[摘 要]通过与当前国际合成塔技术进行比较,介绍了ⅢJD系统及内件技术的设计思想,内件的结构特性及优点,ⅢJD技术的推广应用情况等。
[关键词]氨合成;内件;技术
0 前言
氨是最为重要的基础化工产品之一,其产量居各种化工产品的首位。合成氨同时也是能源消耗的大户,世界上大约有10%的能源用于生产合成氨。我国为合成氨生产大国,拥有超过500家的大、中、小型合成氨企业。但就单套系统的产量而言,均无法和国外的单套系统、单产量相比,近年来,国内的合成氨企业能力不断扩大,大家都向着“大型化、低能耗、清洁生产、长周期运行”方向发展,由此整合着我国合成氨生产资源的分配,也分配着能源。
湖南安淳高新技术有限公司从事合成氨工业技术的开发和节能型氨合成系统技术研究20多年,在全国合成氨行业率先开发了31.4MPa压力级的DN1200、DN1400、DN1600、DN1800、DN2000、DN2200系统。目前正在进行更大型化低压合成技术的开发和多级合成系统的工程实施。正在推进着单套合成氨装置大型化和高产化的国产化进程,将我国的合成氨技术和世界合成氨先进技术“接轨”,开发了与我国合成氨造气方法和造气水平相配套、有中国特色的合成氨技术。特别是氨合成系统及合成反应器内件的设计,从系统流程的设置、各工艺设备的设计等方面“独辟溪径”,创造了多项专利及专有技术。
目前,安淳公司配套和设计的合成系统,单套合成氨能力达1000 t/d,近期将投产运行。笔者作为技术参与者,下面对我公司利用独有的专利技术开发的氨合成系统及氨塔反应器内件进行介绍。
1 国外合成氨技术的现状和进展
1.1 70年代至90年代的氨合成技术回顾
国外著名的合成氨技术及产品供应商有英国ICl、德国Uhde、德国Braun公司、德国Linde公司、丹麦Topsφe、美国Kellogg等公司。在合成氨系统全套工艺技术开发和氨合成塔及合成塔高压回路上,相继开发出各具特色的工艺技术。具有大型化、系列化、能源综合利用科学化等诸多优点。其中有很多不乏为经典之作。
我国合成氨工业进入大型化是从上世纪70年代开始的,当时国家在经济十分困难的条件下引进了13套合成氨装置,引进的装置涵盖上述各个公司的技术,可以称之为集当时国际上合成氨新技术之大全。
当时,氨合成反应器最具有代表性的为Kellogg公司的“K”型氨合成塔,该塔为四床或三床全冷激式塔;再有Braun公司的二塔或三塔氨合成系统,Braun流程中三个合成塔均为绝热层塔,第一合成塔出口配置工艺气加热器,第二和第三合成塔出口安装有废热锅炉,回收合成塔出口反应气热量,产生高压蒸汽(13.03MPa、温度331℃);还有Uhde公司的三床全径向型(第三径向床出口无换热器)氨合成塔,Lurgi公司的二床全径向型合成塔等塔型。当时国际国内的大型合成氨装置大部分为立式塔型。我国引进合成氨装置中以Kellogg公司的冷激式氨合成塔较多,这种大型的塔(180 kt/a,15MPa合成回路压力,DN3200的塔型)以塔直径大、催化剂装填量多、运行的“空速”小等方式来实现高产量。
著名的Braun流程和合成塔则采用三个立式的绝热型催化剂筐,每个塔外设换热器或蒸汽过热器对反应气降温和回收反应热,这也是用较多的催化剂来实现较高的氨净值,进而减少循环量和提高热回收率的方法,也为简化合成塔反应器结构、提高热回收率、提高氨净值等创造了一种经典的流程及设计思路。
1.2 90年代以来氨合成技术的发展及思维走向
进入90年代以来,随着能源的紧张,也随着新技术新材料的不断出现,各个著名合成氨公司又从新材料、及新型催化剂入手,创造了更加完美的新型流程和氨合成反应器。具有代表性的低能耗制氨工艺有4种:Kellogg公司的KREP工艺、Braun公司的低能耗深冷净化工艺、UHDE-ICI-AMV工艺、Topsφe工艺和S-200、S-50型氨合成塔及S-250型的串塔工艺;也有Uhde公司大能力的三塔双级压力氨合成圈流程及三床均为径向流的合成塔,这种流程及配合的双级压力回路最高日产达到了3300t;另外还有KBR流程和卧式横向流氨合成塔;还有一直坚持采用轴径向流合成塔工艺的Casale合成塔及流程。
这些公司对合成塔及合成回路流程的改进,都是在大型化、降低回路及氨合成塔塔阻力降、径向流的设置等方面开展工作。辅以采用新型催化剂,使合成回路的运行效率更高、热回收量更多、回收的蒸汽品位更高。同时单系统的产量也遂步上升,目前最大氨合成回路的单套生产能力达3300t/d以上。
总结来看,主要从下述几方面着手进行技术革新。
① 从全系统(从造气岗位开始至合成氨工序)着手,开发系统总能耗低的制氨工艺技术。主要以节能降耗为目的,立足于改进和发展工艺单元技术。
② 注重净化技术,创造进入合成高压圈气体净化度高、惰气含量少的反应气气源。诸如采用低温甲醇洗串深冷净化工艺、分子筛净化工艺等技术。
③ 注重降低回路阻力,也更注重采用小颗粒催化剂和广泛采用径向流技术,提高氨净值、减少循环量和提高热回收率。
④ 随着机械制造技术和材料技术水平的提高,在氨合成回路的压力级选择上,也不一味地降低氨合成回路的工作压力。各公司结合合成氨总体流程,开发了有11MPa压力级的氨合成工序,也有14.8MPa、19.5MPa、21MPa等压力级的合成工序。如Uhde公司采用了两个不同压力级进行组合的回路技术,最高级的回路工作压力达到了21MPa。
⑤ 采用多塔串联的方式来提高回路产量。由于受运输及制造水平等限制,合成塔大到一定尺寸后,制造成本和运输价格将显著上升。为了提高回路产量,使装置特大型化,运用了多种串塔的流程。这些有传统的Braun三塔或双塔串联流程,也有Topsφe公司的S-250型流程,这种流程是在S-200合成塔反应器后串上一个S-50的合成塔,每反应器配上相应的热回收系统,组成串联塔回路,更加精妙的设计组合有德国Uhde公司的双压力级、三塔串联流程及合成塔技术。上述流程及塔型均可达到回路产量在2000t/d以上,最高已经达到3300t/d的水平。
⑥采用钌基催化剂提高合成效率。这是为提高系统产量进行的革命性工作,使合成塔的氨净值提高,采用各种新型催化剂,特别是钌基型催化剂,氨净值比传统的催化剂提高5%以上。
⑦ 利用燃气透平和蒸汽透平作为动力的离心式压缩机和离心式循环机,有效地整合和利用工艺及原料系统的动力,进而降低整个合成氨系统的综合能耗。
⑧ 提高装置生产运转率、延长运行周期。包括工艺优化技术、先进的控制技术和控制手段等技术的使用。
⑨ 大型化、集成化、自动化,使系统具有经济规模,成为低能耗与环境更友好的合成氨装置。
通过采用上述改造思路,前期引进的合成氨装置,在原料路线和动力路线上也进行了新技术改造工作,特别是在合成氨回路及氨合成塔的改造方面下了大的力气,基本上将原来的Kellogg全轴向冷激型氨合成塔改造成径向流和段间换热型,有效地降低了回路阻力,提高了产量,节约了能耗。
2 我国合成氨工业的现状及特定工艺条件
我国引进的大型合成氨厂总的生产能力仅占合全国合成氨总能力的1/4左右,其余产量靠几百家中小合成氨厂来生产,由于受原料和工艺路线的限制,能耗相对较高。
我国中小合成氨厂绝大部分以煤焦为原料。造气工艺几乎全部为UGI炉型的造气工艺,系统后续工艺的配套大部分为铜洗净化精制、31.4MPa压力级的氨合成回路,这样就构成了我国合成氨工业大部分厂家的特定工艺条件。由于我国资源的限制,我们长期面对的现实是以煤为原料的合成氨厂技术改造如何做,达到什么技术水平和能耗水平。
当然,如果均用水煤浆制气或粉煤制气,净化和压缩等工序将进行配套改造,这要投入大量的资金,显然,在近期是不可能大面积实现的。
由于大部分厂家采用31.4MPa压力级的合成工艺,受压缩机的限制,装置增产也必须沿着原来的特定工艺条件进行。这样,氨合成工段的改造在一个相当长的时间内,也必须在这种特有的工艺环境下进行。
3 ⅢJD系列氨合成系统设计思想
ⅢJD系列大直径、高产量型氨合成技术是湖南安淳高新技术有限公司在总结ⅢJ系列系统及氨合成塔内件在全国合成氨行业400多台套运行经验的基础上,汲取90年代以来国际先进技术以及国内引进的大型氨厂合成塔运行经验,开发设计的新技术。
本技术主要立足于我国现行的合成氨工业条件,依据我国的合成氨相关设备、相关材料及相关催化剂条件开发的。随着合成氨工业的发展,本技术也在“与时俱进”,目前已经发展到日产合成氨能力超过1000t,采用较高的合成塔出口温度,使回收的蒸汽压力更高、生产能力更大,系统运行压力低压化,也进行多塔串联等。其内容和形式上有别于国外的同类型工艺,这些技术完全是有自主知识产权、立足于国内现成工艺的技术。在行业中运用取得了较好的效果。
氨合成反应是一个在有催化剂存在、高温、高压可逆的放热反应,理论上生成1mol氨,合成反应放热量在450℃时可达到54.4 kmol;由于受催化剂反应活性及平衡等因素影响,生产过程中采用了气体循环生产的方法,为提高系统回收氨的水平,运用了冷冻降温和低温分氨的方式。因而,合成氨系统可以视为一个集反应、换热、冷冻、分离、系统动力循环多单元的系统。
最理想化的状态是要求尽量多回收反应热,少用冷冻量、多回收冷量及热量,尽量减少循环量。要达到这些优化条件,设置好系统流程及设计好系统工艺条件最为关键。3.1 ⅢJD氨合成系统的基本流程(图1)
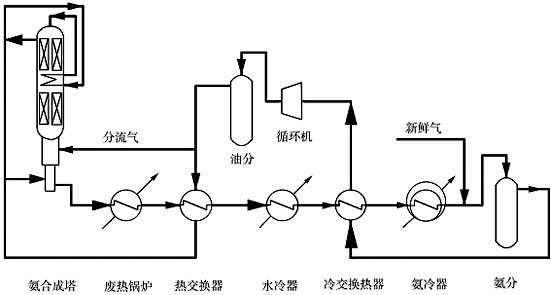
图1 ⅢJD氨合成系统流程
流程叙述:从循环机来经过氨分离后的合成循环气再经过循环机出口油分离器分离油滴后,气体分成两路:一路直接进入合成塔的环隙,对合成塔的外壳进行冷却,以保护合成塔外壳,免超温导致高压条件下材料的“氢蚀”,保证合成塔的运行安全;另一路进入合成塔外的热交换器,和合成塔反应后经过废锅的气体换热,加热合成塔入塔气。加热后的气体经合成塔下部换热器后进入合成塔上层“零米”层,与段间换热器来的气体温合进入催化剂床进行反应,经一段、二段反应后进入第三段,这一段为一个间接换热型的径向反应段,经过此段反应后再进入绝热的第四段反应,经下部换热器出塔。另一股调温用气是和经过合成塔环隙的冷气汇合,这股气体首先从合成塔上部出来,再与热交换器出来的热气进行混合,组成的混合气再进入合成塔的段间换热器,调节合成塔第三段的温度,然后进入合成塔“零米”层。这股气与经过合成塔内下部换热器换热出来的气体一道进入催化剂床反应;出合成塔后的气体,依次进入设置在塔外的废热锅炉、热交换器管内,与未反应循环气换热,再进入水冷却器管内进行冷却。冷却后气体进入冷交换器管间,与氨冷来的冷循环气冷热交换后,气体得到了比水冷更进一步的冷却,冷却后的气体再在冷交的下部分离段进行分离,分离掉70%以上的液氨。分离后的气体出冷交换器后进入氨冷却器管间(如为二级氨冷器,则串联逐级进行冷却),氨冷后的气体和压缩来的新鲜气混合(如果用分子筛进行新鲜气处理,补气可以直接进入氨合成塔)再进入氨分离器再次分离液氨;氨分后气体再进入冷交换器管内,与反应后的循环气换热后进入循环机系统补压循环,这样就完成了一个气体循环过程。循环气中积累的CH4、Ar等惰性气体在水冷的一次出口处弛放,以保证循环气中惰气含量在控制指标内。
按上述流程进行分析,我们将合成系统按功能分为四个单元。第一个单元为反应器单元,这里利用ⅢJD高效氨合成反应器来实现氨合成,本身进行系统内部反应热平衡,达到高的氨净值、低的循环量运行之目的,反应效率是否能提高、催化剂利用率是否高均与本反应器内件的设计水平有关。第二个单元为热回收单元,本单元的主要目的是将合成反应热尽可能地在废热锅炉和热交换器得到回收,达到多生产高品位蒸汽的同时,将相对低位能的热量加以回收,以保证合成塔自身的热平衡,并使反应后循环气进入水冷却器的温度最低。第三个单元为冷回收单元,本单元两个功能,第一个功能是将合成氨的循环气进行冷冻,达到相应条件下循环气的液氨分离量最大,也就是说达到进入氨合成塔的入口氨含量尽量低,另一功能是将液氨气化而产生的冷量进行回收,保证冷量在冷交部分回收得尽量多,以减少氨冷器加入冷冻剂(液氨)的量,确保出冷交换器的冷气温度尽量高一点,这样冷量就得到极大的回收,减少了加入液氨的量,节约了冰机电耗。第四单元是分离单元,这个单元主要是油、水的分离和液氨的分离。如果分离效果好,将减少无用功的消耗,达到节能之目的。
3.2 反应单元——氨合成塔反应器
好的合成塔内件,必须具备有能方便地实现设计要求的产量、运行中调节掌控温度方便、催化剂利用率高、操作弹性好、催化剂易还原、催化剂易装卸、结构可靠且简单、合成塔的阻力也应尽量小。这些因素组合在一起,有的是相对立的,怎样辩证地思考问题,这是合成塔设计者要面对的问题。
怎样才能兼顾各方面,尽量优化反应器,设计出一个在一定条件下运行最稳定、能量最节约的合成塔反应器,我们经过了近20年的不懈努力,开发了获得国家科技进步二等奖的系列合成塔技术及产品,上世纪80年代中期开始,从小型塔入手,DN600、DN800、DN1000、DN1200、DN1400、DN1600、DN1800、DN2000、DN2200系列技术逐步发展,到目前形成了具备全系列、多规格、各种不同要求及不同系统条件相配套的系列合成塔技术及产品。
这种大型合成塔技术及反应器,我们称之为ⅢJD系列氨合成塔技术。这些技术在合成塔内件反应器设计上具备有下述特征及技术特点。
(1)采用分流工艺调节催化剂床层温度
众所周知,氨合成塔的设计是采用了适用催化剂特性的设计方法来进行工艺及结构设计的,而催化剂反应达到一定的温度后就必须将反应热移出,使气体再一次以低的温度进入床层反应,达到第二次反应的条件,这将进行反复升降温操作,使反应沿着催化剂最适宜温度曲线行走,才能达到尽可能高的合成塔出口氨含量,得到尽可能高的氨净值。
经典的合成塔工艺调温方式有下述三种方式,见图2。
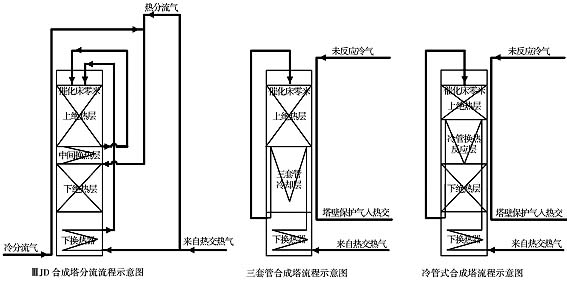
图2 合成塔的调温方式
大部分间接换热式合成塔和冷管型合成塔,采用的是未反应气体一次性进入。气体在反应前先通过管道进入需要降温的催化剂床层,用温度相对较低的未反应气来冷却催化剂床层的高温段。这些合成塔有诸如传统的三套管式、段间冷却型等塔型。这种调温方式的优点是调节温度十分简单,只在合成塔进气的主阀加上一个调节“零米”温度用的副阀就可以了。在具体生产中,只要调节系统的循环量就可以方便地调节合成塔温度了。其缺点是换热管要密布在催化剂床层,进入的气体要反复加热,热气的流程长、通道窄、造成阻力大。另一方面,冷却管内与管外的催化剂反应温度差将越来越小,换热推动力也越来越小,造成要布置较多的管或较大的循环量来降温的态势,这就直接导致了催化剂床层阻力大、催化剂装填量小,系统循环量大,氨净值提不高。采用段间降温的方式,也有同类的问题,同时催化剂床层设计也十分复杂。
ⅢJ系列氨合成塔则沿用了间接降温的方式,并将内部换热器进行优化改良设计。采用冷气体从外部引入,直接进入不同的床层,按要求控制进入气量的大小、调节进入气体的温度,以此来调节催化剂各床层温度,达到了既采用间接换热式调温,又运用了“冷激式”塔的“分流”、分区分层调节的优点。
由于外来的“分流气”进入合成塔床层时的温度较低,传热温差将变得较大,这样,内置的段间换热器及有关调温元件就可设计得较小,占据的合成塔催化剂空间也较小。达到了提高催化剂装填量、降低阻力的要求;另外,由于气体进行分流,也使得各催化剂床层的调节可以达到“随心所欲”——按不同催化剂反应活性和不同的温度及产量分配流量,从而十分方便地调节催化剂各床层温度。
这种“分流”带来了下列好处:一是极大地降低了系统的循环量;二是可以使调节十分方便;三是可以使催化剂升温还原时,完全断掉层间换热器的气流,创造一个绝热升温还原的条件,使催化剂还原能够十分彻底;四是由于“分流”,一部分气体不经过下部换热器,下部换热器的管间流量相对较小,进入中心管的气量也较小,可减少下换热器的面积,也减少了气体流动的阻力。
这种塔内部的分流,还只是一种分流方式。为了更加优化系统,我们也开发了“全分流”的流程——冷气进入合成塔前进行分流,热气也在进塔前分流。成功地将进入合成塔环隙的气体流量下降到仅占主气流量的10%,这样既保证了合成塔塔壁温度不超标,也使得合成塔环隙流的阻力大大下降。这也是ⅢJD合成塔技术一个十分显著的特点。
(2)尽量不用和少用冷激方式来调节床层温度
气固反应床的氨合成塔反应器,一般都采用内置式催化剂床层的降温方式。不管目前的内件设计如何千变万化,但就其降温的方法和降温的原理来分有下列三种降温方式:冷管式降温、冷激式降温和段间换热器型的间接降温方式。见图3。
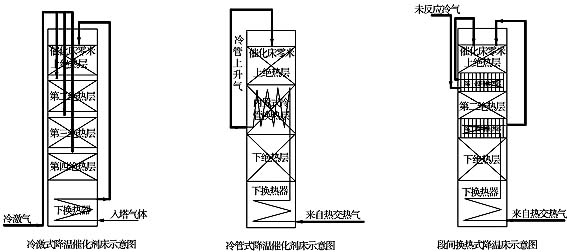
图3 氨合成塔的降温方式
三种降温方式各有优缺点,唯有冷激式降温方式最为简单, 但这种方式由于采用未反应的气体通过外分配方式进入不同的催化剂床层,直接将反应后升高了气体温度降下来的方式调温,这样也冲稀了反应气的氨浓度,当床层设计的催化剂段数比较多时,越进入下部,这一部分未反应气走过的催化剂床层就越短,和催化剂接触的时间就越少,总体来说,就会对反应氨净值的提高有影响。同一产量下,冷激式比间接换热式的合成塔将要增加循环量,也要减少热回收量。上世纪70年代,我国引进的300 kt/a合成氨装置,较多地采用Kellogg公司的瓶式多层冷激式合成塔,随着技术的深入,迄至今日,几乎全部改成了段间换热型的改良“K型”塔。这样,既提高了氨净值,又提高了合成塔的产量。目前国外的Uhde公司、Topsφe公司、KBR公司、Casale公司均很少用冷激式降温的方式来调节床层温度,这也是随着节能工作深入,工艺之必然选择!
ⅢJD型合成塔内件的降温采用分体式,在催化床层中含有一到两件段间换热器组件,组成了一个四段或五段轴径向型的合成塔。它几乎没有用冷激来降温,这样,可以达到十分好的调温效果,同时,得到尽量高的出口氨含量,尽量小的系统循环量。
(3)采用多气室径向床技术
采用径向床,是当前合成塔为了降低阻力降常用的方法。国外的各种塔型气体内部流动方式不是采用径向流就是采用横向流,全部采用轴向流的塔型十分少见了。随着合成塔进入大型化,各合成塔设计公司均注重研究径向筐的分布等问题,做了大量的工作。我公司经过大量的研究和工程实践,开发了一种多气室、反复混合型的径向筐分布器,这种分布器可以将径向流的气体在进入气室前经分气端及收气端的初步分气后,再在收气端进入多气室反复混流型径向分布器中,将气体进行多次折流、多次混合,各方向来的工艺气体混合完全,分布均匀。
采用这种径向筐技术后,合成塔反应器内约占70%以上的催化剂层气体流动为径向流,反应床层阻力降不超过0.4MPa,达到了国内外同类合成塔的先进水平。也达到了分气均匀,运行平稳的目的。
(4)运用可径向流的段间换热器技术
传统的三套管和冷管式的合成塔最大阻力段均在冷管层,因冷管占据了催化剂有效截面,且高温反应后的气体在冷管内进行了节流,因而这部分的阻力大,这是冷管式合成塔无法解决的问题。一般来说,当合成塔的高径比为1/10,合成塔负荷达设计负荷时,一个三套管合成塔催化剂床层的阻力降可达到1.8MPa,一个冷管式纯轴向的合成塔阻力降最少也有1.2MPa,这样就限制了合成塔大型化生产技术的发展,因而,冷管式合成塔基本没有大型的塔存在。
ⅢJD型氨合成塔运用了一个类似于冷管结构的新型段间换热器(已获得了国家专利),它也是段间换热器和冷管变形的换热器,将它埋在催化剂床层,催化剂床的反应气体是沿径向流动的,换热器内作为冷却的气体也是沿径向流动,与外部气体并流进行换热。这就彻底解决了冷管式或换热器式层间冷却器无法实现径向流的问题。它和典型的段间换热比,有管外能填充催化剂,提高反应效率的优势,当然也提高了催化剂的装填量。和传统的冷管式换热器相比,它有径向流的优势。
通过这种技术的运用,我们开发的合成塔塔径由DN1200上升到DN2200以上,合成塔的总阻力降均在0.4MPa以下。
(5)采用细长型分列式内部换热器
合成塔的下部换热器一般来说面积较小,大直径的塔设成一个鼓形换热器将会使管内的气体流程太短,换热效果不好,管外采用折流板时,将会使换热时气体流动“死区”太多,也极大地影响了换热效率。ⅢJD采用了细长形的换热器,它和中心管设计成一个整体,这样既便于维修,也便于提高换热器的换热效率,还有利于合成塔下部径向段的设计(将径向分气与收气、换热器结合成一个整体)。细长形的换热器也更进一步简化了内件结构,使内件的维修变得更加方便。
(6)采用多层复合保温技术
多层复合式保温技术是湖南安淳高新技术有限公司的一个专利技术,它借用了航空技术及般天材料,将内件的保温层做得更加精致,保温效果更好。这种技术在我公司开发DN600合成塔就使用了,之后不断完善,到目前为止,从未出现过内件保温层脱落而影响生产的情况。而这在以前,保温层脱落是合成塔常出现的故障之一。
对保温层的设计,我们还对合成塔内的反应机理进行了研究,考虑了对流、幅射等的影响,运用了多种高科技的手段进行保温效果模拟和保温优化设计,采用了多节式多伸缩结构的保温皮来保证内件的热胀条件好。
(7)采用连续催化剂床、催化剂自卸技术
采用了连续的催化剂床层,这也是保证自卸催化剂顺畅的一个必要方式。内件设计二到三个径向段,每段之间的分层均采用活动和中间有催化剂流动孔的设计部件,完全能保证催化剂从上而下顺利进入内件中,也保证了径向筐上部催化剂能“封住”进气通道,保证径向层进气和出气均不短路。这种设计,使内件装配和检修变得更加容易。
优化设计的ⅢJD氨合成塔反应器由一个独立、下部带换热器的中心管及换热器组件加上一个能实现径向流的段间换热器组成的活动换热件,和一个固定的带有三个径向筐的催化剂组合成的四段式、轴径向、工艺进气全分流、催化剂床连续、自卸催化剂的氨合成反应器。这种塔型也可以结合工艺的不同需要及用户的不同情况进行三段或四段床设计,二段或三段径向床变形设计。
内件见图4。
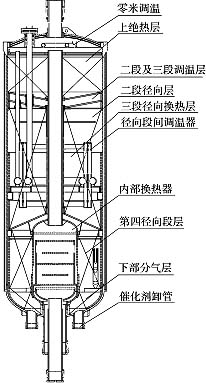
图4 ⅢJD合成塔结构示意
3.3 热回收单元
ⅢJD合成工序的所谓热回收单元由合成塔出口的废热锅炉、热交换器等组成。这个单元包含有两台换热设备和几根高温管线。当设计要生产高压蒸汽时,将设置蒸汽过热器,这也是大型合成技术用得较多的热回收方法。
我们在这部分主要是运用了一个“全分流”的流程,首先将热交换器的冷端温差加大,较好地保证了换热器在换热面积足够的条件下,进入水冷却器的循环气温度低。一个合成系统进入水冷的温度越低,也就是说合成塔在保证热平衡的条件下,进入水冷的温度越低,则合成塔外的废热锅炉回收的热量就越多,热量回收就越好。
(1)“全分流”的流程
“全分流”流程是ⅢJ系氨合成系统流程的一个特色,所谓全分流,即在冷气入塔时进行分流,出热交换器的热气入塔前也进行分流,进入合成塔反应器内件的气体同样进行分流。
图5为分流与不分流的流程比较图。
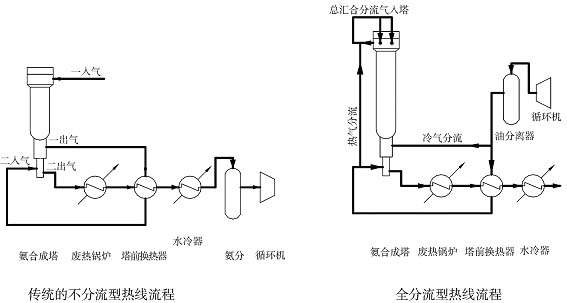
图5 分流与不分流的流程示意
从图5可以看出,不分流的流程中冷却合成塔环隙是用100%的入塔气进入合成塔内件和外壳之间的环隙,这样就有一进和一出气体,一出气体由于经过了合成塔环隙,将反应层的温度传递给了一出气,一般来说,一出气的温度高达60℃以上。这股气体将合成塔反应热的高位能热吸收了,变成了低位能热。这样,进入热交换器的入口气也比从一进来的气要高30℃以上,势必将会使进入水冷却器的反应气在同样换热器、同样冷端温差条件下提高30℃,也可以认为少回收了热量,即少产了蒸汽。
而“全分流”的流程仅只有10%左右的未反应冷气经塔内外筒环隙进冷管,约90%的未反应冷气进入热交。其优点是催化剂筐壁散失的热量仍回收到催化剂筐床层内,相当于减少了催化剂筐的热损失。
这股10%左右的“分流气”是保护合成塔壁的,使合成塔的塔壁温度在适当范围,也不能降得太低,因为温度降得太低了,高位能热将损失太大;塔壁温度过高了,筒体材料不能抗氢蚀,会影响运行安全。我们将这个温度控制在适当的范围内,这样既挖掘了设备的运行潜力,又不使高位能热向低位能无谓地转化;另一方面,这股10%的冷却环隙气并没有浪费,我们的流程是将这股气通过与热分流气混合后再次进入合成塔内,作为段间换热器的冷却用气,这样做到了能量的充分利用。
这种流程,进热交的冷气温度在35~40℃,结果可使进水冷排热气温度降到80℃以下,提高了热回收率,减少了设备投资(节省了一个软水加热器)。传统流程中,如果不设软水加热器,进冷排温度为120~130℃。
(2)“亚热壁”或“热壁”合成塔
如果采用提高合成塔热回收蒸汽压力的方式来回收合成塔热量,这样,就会有一个随着蒸汽压力的提高,热量逐步后移的过程。如表1所示,随着蒸汽压力的提高,出废热锅炉的循环气温度将上升,进入热交换器的总热量也增多,合成塔热气进口温度也将上升,合成塔内的热平衡也将变化,这样也要调整出合成塔反应器的出口温度来达到合成塔回收热量的效果。也会带来合成塔的环隙温度升高,从上述的“全分流”流程来看,也会使合成塔的塔壁温度有所调整。
表1 ⅢJD流程中的几种不同蒸汽压力下系统温度表
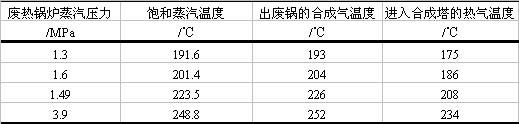
注:①依据ⅢJD流程中的设备及有关通用的设计条件来来计算;②均按废锅出口温差3℃来计算,按热交换器热段温差18℃来计算。
从表1可以看出,如果按回收蒸汽压力为3.9MPa,则采用一次进入合成塔的热气温度将会达到234℃,我们采用来热壁操作方式是将10%的冷气进入合成环隙,将合成塔环隙的温度最高点控制在200℃以内,这就是我们称之为“亚热壁”的操作方式,这样可以极大地简化工艺流程,提高热回收的品位和热回收率。ⅢJD合成塔大直径反应器,也有采用230℃塔壁温度的,由此来回收高压蒸汽。我们为山东瑞星化工设计的日产800t合成氨系统就是用这种设计理念进行设计的。
(3)高效换热型设备
在有先进按热能位高低回收热量流程的条件下,ⅢJD系统还采用了高效的热回收技术。以此来回收合成塔出口的反应热,用于自身热平衡,这主要体现在废热锅炉和合成塔内外热交换器的设备设计上。
塔外的废热锅炉,我们采用降低阻力的设计方法,采用了直通式或U型管式的废热锅炉回收合成塔反应热,在布管上和设备设计上,采用了尽量降低阻力的设计方法,提高了废热锅炉的热回收效率。
塔内热交换器我们采用了如前所述的细长形换热器,以及高效化的换热管,提高了换热器的传热效率;塔外换热器的设计,我们也采用了高效的横纹管换热技术,分段采用不同材料以抗蚀,极大地降低了高压容器的设备投资。同样条件下,同样的传热量,采用这种配套技术,使高压容器的投资下降近20%。
3.4 冷回收单元
氨合成反应器的转化率一般在20%以下,生产中要采用循环反应的方式,收集产品液氨方式为冷却和冷冻分离两种方式串联。因氨的物化性质决定,仅采用水冷却方式是不能使出口氨含量达经济运行水平的,工艺生产中采用了利用自身生产的液氨作为冷冻剂来冷冻合成循环气的方式,达到将合成塔进口循环气氨含量控制在3%以下的指标。
回收和利用好冷冻量,也是高压回路的一个重要问题。一般来说,我们要求经过“冷回收”后的循环气以尽量高一点的温度进入下一个设备。每生产1吨产品液氨用于自身冷冻的液氨量也要尽量少一点,这样可以达到冰机开启量少,达到节约电耗的目的。
ⅢJD系统从下述方面进行冷回收系统优化。
(1)三级冷却两级分离的冷系统流程
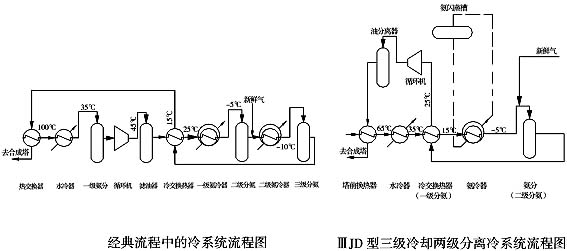
图6 冷系统流程示意
一般的冷系统流程与ⅢJD冷系统流程示意见图6。
从上述流程可以看到,传统的流程采用了水冷后设氨分,并有两级氨冷三级氨分的复杂系统。而ⅢJD的流程采用了十分简洁的冷系统流程——水冷一级冷却后再进入冷交进行进一步冷却,分离;第三级冷却为冷冻冷却方式,这一级采用液氨蒸发冷却合成氨循环气,将气相中未冷却的氨进一步冷却,冷却后再进行冷凝,然后第二次分离。含有大量冷量的冷气进入冷交换器内回收冷量后再入循环机。
这种流程的好处是在水冷后进一步冷却就可以在冷交下部将70%以上的液氨回收分离,降低了后续冷冻及分离的负荷,同时,由于分离靠前,后续的液氨吸收冷量的问题也解决了。另一方面也降低了冷系统的阻力。与经典的流程比较,冷系统的液氨蒸发量下降近30%,出冷交换器冷气的温度上升10℃以上。
ⅢJD在低压合成技术上,由于合成压力较低,氨分离要求的循环气温度较低,为节约冷量,一般设两级到三级的冷却系统,仍用二级分离方式达到尽量节约冷量的目的。
(2)高效冷却器及冷热交换设备
和“热回收”系统一样,“冷回收”系统照样用了高效换热技术,设计了一个运用高效螺纹管和特殊折流元件的冷交换器,将传热效率提高,减少了高压容器的投资,收到了回收冷量好的效果。
同时也设计了一个传热效果好的氨冷却器,采用了带闪蒸槽的液氨蒸发方式,将换冷段设计成高效流动型的冷换系统。同时提高了高压容器的使用效率,提高了使用安全性能。
通过上述两种措施,新的“冷回收”系统达到了设备配置最简单化,系统“冷回收”最大化的效果。目前运行的几十套大、中型ⅢJ合成系统,均采用这种流程及设备的冷回收系统。通常都能降低入合成工段的冷量消耗,降低合成工段的液氨加入量,一般可达到自用液氨返用于冷系统量比传统的流程及设备少100~200kg。同样的氨加入量将会使进口氨含量下降更多一点;冷交换器的冷气出口温度高达22℃以上。
3.5 分离单元
ⅢJD系统的分离单元分为油、水分离器和氨分离器两种类型,油、水分离主要是系统循环机及压缩来新鲜气的油、水及合成系统微量毒物的分离及净化。氨的分离分为高温部分的氨分离和低温部分的氨分离,主要是指冷交下部的氨分离和氨冷后的氨分离。
新鲜气的微量毒物及油、水的分离,ⅢJD系统主要采用分子筛系统来处理,当分子筛系统处理的气体达标后,这部分新鲜气可以直接补在合成塔进口。这样,可以减少合成系统循环量25%。但当分子筛效果不好时,我们设置了将补入气补到“冷系统”的净化方式,工程上常用两种方式并举,流程可以互换的方式来配置。
油分离器采用的为多级离心分离串超级过滤的方式来处理气体。氨分离器在高温分离段,主要采用螺旋管及螺旋流动型折流元件,使液氨在换热段边冷却边顺流,氨液滴长大后再进入离心分离段,再采用过滤分离方式来分离液氨。
低温段氨的分离采用三级到四级离心分离、过滤分离及超滤分离组合的分离方式,这样可达到在一定循环气温度下能分离液相氨90%的分离效果。大系统也采用了卧式氨分离器来集成分离冷系统出来的液氨。
采用这些设计方式,分离效果得到了提高,分离器的阻力降也比较小。
运用上述设计思想及设计方法,我们设计了多套氨合成系统,在全国很多厂家运用,均收到了良好的效果,目前正在进一步优化系统,使热回收量更大、系统能力更大。
4 ⅢJD氨合成系统的推广业绩及达到的技术水平
按照上述设计思想,我们创造的ⅢJD型氨合成系统在全国大中型合成氨企业推广面日益增大,1995年山东鲁西化工股份有限公司采用我公司设计和制造的31.4MPa级的DN1200合成系统,拉开了大直径合成塔研究和应用的序幕,此后相继开发了DN1400、DN1600、DN1800、DN2000、DN2200系统,近期又进行了DN2800、DN3200、DN3400的低压氨合成系统和二塔三塔串联低压及高压氨合成系统的开发。为我国合成氨自主技术的开发作了大量前瞻性的工作。
开发的DN1400合成氨系统在湖南大乘资氮集团成功运行近6年;DN1400系统还在江苏昆山锦港实业有限公司、山西丰喜集团临猗分公司、江苏新沂恒盛化工有限公司、山西天脊集团晋城化工股份有限公司等厂投入运行。公司开发的DN1600氨合成系统最早的一套在湖南岳阳天润化工股份有限公司(岳阳化肥厂),已运行近5年,相继又有河南心连心化工有限公司(河南新乡化肥厂)、河北邯钢集团化肥厂、福建三明化工总厂、山西晋成煤气化有限责任公司、河南骏马化工集团公司化肥厂等厂采用DN1600氨合成系统;开发的DN1800氨合成系统在山东瑞星化学工业集团公司于2003年底投入生产,相继有山东德齐龙化工有限公司三套的醇烃化配DN1800氨合成系统联合工段投产,江苏新沂恒盛化工有限公司的18·30工程中的醇烃化及DN1800氨合成系统投产,江苏华昌化工有限公司的18·30工程中的醇烃化及DN1800氨合成系统投产;开发的DN2000氨合成技术在山东德州化肥厂、河南心连心化工有限公司、山东明水化肥厂等企业相继投用;开发的DN2200氨合成系统近期将在山东鲁西化肥股份公司投入运行。
基于我公司在合成系统技术的先进性,2002年4月24~25日,中国氮肥工业协会组织全国合成氨方面的专家,对双甲和醇烃化净化工艺及合成氨技术进行了针对山西临猗现场的生产评议,评议认为:“……ⅢJD氨合成系统及主要设备结构均采用了优化设计,在国内外处于领先水平,建议在氮肥行业推广应用。”
二十多年来,ⅢJ系列氨合成技术在安淳人及广大用户的共同努力下,获得多种奖励。技术也被列为国家级重大科技成果重点推广项目。技术成果参加过维也纳、吉隆坡国际新技术新产品展览,获国家级新产品称号、获1995年度国家科技进步二等奖(迄今为止,国内合成塔内件最高奖项)、中国专利技术金奖、湖南省科技进步一等奖。
现在有400多家合成氨厂使用该技术及内件。现选择一部分大型塔的推广运行实例,来说明和验证产品及系统运行情况。
河南心连心化工有限公司 该厂2003年新投入一套150 kt/a合成氨装置,合成工段及净化精制工段采用了我公司的ⅢJD系统及醇烃化净化精制工艺来实现,装置于2003年8开车,合成氨生产500t/d,甲醇生产180t,系统压力只有26MPa。开工后,企业每天比原来系统天多创利润20~25万元。今年8月份,该厂230 kt/a总氨的氨合成系统及醇烃化净化系统也一次开车成功,这是我公司又一次与心连心化工公司的技术合作,本次设计采用了一套DN2000氨合成系统,这也是国际国内31.4 MPa级最大的氨合成系统。运行后,达到了日合成氨产量500t/d,甲醇产量180t/天的水平,系统运行压力仅18 MPa,目前正在进行大负荷生产调试,近期将达到日产700 t合成氨,系统压力仅23MPa,为我国特色的合成氨系统创造新的业绩。
山东瑞星化工集团公司 公司现有合成氨能力400 kt,曾于1996、1998年使用我公司的DN1200、 DN800ⅢJ-99氨合成系统各一套,于2003年底在400 kt/a合成氨技术改造中,率先采用了我公司的一套DN1800氨合成系统,于2003年底投产。投用之初,系统每天产合成氨620t,系统压力只有24MPa。目前运行近三年了,后串入一个合成塔弥补合成塔上部催化剂老化的不足,系统可以开到合成氨产量700t以上,整个分离系统尚能达到产量要求,为我公司设计的系统进一步挖潜改造提供了成功的经验。
江苏华昌化工有限公司 这个厂用了我公司三套氨合成及醇烃化系统,一套DN1600氨合成系统。开车近三年了,目前合成氨产量达到了600t/d以上,系统压力仅28MPa,达到了稳定、高效、节能运行的效果。
湖南岳阳天润化工股份有限公司 该公司目前拥有合成氨生产能力180 kt/a。2000年初,投用了我公司一套DN1600氨合成系统,此系统为ⅢJD系统的第一套,目前合成氨产量达450t/d,系统压力只有21MPa,到目前为止催化剂使用约6年。
山西晋城煤化工有限责任公司 该公司进行220 kt/a合成氨工程扩建时,采用了我公司的醇烃化工艺及氨合成工艺,于2002年12月投产了一套DN1600ⅢJD的氨合成系统,目前日产合成氨6000t,系统压力只有27MPa。
湖南大乘资氮集团有限公司 这是最早采用我公司ⅢJD氨合成系统的厂家,目前一套DN1200和一套DN1400氨合成系统,每天产氨和醇共计850t。综合经济效益十分显著。
除此之外,还有山东德州化肥厂、山东鲁西化工股份限公司、山东明水化肥厂、河南开封晋开化工公司、山东德齐龙化工有限公司、邯钢集团化肥厂、福建三明化工总厂、河南距马店化工总厂、江苏昆山锦港实业集团公司、江苏华尔润集团公司、江苏张家港锦港实业公司、山西丰喜集团临猗分公司、江苏新沂恒盛化工有限公司、天脊集团晋城化工股份有限公司等厂先后采用了我公司ⅢJD型氨合成系统。
我公司的ⅢJD型φ1200~φ2200 mm氨合成系统及氨塔内件在全国的应用是十分广泛,占合成氨厂塔型中的30%以上,占上述直径塔型的70%以上。
5 结束语
ⅢJD型氨合成塔系统及合成塔技术为我国自行设计,具有自主知识产权、适应我国国情的合成氨技术,湖南安淳公司从事大型化合成系统技术研究及系统开发近20年,运用了多项国家专利技术,创造了节能效果好的大型化系统,为合成氨产业的国产化走出了一条新路。采用了现代化的设计理念及新材料、新的技术进行设计。随着更大型化的合成系统投产,将进一步检验安淳公司的技术水平及技术成果,为我国合成氨的国产化提供成功的经验。
