食品CO2是近年来发展迅速的行业,可用于饮料、烟丝膨化、超临界萃取、蔬菜保鲜等领域,传统的食品CO2主要用于饮料行业,由于应用领域的迅速拓展,目前用于饮料行业的仅占食品CO2总销量的30%~40%。据一外国公司介绍,中国的饮料人均年需求量仅为美国的1/2.5,而中国的人口则是美国的5倍,因此中国饮料行业的的销售量应该是美国的12.5倍。据了解,美国食品CO2年销售量为约320万t,中国食品CO2的年需求量将可能会超过1000万t,因此尚有很大的发展空间。过去中国的食品CO2标准很粗放,为与国际接轨、以求高的效益,现在很多食品CO2厂都开始执行国际饮料技术协会规定的质量标准(见表1)。
由表1可知,食品CO2的国际标准十分苛刻,指标共有22项,其纯度要求很高:杂质的含量很低,均为10—6(ppm)或10—9(ppb)级。食品CO2的原料气主要来自氮肥厂、石灰窑厂、发酵厂,由于氮肥厂的气源稳定,故外国公司乐意采用。我中心长期从事化肥催化剂与气体净化剂的研究,10年前就将开发的JTL-1常温精脱硫新工艺(即“夹心饼”新工艺)应用于食品CO2工业并跟踪该工业的发展,结合我国中小氮肥厂煤制原料气的特点,认为上述22项指标中最苛刻的是:总硫(H2S+COS+CS2)≤0.1×10—6;苯含量≤0.02×10—6(即20ppb);总烃含量(以CH4计)≤50×10—6(其中CH4≤20×10—6)。
表2是调查食品CO2厂的原料气(来自以煤为原料的中小氮肥厂)或精制气中总硫、总烃与苯含量的数据,结果表明:
(1)原料气中H2S含量波动很大,为(1~500)×10—6,取定于原料煤种,变换气中有无脱硫(湿法或湿法加干法)工段。
(2)原料气中有机硫主要为COS,CS2含量在极大部份厂中可以忽略,COS含量为(2~15)×10—6,主要取定于原料煤种。总硫比食品CO2国际标准的指标(<0.1×10—6)高50~5000倍。
(3)原料气中苯含量为(2000~10000)×10—9,比国际标准<20×10—9超过100~500倍,总烃为(800~3000)×10—6,比国际标准<20×10—6超过40~150倍。
(4)表中E厂与F厂已设有JTL-1常温精脱硫新工艺,精制气中总硫含量仍超标,经调查系CO2负荷显著超标或精脱硫工段操作不当所引起。
综上所述,以中小氮肥厂的CO2原料气生产食品CO2时,精脱硫与脱苯脱烃的任务都相当艰巨,本文简要叙述我中心开发的常温脱硫新技术与THC-1脱烃催化剂在食品CO2中的工业应用。
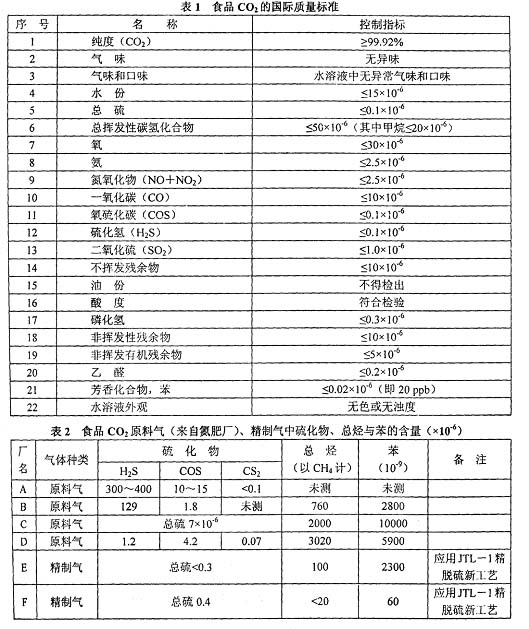
1 常温精脱硫新技术在食品CO2中的应用
国际标准要求食品CO2的总硫小于0.1×10—6,否则生产的饮料发生臭味、混浊。曾经出现大批贮存的饮料变质的严重质量事故。应用于工业焊接时,如硫含量超标易发生起泡现象,降低材料的机械强度。在CO2气体中脱除微量硫化物(如H2S、COS为几个到几百×10—6)时,CO2浓度高达~97%,即97万×10—6,由于竞争吸附与平衡制约(水解反应为COS+H2S=H2S+CO2)的原因,大大制约了水解催化剂的COS转化率与精脱硫剂的脱除H2S效果,故精脱硫一直是食品CO2生产中的一大难题。
自1991年以来,我中心先后开发了多种常温精脱硫剂和JTL-1常温精脱硫新工艺,并在甲醇、合成氨工业中应用,取得了显著的效果。在此基础上,针对CO2气体中上述精脱硫问题,进行了大量的研究工作,并结合工业应用取得的数据进行反复分析,较好地解决了这一难题,并很快在国内30余家企业应用,均取得了满意的效果。下面介绍食品CO2中的精脱硫工艺、原理及应用情况。
1.1 食品CO2精脱硫新工艺的介绍
CO2原料气一般是由氮肥厂脱碳系统解吸而来,温度较低(10~50℃),原料气中硫化物为H2S与COS,因而传统的高温精脱硫工艺不适用。CO2气体中传统的干法脱硫方法是采用普通活性炭、氧化铁或其它混合型脱硫剂,它们的脱硫精度差(<1×10—6)、硫容低,不能达到精脱硫指标。早先也有采用优质的活性碳对H2S、COS进行吸附解吸再生方法,可以达到精脱硫指标,但存在穿透吸附硫容低、再生频繁、需要热源、操作复杂、污染环境等缺点,因而逐渐被常温精脱硫新技术代替,最多采用的是JTL-1常温精脱硫新工艺。
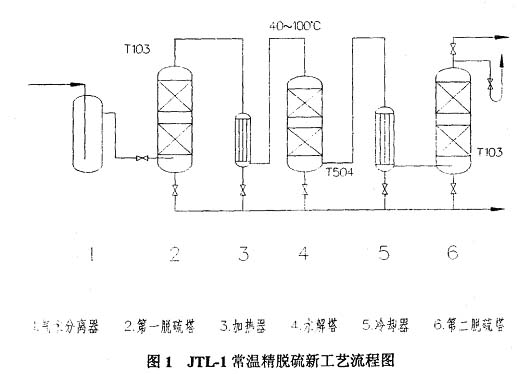
CO2原料气经气水分离器后首先进入第一脱硫塔(装填T103型活性炭精脱硫剂),将H2S脱至<0.03×10—6,然后经加热器提温至40~100℃,进入水解塔(装填T504型水解催化剂)。将COS通过水解反应(COS+H2O2==H2S+CO2)转化成H2S,出口COS<0.03×10—6,工艺气经降温后进入第二脱硫塔(装填T103型活性炭精脱硫剂),将水解转化的H2S脱至<0.03×10—6,从而保证精脱硫系统出口总硫(H2S+COS)<0.06×10—6。
该工艺具有如下的特点:
(1)调整T504水解催化剂配方,开发了能抗高浓度CO2的干扰、专用于食品CO2的T504水解催化剂,使其既能达到高的COS转化率(出口气中COS<0.03×10—6),又延长寿命,目前可达2年以上。
(2)开发了食品CO2专用的T103型精脱硫剂,它在CO2气体中的原粒度精脱硫容可达10%~20%(出口H2S<0.03×l0—6),使用时间也可达1~2年。
该工艺开车时间短、能耗低、无需再生、操作简单、环境不造成任何污染,可保证CO2生产长周期稳定运行。
1.2 JTLI—l常温精脱硫新工艺的正业应用
(1)上海泾福气体有限公司是专门生产高纯度的食品级CO2、干冰及下游产品的公司。该公司曾用铁屑加木屑的传统脱硫剂进行粗脱,再以吸附剂进行精脱,但其价格较贵,且再生频繁,污染环境效果一直不理想。故该公司决定在新系统中采用JTL一1常温精脱硫新工艺(T504型水解催化剂串T103精脱硫剂),并已开1995年1月开车成功。该公司食品级CO2生产工艺如下:

主要指标及参数为:进水解塔气量1500m3/h,压力2.0MPa,进除臭塔CO2气体中COS(15~30)×10—6,要求CO2产品气中H2S<0.10×10—6,COS<0.10×10—6。生产测定数据见表3。
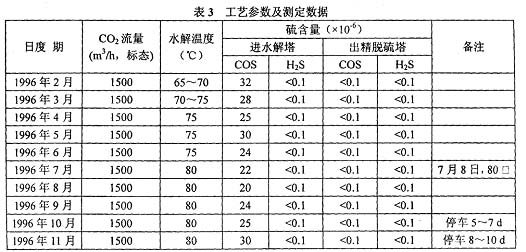
该公司食品CO2新系统开车以来,精脱硫系统运行稳定。系统出口达到精脱硫指标, 即H2S<0.1×l0—6、COS<0.1×10—6、总硫<0.1×10—6。T504水解剂的寿命已达2年以上,高于原设计值(6个月),取得了满意的使用效果。美国可口可乐及百事可乐国际集团公司多次对产品定时或随机抽样,结果表明产品合格,质量稳定,并颁发了认可证书。精脱硫系统的使用也取得了显著的经济效益,以前该公司曾向美国公司询价需30万美元:采用JTL-1新工艺,催化剂与设备的费用30万元人民币,使得投资大大下降。由于该系统正常运行,保证了生产稳定,从而达到增产的目的,扣除催化剂费用及其它费用,年效益为26万元以上。
(2)中国BOC公司下属多个公司生产食品CO2,西安BOC公司在建厂初期采用的原装进口精脱硫剂是特种氧化铁与粉状活性炭的混合物,经过一段时间的实际运行,产品送往原化学工业部气体质量监督检验中心监测,发现氧硫化碳超标,结果为1.1×10—6,总硫高达1.4×10—6,严重制约生产的正常运行。同年7月,经和BOC中国技术顾问商讨,决定采用国内某研究所的技术工艺:氧化铁+水解剂+氧化锌,运行2个月后,发现产品有异味,影响饮料食品级客房的供应。之后,该公司又增加了除味设备,虽然解决了异味问题,但由于氧化铁的硫容太低,使用过程中,需要重新更换,而生产工艺中只有一个脱硫塔,故更换起来非常棘手。1998年底该公司通过多方调研,了解到湖北省化学研究院的T103+T504+T103夹心饼新工艺,1999年3月,采用此专利技术,经过2年多运行,效果令人满意。
(1)自T103+T504+T103精脱硫工艺1999年3月投入使用以来,产品多次经原化学工业部气体质量监督检验中心、美国ATLPUNTICNALYTICAL—LABORATORY及PRAXAIR(THAILAND)C.,Ltd.监测:总硫均小于0.1×10—6,硫化氢和氧硫化碳也均小于0.1×10—6,完全满足国际饮料技术协会对食品二氧化碳中各种硫化物的要求,既保障该公司生产的稳定运行,又满足用户的需求。
(2)由于精脱硫使用了特种活性炭,故对异味的脱除效果特别好。1999年4月,停止双塔吸附器的使用,通过对各种杂质组分的测定,完全符合标准,既降低生产成本,又减少操作工的负荷。
大连BOC先前曾采用普通氧化铁脱硫剂,由于硫容太低,使用不到1个月即被迫更换。青岛BOC原先采用国内某研究院的水解串常温氧化锌工艺,使用不久后总硫明显超过0.1×10—6,经我中心派人带便携式微量硫分析仪到现场测定后发现H2S与COS均已超标。这2家中国的BOC公司均采用T504水解串T103特种活性炭的精脱硫新工艺,使用至今,效果满意。
上述3个中国的BOC公司的精脱硫应用历史表明:我中心开发抗高浓度CO2竞争吸附干扰的、食品CO2专用T504水解催化剂与T103 H2S精脱硫剂是成功的。
(3)BOC公司美国技术中心与我中心多次技术交流,经过近2年时间对食品CO2专用的T504水解催化剂与T103精脱硫剂的实验室对比测定后,已于今年在美国1家以发酵气为原料的食品CO2厂进行T504串T103精脱硫剂的工业应用试验。澳大利亚1家以发酵气为原料的食品CO2也进行T103精脱硫剂的工业试用,初步结果显示T103不仅可以精脱H2S,也对发酵气COS高浓度(平时很低)短时间的冲击有很好的脱除效果。
1.3 EAC—4 H2S、SO2双功能精脱硫剂的应用
在以石灰窑气生产食品CO2时,原料气中除含有H2S、COS外,还含有一定量的SO2,此时除了应用T504水解剂、T103精脱硫剂外,还需要加用EAC—4双功能精脱硫剂,以使食品CO2产品中的总硫与SO2均达到标准。
2 THC—1脱烃催化剂的开发及其在食品CO2中的应用
2.1 苯吸附剂应用的可能性
作者曾见到一份活性炭苯专用吸附剂的资料中简介:比表面~700 m2/g(为普通活性炭),苯饱和吸附量100 mL/g活性炭(以下的表示中,省略活性炭)即0.35 g苯/g。在实际工况下苯含量低,其分压也低,饱和苯吸附量为~40 mL/g,即0.14g苯/g,因此对苯的脱除是一次性的,脱苯的精度可<0.01×10-6。
我们认为,与普通活性炭脱硫剂十分相似,普通活性炭脱苯吸附剂在一般的活性炭厂皆有(多用于环保或分离中),均对高含量苯的脱除,脱除率可>99%,但净化后精度差,远达不到<0.01×10-6。有关苯吸附剂在食品CO2中使用时,应注意下面一些问题:
(1)活性炭的苯吸附是物理吸附,物理吸附是范德华力即分子间的引力作用的,与脱硫或水解化学反应有很大区别。
(2)按物理吸附原则,苯的饱和吸附量与苯在气体中的分压成正比,苯的饱和吸附容量一般是在常压、常温饱和苯蒸气下测定的。以30℃为例,此时苯的饱和蒸气压为119 mmHg,其分压为0.157kg/cm2,—上述苯专用吸附剂的饱和吸附量为0.35g苯/g。在食品CO2生产中,原料气压力为30kg/cm2,苯含量为2×10-6,苯分压=30×2×10-6kg/cm2,计算得此工况下的苯饱和吸附量大大降低,仅为0.134μg苯/g,与上述资料中称苯吸附量为0.14g苯/g相差甚远。
(3)实际应用时需要的是穿透苯容,而不是苯饱和吸附量,穿透苯容比苯饱和吸附量低的多,低多少,没有数据。假定苯吸附剂在食品CO2生产工况下的苯饱和吸附量仍以上述的0.134μg苯/g计算,实际应用时也仅2h即穿透。
(4)痕量苯(即ppb级)分析的准确性有相当难度,苯标气属于国家标准物质,现在国内尚未验收,又无国家标准的食品CO2中痕量苯的分析方法,因此市场上提供的苯吸附剂可在食品CO2生产中一次性使用,并将苯脱至<0.01×10-6,可信度相当低。
2.2 THC—1脱烃催化剂的研究与开发
经过10多年的努力,我中心开发了多种贵金属催化剂,已工业应用的有TH系列脱氢、TO—2脱氧、THC—1脱烃催化剂,它们均是借氧化铝载体上负载钯(或铂)、特种助剂与添加剂后加工而成。虽然贵金属催化剂的价格较高,但由于它们有十分优异的催化活性,在很多领域中仍是非贵金属催化剂所不能取代。TH—2、TH—3尿素脱氢催化剂自1999年在镇海化肥厂应用以来,在以天然气、重油与煤为原料的大、中、小氮肥厂在推广,市场占有率达70%。TO—2脱氧催化剂在某无线电器厂空分氮气中应用。THC—1脱烃催化剂于2002年在江苏、湖北聚脂切片领域中应用成功后,结合食品CO2工况又进行了开发研究,其典型的实验数据见表4~6,结果表明:
(1)CH4与C6H6分别为单独气源时(表5~6),在300~400℃时THC—1催化剂均可将C6H6的转化率>99.98%,对CH4则要困难得多,需要到~425℃时,才能使其转化率>99%。
(2)CH4与C6H6为混合气源时(表4),在350~450℃时,THC—1催化剂对C6H6的转化率均>99.98%,对CH4的转化率则低得多,仅为20%~95%,进一步证明CH4比C6H6要难脱除,因而在它们共存时,THC—1催化剂对C6H6脱除的选择性比CH4要好。
(3)如果CO2原料气中的CH4含量2000×10-6、苯含量5×10-6,则THC—1催化剂的初步操作温度为~450℃。
2.3 THC—1脱烃催化剂在食品CO2中的工业应用。
经与杭州快凯有限公司合作,于2003年底THC—1脱烃催化剂在国内某厂首次投入工业应用,进行升温活化后,取脱烃塔出口的气样送近邻的该省纺织化纤集团质检中心,测定结果(见表7)表明:
(1)食品CO2原料气中总烃含量仅为85×10-6,比表2中的数据低得多,因此在380~460℃很宽的温度范围内,THC—1催化剂可将总烃脱至<3×10-6。
(2)食品CO2原料气中苯含量为(4~5)×10—6,与表2中的数据相吻。经THC—1催化剂后的出口气中,苯含量在380~460℃间均为未检出,该中心未有苯标气,故最低检出量尚有待进一步确认。由于测定的温度范围达80℃,从实验室数据可以推论,在某一温度(如400或425℃)以上时,脱烃塔出口气的苯含量可以<0.02×10—6。正在积极努力,尽快取得准确的结果。
(3)THC—1催化剂在380℃下可几乎全部脱除H2与CO,这对降低提纯塔负荷,减少放空量,提高产量均很有好处。
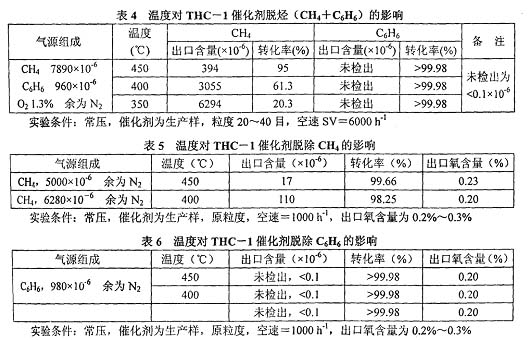
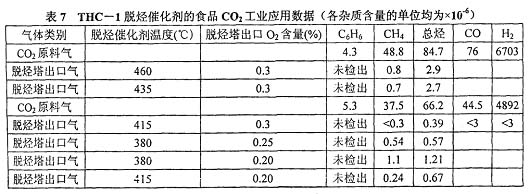
鉴于THC—1脱烃催化剂在食品CO2厂中得到初步的成功应用,目前已有几家食品CO2厂即将投入应用,到时将会有更多的工业应用结果报导。
3 小结
(1)食品CO2的国际质量标准十分苛刻,其中总硫<0.1×10-6、总烃<50×10-6与苯<20×10-9 3项指标是关键。鉴于大多数氮肥厂均有富余的CO2气体,食品CO2又是一新兴发展的、且已与国际质量标准接轨的行业,因此,为实现这3项关键指标必然要增加投资,但同时可产生显著的经济效益,给一些氮肥厂带来了一次宝贵的发展机遇。
(2)由抗高CO2竞争吸附干扰、专用于食品CO2的T504水解催化剂与T103 H2S精脱硫剂组成的常温精脱硫新工艺,应用于食品CO2领域已有10年历史,可脱除总硫<0.1×10-6,运行稳定,寿命长,产品质量得到可口可乐公司与百事可乐公司认可。该精脱硫新工艺也已开始在美国、澳大利亚食品CO2工业中应用。
(3)THC—1贵金属脱烃催化剂的实验室数据表明:在食品CO2的典型工况下,为使CH4与C6H6的净化度达到指标,THC—1催化剂的操作温度分别为425~450℃与400~425℃,CH4比C6H6更难脱除。THC—1催化剂于2003年实现食品CO2领域中的首次使用,得到了初步满意的效果。
