尿素装置发生爆炸的事故屡见不鲜,其原因是多方面的,如设备管道腐蚀引起的爆炸;爆炸性气体引起的爆炸等等。就其爆炸比例来看,爆炸性气体引起的爆炸比例当属前列。就尿素装置而言,爆炸性气体产生爆炸多在中压系统。笔者针对尿素中压系统爆炸隐患的来源和防治等进行分析和探讨,以求从根本上消除爆炸性气体所带来的危害。
1 尿素中压系统爆炸隐患分析
1.1 爆炸性气体的来源
尿素生产中所用的CO2来源于变换气脱碳后的解析气。不论采用什么方法脱碳,在脱碳液吸收CO2的同时,还溶解了一定量的CO,H2,CH4及N2等。当脱碳溶液再生时,这些气体随同CO2一起被解析出来,进入CO2气中。根据有关设计资料数据,尿素原料CO2气组成见表1。
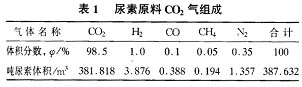
为了设备、管道防腐,在原料CO2中需加入一定量的O2,一般加O2量为0.5%,原料CO2气加O2后的组成见表2。
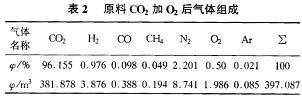
液氨也是生产尿素的原料,生产中液氨会溶解一些H2,N2,CH4及Ar等气体,设液氨在压力2.1MPa(绝),温度30℃条件下送往尿素装置,溶解于液氨中的气体(按吨尿素590kg氨计)组成见表3。
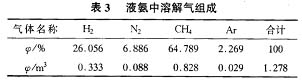
这些气体随CO2气及液氨带入尿素装置反应圈,其中除CO2在尿素系统参加反应外,其余气体均不参加反应,称之为“惰性气体”。在尿素系统CO2与氨生成尿素后,惰性气体被留下来,且得到了“浓缩”,在到达中压系统的氨冷凝器、惰性气体洗涤器内时逐渐达到最高浓度。根据表2及表3所列的气体组分,到达中压系统的惰性气体(不计NH3,H2O)组成见表4。
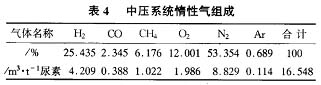
根据表4中惰性气组分,在尿素中压系统氨冷凝器及惰性气洗涤器操作条件下的尾气组成见表5。
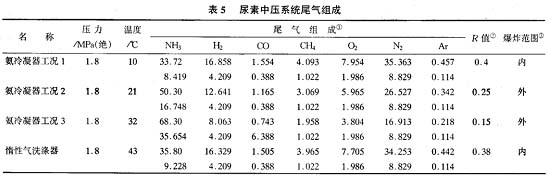
惰性气体中的H2,CO,CH4等气体具有可燃性,在一定条件还会引起爆炸。由(H2+CO+CH4)/(NH3+H2+CO+CH4)算出的比值,可确定气体是否处于爆炸范围。由表5计算的R值查图可知,当氨冷凝器操作温度在10℃时,氨冷凝器内的气体己处于爆炸区域之内。提高氨冷凝器的温度,如21℃及32℃时,由于气体中NH3含量的提高,R值缩小,使气体处于爆炸范围之外。为保证氨冷凝器的安全,氨冷凝器只有在较高温度下操作。但在惰性气洗涤器内随着氨含量的降低,其气体组分仍处于爆炸范围内。由此可知,尿素中压系统的爆炸隐患始终是存在的。
注:①表5中尾气组成各项数值上行为体积分数,%;下行为标准状态下的体积,m3。
②R=(H2+CO+CH4)/(NH3+H2+CO+CH4)
③查年产4万t水溶液全循环法尿素装置操作手册“NH3—H2—N2—空气混合物爆炸区域图”
1.2 爆炸条件的存在
气体处于爆炸范围只是引起爆炸的一个方面,引起爆炸还应具备诱发爆炸的其他因素,这些因素有:①O2的存在;②火源。
H2,CO,CH4等爆炸性气体的爆炸,实际上是在一定条件下这些气体与O2发生激烈的化学反应而引起的。O2的存在是引起爆炸的不可缺少的因素。由于尿素装置防腐蚀的需要,在CO2中加入了相当于气体总体积0.5%的氧,这些O2到达氨冷凝器、惰性气洗涤器等设备时含量已相当高了,这就为气体爆炸创造了“物质”上的有利条件。
爆炸性火源产生于尿素装置以下几个方面:①冲击产生的火花;②气体高速流动中摩擦产生火花;③静电产生火花等。虽然上述情况由于设计上采取了一系列措施,一般不易发生,但爆炸隐患在所难免。
1.3 尿素装置典型爆炸事故
自1966年以来,我国尿素厂家中压系统所发生的严重爆炸事故统计见表6。这些爆炸事故不仅造成企业巨大的财产损失,同时带来了人员伤亡,对工厂及职工造成严重创伤。
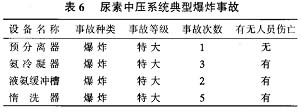
2 尿素中压系统爆炸隐患的防范措施
为了防止气体爆炸,我国自行设计的水溶液全循环法中小型尿素装置都采取了一些防爆措施,这些措施主要有以下几种。
(1)防止爆炸组分的形成 ①向系统补入空气替代补纯O2,增加N2气带入量,以冲稀尾气中爆炸气体浓度,使中压系统中尾气爆炸范围缩小,降低爆炸危险性;②向中压系统补入N2气,使尾气中O2含量降至4%以下,成为非爆炸性组分;③控制中压系统设备温度,提高气体中氨含量,使气体处于爆炸范围之外。
(2)防止火源生成 ①防止静电产生,如将设备、管道、仪表等可靠接地;②改进中压系统压力调节系统,防止因压差过大,气体流速过快发热而产生火花。
(3)在惰性气洗涤器内设置防爆板,当发生气体爆炸时,设备内防爆板被损坏,以避免设备壳体损坏而造成重大事故。
上述防爆措施在我国中小型尿素装置中起到了积极的防范作用,但由于管理、维修的疏漏,操作的失误等原因还是造成了多次特大爆炸事故。原料CO2气脱H2技术就是在这样的背景下产生的,该法可以从根本上消除爆炸隐患。
在催化剂作用下,将尿素原料气中的H2,CO,CH4等具有爆性的气体,在很低浓度的条件下加以去除,从而使尿素中压系统尾气中爆炸气体组分始终达不到爆炸所需的浓度,即使有火源也不会产生爆炸。
脱H2实际上是使CO2气中的H2,CO及CH4等可燃气体与O2反应而除去,而O2是以补入空气的方式补入系统。根据表1气体组成,脱氢所需空气量为:
H2燃烧反应耗O2量=3.876×1/2 O2=1.938(m3)
CO燃烧反应耗O2量=0.388×1/2 O2=0.194(m3)
CH4燃烧反应耗O2量=0.194×2 O2=0.388(m3)
3项耗氧量合计为2.52m3。与O2一同带入的N2为9.469m3,Ar为0.011 m3。脱H2前后原料CO2气中气体组成变化见表7。脱H2后CO2气体与液氨释放的气体到达中压系统时的组成见表8。
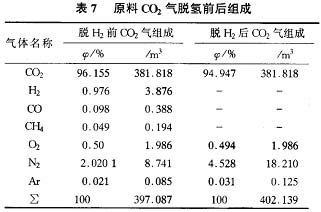
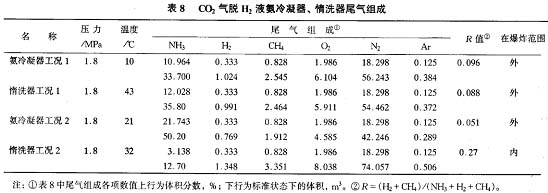
表8与表5相比,同样氨冷凝器在10℃下操作,惰性气洗涤器在43℃下操作,表5中两设备的尾气均在爆炸范围内,而表8中(第1种工况),由于采取了脱H2技术,氨冷器和惰洗器中的尾气都远离了爆炸范围,即使有火花也不会产生爆炸,可以说实现了真正的安全。
表8中第2种工况属于开停车工况(同表5中工况2),脱H2后尾气组成在爆炸范围之外,亦即在安全生产范围内,扩大了主要调节参数及操作范围的限度(如CO2气中O2含量,出惰洗器的氨水浓度及温度等)。
3 CO2原料气脱氢及精脱硫技术的应用
3.1 CO2脱H2技术的应用实例
尿素CO2原料气脱H2技术在大型尿素厂应用较早。由于脱氢催化剂最早由国外公司开发,价格昂贵,且需要进口,国内设计的尿素装置大多采用煤制气,CO2原料气中硫含量高,当时CO2气体精脱硫技术还未开发成功,故国内设计的尿素装置均未采用脱H2技术。20世纪90年代,湖北化学研究院在CO2脱氢催化剂的研制、脱氢工艺技术的开发、CO2精脱硫技术等方面取得了突破性进展,先后开发出TH-2、TH-3型脱H2催化剂,并在全国大中小型尿素厂推广应用,取得了预期效果。表9列出了利用湖北化学研究院技术进行尿素CO2气脱氢、精脱硫的应用厂家。
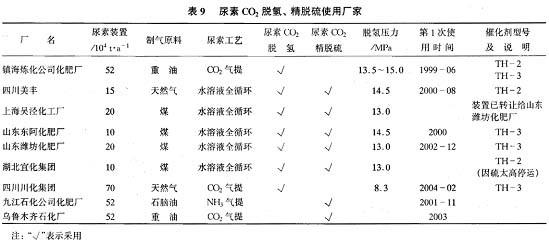
有关厂家脱氢操作数据见表10、表11。表10是镇海炼化公司化肥厂第1炉TH-2脱氢催化剂使用总结报告数据(该厂已使用3炉脱氢催化剂)。该炉催化剂从1999年6月24日投运,至2000年7月16日(总结之日)已运行1年,共经历了4次停车,6次高硫冲击(表10中残H2含量高是因为高硫冲击所致),几次高硫冲击中最高硫含量达16.1mg/m3,高硫冲击时催化剂活性下降,待硫含量回到正常值,催化剂活性即恢复,残H2又达到指标以内,证明催化剂性能是好的。表11为四川美丰化工股份有限公司第1炉TH-2脱氢催化剂使用1年的总结报告数据。
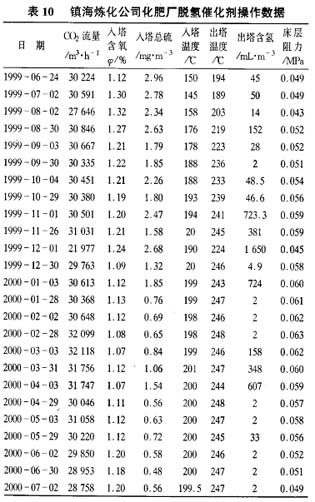
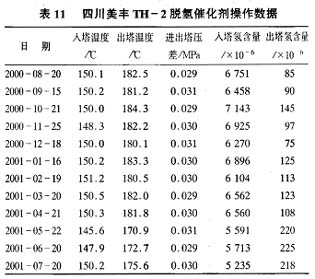
该厂CO2气H2含量维持较高,一般在100×10—6左右;该厂的目标是残余H2<300×10—6,以节省因加热气体消耗的热量。该炉催化剂使用1年后的活性稳定,出口CO2中残H2没有大的变化,入口温度仍保持在150℃。需要说明的是,2001年5月以后由于脱氢塔“副线内漏,少量CO2未经脱H2装置,致使气体中H2含量升高”(总结资料语)。该炉催化剂一直用到现在。
3.2 尿素CO2原料气脱H2工艺流程
3.2.1 脱氢原理
CO2原料气脱H2工艺中包括CO2气精脱硫、除油,加热、脱氢等部分。如前所述,CO2脱氢是在脱H2催化剂作用下,使CO2气中的H2,CO,CH4等可燃性气体与O2反应生成H2O和CO2,从而达到脱除爆炸性气体的目的。
2H2+1/2 O2→2H2O
CO+1/2O2→CO2
CH4+2O2→CO2+2H2O
3.2.2 工艺流程
脱氢工艺流程见图1。从CO2压缩机来的CO2气,经提温气体温度达到脱H2催化剂所需温度(150~220℃),而后进入脱氢反应器,CO2气中的H2,CO,CH4等可燃气体在催化剂作用下与O2反应。出脱H2反应器的CO2气中残余氢含量<100×10—6。出反应器的CO2气体因H2等气体的燃烧使其温度升高,温度升高多少视H2等可燃气含量而定。出反应器的热CO2气经冷却后去CO压缩机或直接送往尿素合成塔。
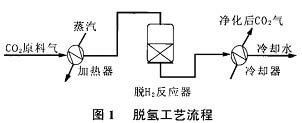
脱氢装置可设在CO2压缩机段间,也可设在压缩机的最后一段。装置设在段间的优点是:一般段间温度较末段高,可节省加热消耗的热量;同时可利用压缩机段间冷却器、分离器等设备,减少设备投资及冷却水消耗。具体放置位置应根据各厂的具体情况而定。
3.2.3 尿素CO2除油及精脱硫
尿素CO2压缩机后续各段均采用无油润滑,脱氢装置一般均设在无油润滑段,以减少除油的麻烦和节省投资。CO2脱氢催化剂是钯、铂等贵金属催化剂,价格比一般催化剂高得多。这种催化剂对硫化物等毒物十分敏感,少量的硫化物就能引起催化剂活性下降甚至失活。实践证明,当原料气中总硫<2×10—6时,催化剂寿命仅为1年;总硫<0.5×10—6时,催化剂寿命为2年;总硫<0.1×10—6,催化剂寿命可达3年以上。可见CO2气的精脱硫对脱氢催化剂的寿命至关重要。
我国中小型氮肥厂主要以煤为原料制气,变换气中硫含量都较高,一般多在100~200mg/m3,即使一些厂增加了变换气湿法脱硫,气体中硫化物也在10~20 mg/m3。这些硫化物经过脱碳,最后都富集到了CO2气中,致使CO2气中硫含量很高。因CO2脱硫难度大,过去的脱硫技术达不到精脱水平,故国内以往设计的水溶解全循环法尿素指标规定,进入尿塔的CO2气总硫含量为10 mg/m3。这是受到当时脱硫技术水平的限制。
20世纪90年代前,我国在中型尿素厂也尝试过使用CO2脱氢技术。当时CO2气脱硫采用低温氧化铁加氧化锌工艺,脱硫效果很不理想;再加上氧化铁强度低,粉尘带入往复式压缩机,造成压缩机气缸严重磨损,脱氢装置很难维持,运行半年后便停运。
CO2与硫化物均属于酸性气体,在脱硫过程中具有竞争吸附的特征,这就为CO2气精脱硫带来了很大的困难。20世纪90年代,湖北省化学研究院成功开发出用于CO2气常温精脱硫的脱硫剂及其工艺,解决了高浓度CO2气条件下的精脱硫难题。此后在全国食品级CO2、尿素CO2原料气中得到推广,并取得了满意的效果。精脱硫后CO2气中总硫可达<0.1×10—6。CO2气精脱硫技术的突破为我国CO2气的广泛应用起到了促进作用。CO2气精脱硫也为CO2气脱氢技术的推广创造了条件,并成为CO2脱氢的主要组成部分。尿素CO2气精脱硫不仅有效地保护了脱氢催化剂,延长了催化剂寿命,同时减少了硫对尿素系统的设备、管道腐蚀,从另一方面对保障安全生产起到了重要作用。
4 经济效益
4.1 脱H2的经济效益
由于采用CO2脱氢技术,合成尾气形成不了爆炸气体,从而可降低高压洗涤器温度,使尾气中放空氨含量减少。据实际考察,每吨尿素可减少2kgNH3的损失。
以镇海炼化及四川美丰为例,镇海年产尿素52万t,美丰年产尿素15万t,两厂各用TH—2型脱氢催化剂0.93m3和0.502m3。镇海节氨 520 000×2/1 000=1 040(t/a)美丰节氢 150 000×2/1 000=300(t/a)
设每吨氨售价1 500元,每年产生的价值为:镇海 1 040×0.15=156(万元);美丰300×0.15=45(万元)。两厂一次性投资(设备费、工艺管道安装费及催化剂费)镇海为64万元,美丰为38万元,投资回收期分别为0.41年和0.84年,产生的经济效益分别为:镇海156-51=105万元,美丰45-11.5=33.5万元。式中,镇海、美丰51万元、11.5万元为年消耗费(包括每年的设备折旧费、催化剂消耗、加热蒸汽消耗及人工费等)。
4.2 精脱硫的经济效益
CO2气精脱硫不仅有效地保护了脱氢催化剂,延长了催化剂使用寿命,同时由于CO2气中硫化物由10 mg/m3脱除至0.1×10—6,降低了对尿素系统设备、管道的腐蚀。生产实践表明,由于CO2气中硫含量高而引起CO2压缩机、二段蒸发加热器等设备的腐蚀,轻则引起停车,重则更换设备。有人对以煤和以天然气为原料的尿素装置二段蒸发加热器的腐蚀情况进行对比,分析发现,在一些以煤为原料的尿素厂,二段蒸发加热器的寿命通常只有1~2年,而以天然气为原料的尿素厂二段蒸发加热器根本就不存在腐蚀,使用若干年后都不更换。其原因与两者CO2气中硫化物含量有关。以天然气为原料的CO2中硫含量仅为0.1×10—6,两者相差70倍。一个10万t/a尿素厂更换1台二段蒸发加热器需要10万元以上。有的厂因CO2压缩机气缸受到腐蚀不得不停车检修,被迫停产或减产,对工厂造成很大损失。可以说,CO2气精脱硫可为企业带来可观的经济效益。
