[摘 要] 论述了双甲(醇烃化)工艺因地制宜设计的几种类型工艺及不同的设计压力和工程的有关配置方式,介绍和分析了对工程问题的思考方法及处理问题的方式,并对各种模式的工程设计进行了较详细介绍和经济效益、环保效益的初步分析。
[关键词] 双甲工艺;醇烷化;醇烃化;工程设计;分析
0 前言
获得了国家科技进步二等奖的技术——合成氨原料气双甲净化精制工艺(简称双甲工艺或醇烷化工艺)为我国自主知识产权的发明技术,是以谢定中教授为首的湖南安淳高新技术有限公司技术人员经过近二十年的不懈努力创造的技术。
从1992年第一套工业化装置在湖南衡阳市氮肥厂投运到现在,安淳人经过多次对技术的工业化适用性、工艺配套的节能性、工程设计的可行性及工艺优化等方面进行了大量的工作,经过了几次大的技术提升,几次大的完善性技术改造,创造了多种适应于不同生产类型、不同生产厂家和不同生产条件的工业配套模式,极大地丰富了本技术的可适用性,也大大地节约了技术受让厂家的工程投资,创造了更大的经济、社会效益及环保效益。到目前为止,双甲工艺及提升技术——醇烃化工艺已经在全国中、小合成氨企业推广达40余家。已经投用了的每一个厂家都有其工程设计及技术实施方法的独特性,笔者作为技术开发者之一,长期进行本技术的推广和配套工作,特撰文以总结之。
1 双甲(醇烃化)工艺的基本原理
1.1 双甲(醇烷化)工艺基本原理
双甲工艺——甲醇化反应串甲烷化反应,即以甲醇化反应来脱除脱碳工段后的工艺气中的CO+CO2,达到0.03%~0.3%,再以甲烷化反应将此气体精制到15×10-6以下,完成对合成氨原料气的净化精制。其基本方法是在合成氨原料气的净化精制中,在一定的压力和有关工艺条件下,先以甲醇化反应来净化合成氨原料气,将其中部分的CO+CO2和H2反应生成甲醇产品,同时也使工艺气体得到了净化。这时原料气中绝大部分的CO+CO2被脱除干净。再将气体送入甲烷化工序进行精制,精制后达到CO+CO2总量在(5~15)×10-6,最终获得了可进入氨合成工序的合格原料气。
反应同样以CO+CO2与H2作为原料,生成了CH4。但反应主要目的是精制合成氨原料气——将甲醇化后的只有很少量的CO+CO2进行脱除。为了减少精炼气的放空量,我们要尽量使进入甲烷化中的CO+CO2少,这也是双甲工艺中比较注重的工程技术问题。
1.2 双甲工艺的升级技术醇烃化反应基本原理
醇烃化反应是为了降低原料气中的H2耗量。因甲烷化反应的反应生成物全部为CH4气体,这种惰性气体要在合成工段放空,增加了合成工段的气耗和电耗。我们创造了一种催化剂来取代甲烷化催化剂对工艺气体进行精制,这种工艺我们称之为醇烃化精制工艺。反应是在精制反应器内的催化剂床中完成的,大部分气体中的CO+CO2和H2进行了醇化反应,少量的气体进行了烃化反应,生成了多元醇类和极少量烃类和水的混合物,达到以液态副产品输出方式的目的,使合成工段的循环气放空量基本不增加。这种副产品可进入甲醇精馏工段回收完多元醇类产品后再和甲醇精馏后的残液一道作为燃料使用。或直接将醇烃化液作为燃料使用。也就是说醇烃化反应为大部分是液态的副产品输出,而甲烷化反应则是以气态的副产品输出的方式。
由于碳原子在分子中以多碳结构存在,也就是说碳原子形成了“链”,这样的分子结构形态就可以减少H2的耗量。通过多次优化,我们不断改进醇烃化催化剂的配方,目前通过醇烃化精制生产出来的副产物主要成份为:水39%,甲醇33%,乙醇15%,其他多元醇13%。
由于是液态取样,生成的甲烷及其他常温下挥发的二甲醚类等物质未分析出来。采用这种催化剂,醇烃化的出口物质大部分为醇类物质。这些物质是完全可以燃烧的,无毒,可以作为清洁燃料使用的。2 几种典型的双甲(醇烃化)工艺的工程设计模式
2.1 不同压力级组合的设计模式
2.1.1 等压力级的双甲净化工艺设计模式
双甲工艺发明之初,1992投产的湖南衡阳氮肥厂是世界上第一套双甲工艺,当时国内的常温精脱硫技术尚未进入工业化,我们采用了甲醇塔内置高温氧化锌精脱硫剂的方式来进行精脱硫,将高温氧化锌放置在甲醇化合成塔催化剂的上部。由于当时甲醇市场较好,我们工程设计中采用了双塔可“串联”可“并联”运行的甲醇化工序设计方式,生产中将变换出口气的CO提高到了5%以上,得到了甲醇产量较高,甲烷化精制效果也好的结果。
后来再经过优化设计,也有了湖南郴州地区桥口氮肥厂、山西丰喜集团临猗分公司、湖南湘阴氮肥厂、吉林梅河口化肥厂等厂都采用了这种在12.5~15MPa级等压力级条件下的双甲工艺模式。
本流程比较适应于原来厂家已经有这一压力级的联醇岗位,也适应于由铜洗改造成双甲工艺的单位。可以在压缩机“五出”或“六出”总管上由原来进入铜洗工段的管道上接双甲工艺,不需要再设置压缩机出口总管,也适应于以净化精制合成氨原料气为主的单位。况且,目前的铜系甲醇催化剂已经能在这个压力下获得很高的转化率,我们认为再提高压力也不会使甲醇化的转化率提高很多。基于此,如果是以净化为目的而设双甲工艺的厂家,我们首先推荐这种模式来完成工程设计,后来如山西晋丰集团高平化肥厂、山西晋丰闻喜化肥厂、江苏华尔润化工有限公司、山东德齐龙化工有限公司等厂均采用了这种配置方式。
这种配置工艺的最大优点是甲醇化后的气体不要经过压缩,减少了压缩油污染的气体对甲烷化或醇烃化催化剂的影响;其二,醇化系统设在一个压力级便于两工序循环机的共用,也便于操作管理;其三,可以利用甲醇化的反应热来加热醇烃化或甲烷化的入炉气体;其四,可利用原铜洗的高压设备改作甲烷化或醇烃化设备。
另一个要注意的是由于甲烷化催化剂对甲醇和二甲醚等类物质比较“敏感”,会影响其反应活性,因此,如果是采用甲烷化反应来进行精制(醇烷化工艺),则必须要考虑在甲醇化后设一个洗醇岗位,以软水来洗净尾气中的微量甲醇和二甲醚,达到保护甲烷化催化剂之目的。 这种配置的典型流程图1。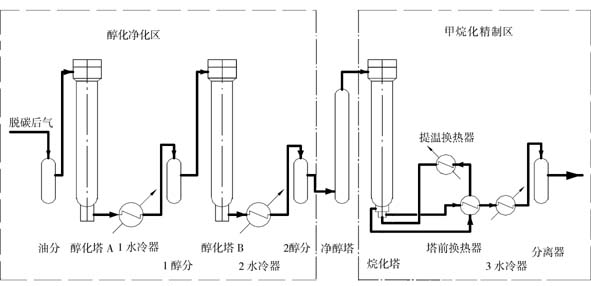
图1 醇化或烷化等压力下的双甲工艺流程
2.1.2 与氨合成系统等压力级的双甲净化工艺设计模式
当建设方有部分高压设备可供利用,而双甲工艺又是以净化为目的运行方式时,我们也考虑双甲工段和氨合成压力等压的流程进行系统设计。
这种方式特别适应于氨合成系统改造和净化精制改造同时进行的工程,如我公司在2001年为邯郸钢铁集团公司化肥厂等厂设计的系统。当时,厂家正要进行DN1600氨合成系统改造,原来的氨合成系统有很多设备可供利用,我们为此设计了一套醇化系统和甲烷化系统均为32MPa的双甲净化精制系统,醇化和烷化运行压力均为32MPa,这个压力和氨合成系统压力一样。装置运行近6年了,目前运行状况良好。后来相继有部分厂家也运用了本设计方式进行系统配套。
这种设计方式的优点之一是可利用原来氨合成的旧设备,不需要将原设备以降低使用压力的方式进行使用,可提高催化剂的利用率,也可以提高甲醇化的能力;优点之二,是在高压下运行,催化剂使用“空速”可适当提高,系统热利用也高,热损失相对也较小,还可以提高一些反应速度;优点之三,是经过双甲工艺后的气体不需要再经过压缩机来增压,减少了气体被压缩机油污染的机会,更大程度地保护了氨合成催化剂。缺点之一,当产醇量较高时,将会使使制醇气体压缩功耗比在中低压下的压缩功耗增加,经过计算,生产1吨甲醇的原料气,由12.5MPa压力级压缩到26MPa压力级,压缩机将增加电耗53 kW·h;缺点之二,不能认为提高醇化反应压力可以较大幅度地提高甲醇化的转化率,也就是说,10MPa以上的甲醇化反应,利用目前铜系催化剂,转化率提高也相当有限了,相反还会增加甲醇反应的副反应,使产品甲醇的品质受到影响。
本工艺的基本流程与图1一样。
2.1.3 在12.5~32MPa压力级任一压力下等压下的醇烃化净化精制工艺
按2.1.1和2.1.2的配置方式设计的双甲系统,同样适用于醇烃化工艺。我们在2000年后,为了提高双甲工艺的技术水平,减少能量消耗,提高气体利用率,创造了醇烃化工艺。工艺先期是采用醇化后串烃化的方法,这种烃化反应主要是利用一种烃化催化剂来实现。烃化产品由于反应选择性强,要求温度控制在一定的范围。为了更有其工程可行性或实用性,后期又创造了更加方便的甲醇化再串醇烃化的工艺方式。也就是说,在原来装甲烷化催化剂的反应炉内,换装上醇烃化催化剂(这一种催化剂同时完成醇化和部分烃化反应的催化剂,故称之为醇烃化)。这样即达到了尽量多产有用的醇类产品的目的,也可以使深度精制达到合成气的要求。
醇烃化技术基本原理是利用甲醇工序对合成氨原料气进行醇化反应并副产甲醇产品,同时对气体中的CO+CO2进行初步脱除(甲醇化),再利用醇烃化工序的醇烃化反应进行合成氨原料气的进一步精制,并副产醇类物和烃类物的混合物等有用的常温下可分离的物质。工艺的第一步是将CO+CO2首先转化为CH3OH,使CO+CO2 下降至0.03~0.3%;第二步是将少量CO+CO2在醇烃化反应器内转化为低碳烃类物、低碳醇类物、甲醇和少量甲烷,最后使精制气中的CO+CO2小于10×10-6,再进入氨的合成工序。这种工程设计可取消醇化后的净醇处理工作,简化了流程,降低了消耗量。
我公司在山东德齐化工有限公司的两套“1830工程”、天脊集团晋城化工公司等厂均采用了这样的设计方式。流程见图2。
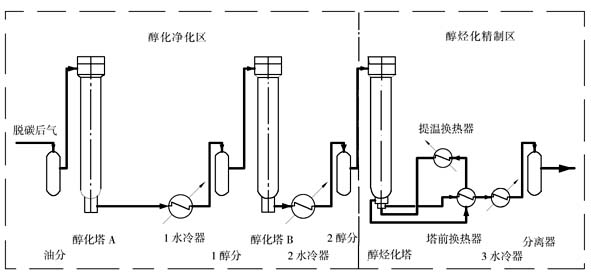
图2 甲醇化和醇烃化等压力下的醇烃化工艺流程
2.1.4 不等压力级的双甲(醇烃化)设计模式
醇化工序或甲烷化(醇烃化)工序可以在一个压力级下进行,但也可以按工厂实际情况进行分级分不同的压力下进行。如我公司为河南心连心、湖南岳阳、湖南衡阳、瑞星化工有限公司、江苏新沂恒盛化工有限公司、河南心连心化工有限公司等多套改造工程的醇烃化工艺,为江苏华昌化工有限公司、山东德齐龙化工有限公司的高产量甲醇联醇烃化工艺均采用了不同型式的不同工序的不等压的设计方式,这些厂家均收到了很好的效果。
还有一种方式是将一级和二级甲醇化反应放在一个压力级,将甲烷化(或醇烃化)放置在另一个压力级。流程中只有一个区别是当采用甲烷化进行精制时,必须在甲醇化后设一个醇洗工序,用以去除相应温度下分离不出来的甲醇及二甲醚。由于甲醇化后的气体要再次进入压缩工序,也要采用除油处理方式来保证醇烃化或甲烷化的催化剂安全。典型的流程见图3。
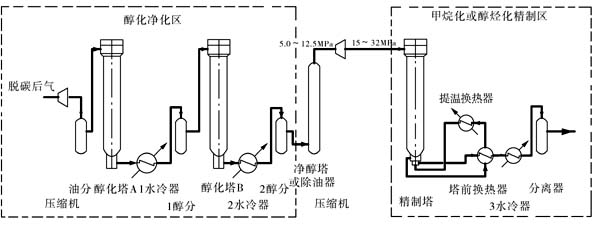
图3 二级醇化等压力甲烷化或醇烃化不等压力的流程
图3所示的这种流程的优点是,二级甲醇化均在同一个压力级进行反应,已经有联醇及联醇设备的厂家改成双甲工艺时,可不用费较大的工程量。
这种流程的甲醇产量可以做得较大,二级甲醇化的碳CO+CO2的转化率也可以达到很高(二级甲醇化后的CO+CO2可达到0.03%),二级甲醇可共用循环机,并且甲醇化塔“可串可并”,可以一塔操作,一塔更换催化剂和升温还原,当甲醇产量较低时,也可以一个塔生产、一个塔备用,调配十分方便。
保证将较好的催化剂活性的塔设在二级甲醇化,保证了二级甲醇化对原料气的深度净化的要求。
甲烷化或醇烃化如果设在更高一级的压力级,可使用退下来的旧的氨合成系统设备,使甲烷化催化剂或醇烃化催化剂使用量变少,精制度提高,也有利于从合成系统取热来供甲烷化炉或醇烃化炉。
这种流程的缺点是流程相对较长,在甲醇化和甲烷化中要设除油或净醇工序,多设的各级不同的压力,也给生产管理和操作带来了一定不便。
这种流程的缺点是流程相对较长,在甲醇化和甲烷化中要设除油或净醇工序,多设的各级不同的压力,也给生产管理和操作带来了一定不便。

图4 二个醇化塔的操作压力不相同,精制塔与第二级醇化等压力的流程
图4所示流程是最近我们在山东德齐龙化工有限公司研制投用成功的一种全新的、产醇量大、净化精制度高,调节十分方便的流程。
这种流程的优点是产醇量可以做到很大,生产1吨甲醇可副产高品位蒸汽(蒸汽压力3.9 MPa)1.4~1.5t,只要将产生的蒸汽在其他岗位进行过热后,就可以进行差压发电,发电后的背压蒸汽还可作工艺用汽,可获得很好的经济效益。
第一级甲醇在低压力下完成,有效地节约了压缩功耗。这也是非常符合我们提出的产醇在低压下进行、净化精制在高压下进行的工艺理念。
这种流程的另一个优点是第一级甲醇化塔产醇量无论多大,因是采用3.9MPa压力级的饱和水来调节催化剂床层的温度,比传统的气气换热的反应器调温方便,操作安全性强。但这种流程不太适应于产醇量小时的工厂,如果用这种流程,第一级醇化塔的投资较大,流程也较长。
当然,也可以将第一级甲醇塔设为普通的气气换热方式的反应器,虽然回收的蒸汽量较少,蒸汽品位较低(0.2MPa左右),但却比较适应于目前很多厂家已经有这一级压力的联醇系统,也有相当成熟的操作经验。但我们认为,从产醇塔的反应机理上来看,不主张大量生产甲醇的塔用冷激式降温的方式来制造反应器,这样对热回收、对降低循环量、对保护甲醇催化剂和提高产品甲醇的品质等方面均没有好处。
2.1.5 不同压力级分配的双甲工程设计小结
安淳公司的设计者们从工厂的实际出发,采用我公司的专利技术,按照双甲(醇烃化)工艺的特点,十多年来为用户设计了近40多套净化精制工艺,曾经运用了各工序的多种压力级配置的设计方式。有“等压”的双甲流程、也有“等高压”的双甲流程、“非等压”的双甲流程和甲醇不等压,甲醇与醇烃化也不等压力级的“非等压”流程。至于各工序的压力级如何配置,要依照催化剂和反应条件进行流程配置。换言之,无论采用何种压力级进行工序配置,目的要使反应器和催化剂发挥最大效益、要使系统能力达最大化、安全化、要使系统流程最为简化,最终达到最好的综合效益。
2.2 不同产出物的工程设计方式
双甲工艺有二个或三个反应器,每一个反应器均要在有催化剂条件下进行反应,主要原料为CO+CO2和H2。而这些原料是组成碳氢化合物的基本原子,如果我们运用不同的反应条件和相应的催化剂,理论上来讲,可以得到多种有机反合物。
目前最为成熟的方式可以得到甲醇和二甲醚及甲烷或多元醇烃类物质。如果进一步研究也可以得到汽油的替代物,我们在双甲工艺中采用了不同的催化剂,也创造了几种产品生成物的设计方式。
2.2.1 生产醇醚燃料的双甲工艺
1996年在湖南湘阴氮肥厂的双甲工艺改造中,在甲醇化炉内放入我公司研制的醇醚催化剂,生产出了醇醚混合物的副产物。并用这种物质进行了作民用醇醚燃料的推广工作,取得了可喜的成果。也为一步法合成二甲醚进行了前瞻性的工作,目前正在进行“一步法”生产二甲醚的深入研究工作。
如果再采用相配套的精馏方式,可以同时得到甲醇和二甲醚两种产品供应市场。这种工艺方式为甲醇类厂家生产二甲醚提供了经验,也为利用本系统流程生产其他碳一化工类产品提供了经验。工艺流程见图5。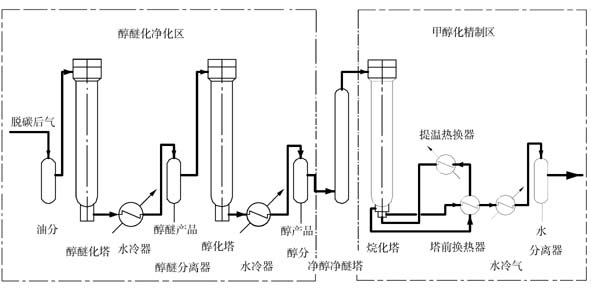
图5 甲基化产二甲醇及醇类混合物的双甲净化精制流程
这种配置方式的优点是为小型化肥企业,特别是产碳铵的企业在肥料销售淡季可提供甲醇或醇醚原料产品选择。
2.2.2 将甲烷化炉内催化剂换成醇烃化催化剂将得到优质燃料的精制工艺
如图5的流程一样,如果将甲烷化塔内的催化剂换成醇烃化催化剂,或将其催化剂配方优化,或生产出多元醇产品的优质燃料,将其中的甲醇等类物质精馏出来,可更进一步得到甲醇产品。也就是说,甲烷化精制生成的副产物为气态的甲烷,这种甲烷只有随气体进入氨合成工段以放空的形式排掉;而醇烃化精制生产的副产品绝大部分为液态的多元醇类产品,这种产品可用以代替液化气作为燃料产品出售,因而它有更高的经济和环保效益。
这种产出物也可作为燃料进入锅炉或造气系统烧掉。还可以将液体送入甲醇的精馏系统,回收其中的33%的甲醇后,其余物质随甲醇精馏的残液送入锅炉或造气系统烧掉。
这种产品工艺改进的方式直接带来了原料气中的H2消耗量比同样条件下甲烷化反应的H2消耗下降近24%,也使合成放空量减少80%。
这种方式是基于我公司创造的醇烃化催化剂技术,在一定条件下设置工艺,主要目的是减少原料气消耗。
2.3 采用不同的醇氨比设计的双甲工艺
安淳公司在上世纪90年代初期,已经申请了一个可调醇氨比的双甲工艺的技术发明专利技术,它的核心内容是运用两级甲醇系统的工程设计方式,第一级甲醇系统着眼于多产甲醇产品,第二级甲醇系统立足于对原料气进行深度净化。这样整个工序运行可以十分安全地应付甲醇产量的变化或气量的变化,催化剂在初期、中期和未期均能十分方便地调节系统,达到系统始终处于高效节能的运行状态。
我们的工程实践中,有的单位醇氨比达到了1:2(湖南衡阳市氮肥厂,山东德齐龙化工有限公司)或更高,而以净化为目的的厂家醇氨比仅只有1:20(山东德齐龙化工有限公司、邯钢集团化肥厂、河南心连心化工有限公司等厂),这些厂家系统运行安全十分可靠。进入烷化或醇烃化的气体中的CO+CO2量也在0.3%以下,最小的可达0.03%。当然,甲烷化或醇烃化的外供热也相应增加了一些。
2.4 精制工序的不同的外供热的设计方式
通过醇化串醇烃化或甲烷化各反应器的热量衡算及工程实际证明,采用甲烷化反应方式作为精制时,要达到甲烷化炉内的反应热量平衡,通常的控制指标是让进甲烷化炉内的CO+CO2量大于0.7%;进入醇烃化炉内的CO+CO2量要大于0.5%(因醇烃化反应比甲烷化反应的温度低)。
如果采用这样的成份入甲烷化炉内,将会有较多的CH4生成,也会增加原料气的H2的消耗量。造成合成工段的放空量增加;如果进入醇烃化工段,也会使副产的多元醇类产品增加,造成精馏的负荷增加,工程上要尽量降低这个指标,将有效的气体多生产甲醇类产品。
我们一般是将进入醇烃化或甲烷化的CO+CO2这个值定为0.03%~0.3%,这样势必在精制工段要采用外供一部分热量来保证反应器运行正常。当然,如果生产的是人造汽油产品或生产的是畅销的民用燃料产品,我们会要求产品产量愈高愈好,那时,工艺上也将会有个较大的调整。
以年产100kt氨副产31.3kt粗醇为例:变换气中CO 4.31%,原料气中CO 5.95%、CO2 0.31%,醇后气CO、CO2含量与补充热(以电功率计算)的关系如表1。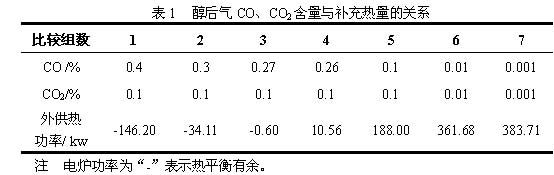
由表1看出,不计热的损失,也不考虑有水冷却器部分的热量损失的条件下,只考虑反应平衡的条件下,CO+CO2为0.37%时(3组)不需外供热,但CO+CO2下降为0.36%时(4组),需外供热10.56kw;CO+CO2降至0.2%时(5组),外供热增加188.00kw,即成份(CO+CO2)下降44%,外供热增加16.8倍,随着CO+CO2的降低,外供热随之增加直至CO+CO2为0.002%时,外供热(电)达到383.71kw。
一般来说,要维持低组分下的反应热平衡,尽量要降低进入水冷却器的气体温度,也要提高催化剂活性,提高较化率,更不能开用循环机,开了循环机将会使系统的热损失更大。也要尽量降低系统的热损失,才能够以最少的外供热量来实现热平衡反应。当然工程实际中要考虑多种因素,因而要充分留有余量来设计系统。
双甲工艺的工程设计中,我们采用多种方式向系统补热。
2.4.1 用发电蒸汽取热的方式
这种方式是采用一个蒸汽加热器来加热甲烷化或醇烃化炉进口气体,过热蒸汽的温度要在260℃以上,工艺只需将精制塔进口气的温度由190~200℃加热到210~220℃(采用醇烃化精制时入口温度,当用甲烷化时,温度至少要高20℃以上)。
我们在河南心连心化工有限公司、湖南岳阳天润化工有限公司等厂均采用这种方式来补充热量,利用原合成系统的旧废热锅炉来实现本工艺。加热的流程见图6。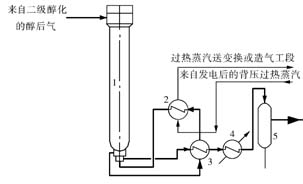
图6 利用过热蒸汽加热精制反应器流程
1—醇烃化或烷化塔;2—提温换热器;3—塔前换热器;4—水冷器;5—水或醇烃化合物分离器
这种流程的优点是间接加热气体,不需要设置一个内外均是耐高温和能承受高压的气气换热器。这种间接加热方法安全可靠;可以利用旧的合成塔出口废锅来改造用之。这种方式必须有过热蒸汽的来源,换热过程是取蒸汽的显热,没有一定的蒸汽流量,也不会使加热过程顺利。
2.4.2 利用变换系统的热量来加热精制塔进口气
当变换为“中变串低变”或“全中变”的流程时,可利用中温变换炉出口的310~400℃的反应出口气,利用传热介质来间接加热甲烷化或醇烃化炉的进口气体。这种流程可在变换炉出口设一个U型管换热器,管外走变换气,管内用走传热介质;同时也在醇烃化或甲烷化炉的进口设一个U型管换热器,管内走高压入口气,管外走热介质,利用热介质的流量来调节加热入炉气。
这种流程相对简单,不是用气气直接换热的高温高压换热器来加热,从而减少了换热器泄漏造成氨合成塔内的催化剂“中毒”危害。但使用这种流程必须要有一个中温变换工序,如果是采用“全低变”的变换工艺,因反应气的温度与甲醇化和甲烷化的反应温度相近,无法用此方法来换热。
2.4.3 利用合成工段的出口气热量来加热精制塔进口气
这种加热的方式我们1996年就在有关文章中提出过,也进行过详细的流程考虑。由于此种方式要增加一个抗氢腐蚀、且能耐高压的设备于合成塔的二出口入废热锅炉的管线中,而换热采用的是气气直接换热的方式,要考虑到很多安全性等问题。为了使内件压差不至于太大而造成内件设计更为困难,最好是将合成压力和精制系统压力设计成一个压力级,从而也限制了使用范围,基于此,我们更多地是考虑用其他方式来取热用于精制塔。
这种取热方式的优点是,可以长期利用合成系统的高温反应热,采用高温反应气来直接加热较低温的未精制气的方式,采用直接的气气换热方式。只要把换热器设计好,系统开停车安全性考虑周到,各管线和阀门用材料考虑周到,基本上是可以稳定地操作运行。
但这种方式的流程很复杂,要用很多抗氢蚀、耐高温的特种管材。为了有利于节约有关特种材料的管线,要求氨合成系统与净化精制系统位置相距不远,也要求氨合成工序和精制塔的反应压力在同一个压力级。
运用这种流程,有多个相关联的换热器,具体是合成的塔外换热器、精制部分的塔外换热器、加上应设的这个跨工序的提温换热器,假若这个运行条件很苛刻的提温加热器一旦泄漏,哪怕是一点小的泄漏,将会造成未精制的含CO+CO2在0.03%~0.3%的原料气进入氨合成工段,造成进入氨合成塔的气体中的微量增高,造成催化剂中毒,氨合成系统的热交换器的热负荷和醇化部分塔外换热器的热负荷也会相应变化。
(流程图略)
同样是在合成塔部分取热,我们也发明了一种间接换热方式——将耐热介质加热后,再通过另外的间接加热器,将热量传热给精制塔进口气的方式。这种方式在我公司设计的河南晋开的醇烃化工程、贵州开磷集团剑江化肥有限公司的醇烃化工程设计被采用。
2.4.4 取造气工段或锅炉工段高温热的方式
在合成氨厂,只要有稳定的温度在300℃以上的热源就可以来加热精制塔进口气体,我们在造气工段的吹风气回收锅炉内,或在锅炉工段的省煤器前设一个加热器,用间接换热的办法,同样利用传热介质来加热精制塔入口气,这也是一种好的方法。但设备设计可靠性研究及工段取热的方便性将被视为工程设计的重点。这些取热方式将视厂家的具体情况因地制宜而选之。
2.4.5 利用适当控制精制塔入口气体成份的方式辅助用电炉直接加热
通过表1可知,当气体中的CO+CO2量达到一定值时,可使外供热量减少或不需外供热,而我们为了降低H2的消耗,尽量要使进入精制塔内气体的CO+CO2量少一些,这就有一个“度”的把握问题,一个优化操作控制的问题。
我们不主张将这个指标降得过低,一般来说,当进入精制塔的CO+CO2量约0.3%就可以了,这样加入的热量也不多,操作也方便。
表2中列出了醇后气成份与气体消耗的关系,通过表2可知,在CO+CO2为0.3%左右时的气体消耗量增加并不很大。综合表1数据分析,只要控制热量损失小,进水冷却器的温度控制低一些,也有可能达到系统的热量反应平衡。
我们设计的正在使用的双甲工艺系统中,很多厂家都采用这种带一定的补充电炉热的甲烷化或醇烃化炉的操作法,只要控制得法,也达到了安全高效的运行效果。一般来说,每吨总氨的补充耗量均小于10kW·h,也不破坏其他工段的热平衡。
这种方式操作简便、投资小、综合效益好。我们第一套双甲工艺在湖南衡阳氮肥厂投产至今已经成功运行了15年,先期为醇烷化工艺,后改成醇烃化工艺,一直采用外供电补热的方式,安全运行这么多年,他们认为采用醇烃化比醇烷化的外供电量消耗小得多。因此,采用醇烃化精制不但可以减少外供热量,减少原料气中的H2耗量,同时还可以得到副产品中的醇,创造比烷化精制更好的效益。
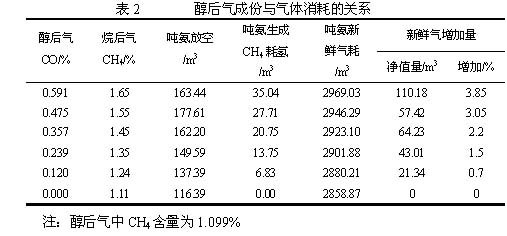
2.4.6 各种取热方式总结
在双甲工艺的工程运用中,我们为了降低原料气中的H2消耗,人为地要将甲醇化后的CO+CO2量控制小一点,让其多在甲醇化系统产甲醇产品。一般来说控制在0.03%~0.3%,这样尽量让有效的气体变成有用的产品,而不要变成“废物”。
但如果甲醇化后的气体CO+CO2指标过低,外供热就会增大,这个指标,醇烃化反应也不能达到“全自热”,更何况醇烷化工艺。因此,必须要采用有效的外供热来实现这一目的。大多数控制方式是将进入醇烃化或甲烷化炉的指标适当化,不一味追求太低的指标,也采用因地制宜的外供热方式,具体供热方式要视方便化程度、投资情况及整个合成氨工艺配备的条件而定,要算经济帐、环保帐。最简单、最经济的取热方式应当是我们所共同追求的。
甲烷化或醇烃化要达到“全自热”,也就是说精制塔全部靠自身的反应热来维持反应平衡,工程中必有一定的入口气反应物组分,才能有一定的能够支付热损失和水冷器降温带走的热量,否则,不论你的换热器做得多好,要达到自热是不可能的。如果要向外工段“取热”,就谈不上“全自热”。
上面列举的各种“取热”方式,我公司均有实施的先例,或正在实施,总的来说,我们认为因地制宜的设计是最适合使用厂家的方式,应该是用户能接受、能给用户带来更好效益的方式。也就是说,工程问题是最具实践性的问题,只有不断结合不同厂家的具体情况进行工艺及设备优化设计,才能使一个好的工艺及技术达到应有的水平。
3 结 语
醇烃化工艺是合成氨的具有革命性的成果,它可使原料气CO+CO2降到(5~15)×10-6。醇烃化工艺除了精制气体功能之外,还利用变换后的CO、脱碳后的CO2副产粗甲醇或醇醚混合物,还可利用醇烃化催化剂生产多优质的民用燃料,生产中完全可实现“零污染、零排放”。
本技术由发明之初的只有一到两种副产品和单一的流程设置方式,发展到现在有各种流程配置方式和能够生产多种副产品的技术。工艺成功地进行了两次技术突破性地“升级”,目前全国中、小合成氨行业有近40家企业使用了这个技术,合成氨净化精制能力由40kt/a总氨到400kt/a总氨均有技术运用,无论是双甲净化精制工艺还是醇烃化净化精制工艺均收到了十分显著的环保效益和经济效益。
本工艺被列为国家级重点科技成果推广项目计划,列为我国合成氨行业的环保节能首先技术项目,获得了国家科技进步二等奖。
安淳公司在设计双甲工艺流程及选择设计中,运用了因地制宜的设计方法,不断优化系统,创造了多种工艺的配置和设计模式,可供同行业人士借鉴。无论在二级甲醇系统的压力级的选择上,各工序压力级的组合上、多种热利用方式的配备上、各工序进出口气的成份控制上,还是在采用烷化工艺或醇烃化工艺的精制方法选择上,都进行了深入的研究和创造了工程实例。
为了更进一步将醇烃化工艺推向更节能、更适用的技术高度,下一步将重点放在工艺配套的催化剂研究上,使双甲工艺可以生产醇、醚或烯烃类基础化工产品,也能够生产汽油的替代品——人造汽油。我们期待着和国内外有关同行合作,为我国的合成氨工业和能源工业创造更多的技术及实用工艺,为净化篮天,创造好的经济效益而更多地工作。