管换热器
小直径合成塔内件下部换热器为鼓形小列管换热器,ⅢJ内件换热器为瘦长型,长径比为7~8,换热管为横纹小列管,使传热系数大幅度增加,占用高压容积减少。
2 合成系统流程开发及研究
以内件为中心而设计的合成系统流程,我们主要是注重热量的回收和冷量的回收。
2.1 流程概述
ⅢJ合成系统原则流程如图2。
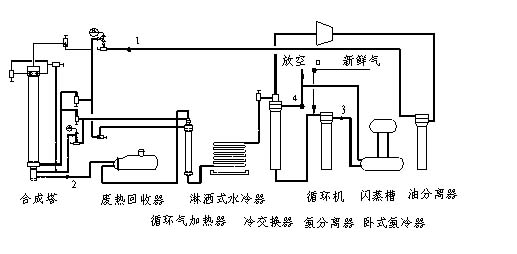
图2 ⅢJ合成系统原则流程
从合成塔下部四通出来的热气,温度约320~340℃,氨含量16%~17%,进入废热锅炉,温度降至200~210℃,进热交换器,被冷却至约80℃,进水冷排,冷却至35℃,进入冷交管间,温度降至10~15℃,液氨分离后,进入氨冷器,氨冷、氨分之后,补入新鲜气,使混合气温度达到-5~-1℃,再进入冷交管内,回收冷量之后,气体升温至约25℃,进循环机压缩,分离油后,分成两股,一股约62%进入热交管外加热至185~195℃,从合成塔底部进入(二进)塔内换热器管内,加热后进入中心管,从中心管出来进入催化剂筐第一绝热层反应,反应后热气利用从塔顶下来约8%的冷激气降温后进入第二绝热层。另一股约30%的未反应气体从合成塔下部进入环隙,由下而上到内件顶部,从两根导气管进入冷管束,气体在冷管束内加热后,温升至约250℃,经上升管达到第二、第三绝热层之间,作为从第二绝热层反应后热气(470~480℃)的冷激气,两者混合后,温度为410~420℃,进入第三绝热层、冷管层、第四绝热层反应,反应后温度为440~450℃,进入塔内换热器管间,被冷却至310~340℃,出塔,再进入废锅,热交……如此循环。流程中各节点组成见表1。
2.2 流程特点
①约30%的未反应冷气经塔内外筒环隙进冷管。约62%的未反应冷气进入热交。其优点是通过催化剂筐壁散失的热量,仍回收到催化床层内,相当于减少了催化剂筐的热损失。
表1 流程中各节点的物料成分表 %
节点 |
组 分/% | |||||
H2 |
N2 |
NH3 |
CH4 |
Ar |
合计 | |
0 |
74.10 |
24.70 |
0.00 |
0.88 |
0.32 |
100 |
1 |
57.75 |
19.25 |
3.00 |
14.67 |
5.33 |
100 |
2 |
42.76 |
14.25 |
19.74 |
17.05 |
6.20 |
100 |
3 |
49.55 |
16.52 |
4.99 |
19.76 |
7.19 |
100 |
4 |
51.02 |
17.01 |
4.24 |
20.34 |
7.40 |
100 |
② 进热交的冷气温度35℃~40℃,使进水冷排热气温度降到小于80℃,提高了热回收率,减少了设备投资(节省了一个软水加热器),传统流程中,如果不设软水加热器,进冷排温度为120~130℃。
③ 冷交热气走管外,有利于氨的分离。传统流程中反应后热气由上而下走管内,再由下而上经中心管离开冷交,被管外冷气冷凝后的液氨部分积留在管内,影响冷却效果。而新的流程含氨气体走管外,管子是螺旋管,冷凝的液氨沿管壁螺纹槽旋转而下, 在分离段分离。提高了冷却效果。
④ 补气位置在氨冷氨分后,流程图中的“0”点。减少氨冷负荷,节约了冷冻量,同时又降低了气体中氨含量,有利氨合成反应。流程中第3点之后,即氨冷之后氨含量为4.99%,补入新鲜气后,即为流程中第1点,氨含量只有3%。但新鲜气中CO+CO2应控制在10×10-6以下。采用双甲工艺,可以达到或低于此指标。
⑤ 循环机放在塔前,其优点是节约了冷冻量。
⑥ 放空位置在冷交氨分后,流程中第4点。已有70%左右的氨冷凝为液氨,并分离出去,气相中氨含量较低,为4.24%,而甲烷含量最高,为20.34%,因此,放空量最小,氨和有效气体损失少。
3 智能化控制装置
ⅢJ型氨合成系统采用微机智能化控制系统。配用DCS或FCS计算机工控装置,将专家设计思想、控制策略设计成程序,在屏幕上适时显示各点运行参数(如各点温度、压力、成分、液位等),各种图表曲线(如流程图、趋势图、催化床层温度曲线等),根据气量、成分的变化,自动调节阀门,将催化床层温度控制在最佳范围之内,出现突发事故,例如温度突然下降,屏幕上立即提示是什么原因,并立即自动处理,包括自动开启电炉。有些情况不能自动处理恢复,屏幕专家提示手动调节的方法,可供参考。这样不但稳定了工况,稳定了生产,同时减轻了工人的劳动生产强度,并节约了劳动力,配用智能化控制系统以前,每台班至少要安排两名操作工,配用了智能化控制系统后,只要一名操作工就可以了,而且给生产管理人员带来极大的方便。
4 采用先进的换热设备和分离设备
传统流程的合成系统采用的热交和冷交都用大环密封填料,实践证明此种结构密封效果很差,而且随着设备尺寸的加大,效果更不理想,ⅢJ氨合成系统设计的热交、冷交都采用小密封填料的结构形式,同时换热管采用高效强化换热管,所以换热(冷)效果较前好很多,节能显著。
在分离设备上我们也改变了传统的碰撞和填料分离方式,采用高效旋流分离与填料分离相结合的新型分离器。
5 卧式氨冷器及闪蒸槽
小直径合成塔系统配置的氨冷器为立式盘管式或立式U型式,当氨冷面积较大,制作加工困难,且氨冷液位不稳,影响冷热传递效果,为解决此问题,ⅢJ合成系统借鉴引进大型氨厂的先进技术,设置卧式氨冷器,并在其上配置闪蒸槽,经过多年的实际运行证明,此型式的氨冷器具有冷却均匀,节冷效果显著,对保护设备和提高制冷效果均有突出的优越性。
6 配套系统的设计
6.1 原料气精制度很高的净化精制工艺
为保证大型塔催化剂长周期运转,至关重要的是原料气的质量。即CO+CO2含量要很少(CO+CO2≤10×10-6)。国内以煤为原料的氨厂,采用铜洗流程,上述指标是达不到的,且时有带液现象。国外的深度低变—甲烷化,因为要保证进甲烷化CO+CO2≤0.1%~0.3%,要求低变气中CO≤0.3%,国内以煤为原料的变换系统达到这个指标将使蒸汽消耗很大(吨氨耗蒸汽800kg)。为此必须采用国内已实现运行六、七年之久的双甲工艺精制方法(或醇烃化精制工艺方法),它采用中高压(10.0~32.0MPa)压力等级。任意氨醇比之下只要求脱碳气CO2含量为0.2%及其总硫0.5×10-6下,经过甲醇化,将原料气中CO+CO2转化为粗甲醇,醇后气CO+CO2含量≤0.3%,进入甲烷化,烷后气中(即进合成系统气体)CO+CO2含量≤5×10-6。
6.2 宽温高活性高强度小颗粒催化剂
ⅢJ型内件零米温度设计较低,为350~360℃,热点温度设计较高为470~480℃。即第一绝热层温升120℃,氨净值8.1%,因此要求催化剂是高活性宽温催化剂。其次,设计有三个径向段,催化剂以小颗粒(2.5~3.5mm)为主,可大大提高反应效率,又不会增加阻力,在提高催化剂低温活性的同时,充分注意制造工艺,不使催化剂颗粒过于硬脆,防止使用中粉化。本公司特研制了适用于上述特征的含钴和稀土的XA201、XA203催化剂。
7 推广使用实例
(1)山东瑞星化工集团公司
该公司现合成氨能力为400kt/a,曾于1996年、1998年使用了我公司的DN1200、DN800 ⅢJ-99氨合成系统各一套,于2003年底在400kt/a合成氨技术改造中,率先采用了我公司的一套DN1800氨合成系统,于2003年底投产。目前,此套氨系统每天产合成氨620t,系统压力只有24MPa。整体工程设计和设备均由我公司提供,全部工程投资约2500万元。工程投产后,吨氨综合电耗比改造前减少约120kW·h,吨氨综合煤耗比改造前降低约180kg。全厂上下均一致称道,为一个质优效益好的工程。此DN1800氨合成系统为全国此压力级最大的塔型,也为目前世界上最大的32MPa压力级氨合成系统,开创了先河。继此后,山东德齐龙化工有限公司也投用了此系统,用该型内件和我公司设计的醇烃化工艺配套,实现单套装置180kt合成氨的生产能力。
(2)江苏新沂恒盛化工有限公司
相继使用了我公司的DN1400氨合成塔、DN1400甲醇化塔等,目前又投用了我公司设计的DN1800氨合成系统,用以配套18·30工程,并采用了醇烃化工艺,运用了DN1600甲醇化系统。
(3)山东德齐龙化工有限公司
两套18·30的合成氨工程使用了我公司的醇烃化技术及氨合成技术,甲醇化塔使用了4台DN1400的合成塔,氨合成塔使用了2台DN1800氨合成塔。
(4)湖南岳阳天润化工股份有限公司
该公司目前合成氨生产能力180kt/a,2000年初,投用了我公司一套DN1600氨合成系统,此系统为ⅢJ系统的第一套,目前合成氨产量达450t/d,系统压力只有21MPa,催化剂使用到目前为止约5年。
(5)河南心连心化工有限公司
该厂2003年新投入一套150kt/a合成氨装置,合成工段及净化精制工段采用了我公司的ⅢJ系统及醇烃化净化精制工艺来实现,装置于2003年8开车,目前合成氨生产450t/d,甲醇生产200t,系统压力只有23MPa。开工后,企业第一天多创利润20~25万元。目前230kt/a合成氨系统正在安装我公司设计的DN2000氨合成系统及DN1600甲醇化系统和醇烃化系统。
(6)山西晋城煤化工有限责任公司
该公司进行220kt/a合成氨工程扩建时,采用了我公司的醇烃化工艺及氨合成,于2002年12月投产了一套DN1600ⅢJ的氨合成系统,现日产合成氨480t,系统压力只有25MPa。目前的30·40项目采用我公司设计的DN2200甲醇化系统及氨合成系统。
(7)湖南大乘资氮集团有限公司
也是最早采用我公司ⅢJ氨合成系统的厂家,目前一套DN1200和一套DN1400氨合成系统,每天产氨和醇共计850t。综合经济效益十分显著。
除此之外,还有山东鲁西化工股份有限公司、山东华鲁恒升化工有限公司(德州化肥厂)、邯钢集团化肥厂、福建三明化工总厂、河南驻马店化工总厂、江苏昆山锦港实业集团公司、江苏华尔润集团公司、江苏张家港锦港实业公司、山西丰喜集团临猗分公司、江苏新沂恒盛化工有限公司、天脊集团晋城化工股份有限公司等厂先后采用了我公司ⅢJ型(φ1400~φ2200mm)氨合成系统。我公司的ⅢJ99型φ1200~φ800mm型氨合成系统及氨塔内件在全国推广面更是十分广泛,占合成氨厂的塔型中的30%以上。
8 结束语
ⅢJ型氨合成系统及氨合成塔内件,是在内冷、间冷、冷激等传统内件的基础上,吸收了国外合成系统的精华和经验,用计算机优化计算,并且经过φ600、φ800、φ1000、φ1200的反复实践、修改,研制的低空速、高净值、低压降的新型节能内件。同时以内件为中心,设计出与之配套的系统流程与设备,更能发挥整体优势:
⑴ 结构简单;
⑵ 高压容积利用系数大;
⑶ 生产能力大;
⑷ 氨净值高,空速小,塔压降小及系统阻力小;
⑸ 催化剂还原容易;
⑹ 装卸催化剂容易;
⑺ 结构可靠,使用寿命长;
⑻ 智能化控制,操作简单,弹性大,稳定性好;
⑼ 热回收量大,冷冻量消耗少,放空量少;
⑽ 内件金属材料消耗少,设备投资少。
这些优点,主要得益于分流工艺和绝热、内冷、冷激的巧妙结合,以及直形异径冷管束和两头成锥形的径向催化剂筐。是从小到大(φ600mm、φ800mm、φ1000mm、φ1200mm、φ1400mm、φ1600mm、φ1800mm)反复实践、修改、优化的结果,经过了多年的实际考验,受到了普遍的赞扬。
