0 前言
目前中串低、中低低、全低变流程是国内UGI炉制气的合成氨厂变换工艺主要方式,其所采用的 Fe-Cr系中变催化剂对原料气的硫有一个最高限量,而所采用的Co-Mo系低变催化剂对原料气的硫有一个最低限量,本文在此结合国内的实际工况给予分析阐述。
1 Fe-Cr系中变催化剂的耐硫含量
1.1 硫中毒化学反应
铁铬催化剂的活性组分Fe3O4与H2S发生下列反应:
Fe3O4+3H2S+H2→3FeS+4H2O =-75 kJ/mol
显然与气体中的蒸汽含量(汽气比)有关,其各汽气比下的平衡H2S浓度见表1、图1。
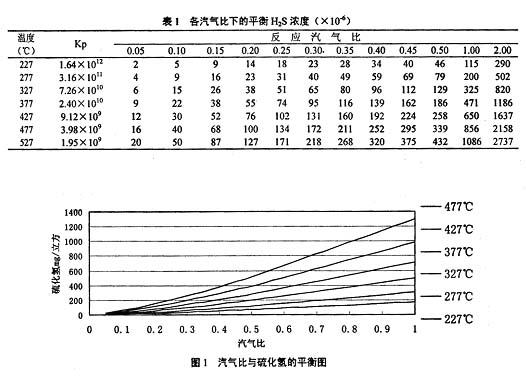
从表1及图1中可见H2S与汽气比关系很大,当汽气比小于0.5时,其平衡的H2S急剧减少。国内中变催化剂的产品说明书都有耐硫指标,一般都在400mg/Nm3左右,但都无相对应的汽气比要求,其实催化剂的硫中毒(或耐硫)指标都是在某一汽气比下才有意义。目前企业或行业标准的活性检测的汽气比为1.0或2.0,测试温度为300℃,从表1可知其硫平衡值为(300~700)×10-6,即455~1000 mg/Nm3,活性检测时耐400mg/Nm3硫是没有问题的,因此,这种耐硫指标对实际应用是没有意义的。有的中变催化剂即使在活性检测时能耐高硫,其实也是暂时的。当然,有的催化剂添加了别的活性组分如MoS2那就另当别论了。 1.2 中串低工艺最高耐硫含量
原料气以CO~29%、CO2 ~9%、H2~38%计,各种净化方式的耐硫含量计算结果见表2。
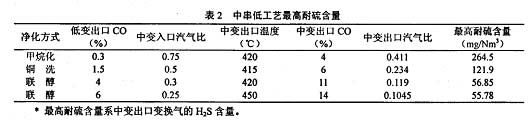
1.3 中低低工艺最高耐硫含量
原料气以CO~29%、CO2 ~9%、H2 ~38%计,各种净化方式的耐硫含量计算结果见表3。
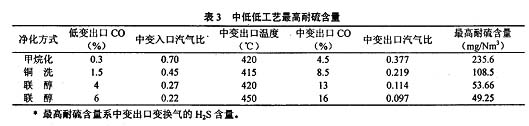
1.4 实际工况下的硫中毒
大部分有机硫化物在CO变换反应过程中很快转化为H2S。
COS和CS2接近于全部转化为H2S:
COS+H2→CO+H2S =9.2kJ/mol
COS+H2O→CO2+H2S =-34.7kJ/mol
CS2+2H2O→CO2+2H2S =-60.4kJ/mol
随着变换反应的进行,虽然温度逐步升高,但床层中的汽气比愈来愈低,有机硫转化无机硫也愈来愈多,H2含量也愈来愈高,其相应允许的最高H2S含量愈小,即耐硫性却愈来愈差,出现下部催化剂硫中毒,而上部比较完好的现象。
与其它催化剂类似,由于H2S在催化剂表面发生化学吸附,尽管浓度还不足以使催化剂生成相FeS,但催化剂活性却已下降。因此,合适的硫含量应以反应出口的汽气比计算并考虑硫的吸附能力,要低于理论计算值为宜。另外常规的硫化氢分析的取样不可避免有冷凝水,硫化氢的溶解会使分析结果低于实际变换气的硫含量。因此建议实际工艺的最高耐硫量(分析值)取计算值的~80%。
2 Co-Mo系低变催化剂的最低硫含量
2.1 反硫化的提出
由于钴钼系变换催化剂的活性组份为Co-Mo硫化物,需要一定的H2S来维持其硫化物组份。到目前为止,对钴钼系催化剂的硫化态结构,尤其是活性中心结构的认识尚不够深入全面,一般认为该催化剂的活性组份主要以MoS2的形式存在,用MoS2与H2O反应来计算其平衡H2S浓度,MoS2在一定的蒸汽分压下存在以下反应:
MoS2+2H2O=MoO2+2H2S
所以在反应气中应有一定量的H2S存在,当H2S低于其平衡浓度时上述反应会向右进行,即发生反硫化现象,由于反应物和生成物的热力学数据来源不同,利用热力学计算出的最低H2S含量也相差颇多,而且与实际工况不符。因此,探讨最低硫化氢浓度,有助于该催化剂的开发,也有利于判断催化剂失活的原因。
2.2 催化剂对H2S的吸附
众所周知,合成甲醇的铜基催化剂对原料气的S含量极为敏感,要求S<0.1×10-6。
但从Cu+H2S→CuS+H2 (A)
2Cu+H2S→Cu2S+H2 (B)
热力学计算其最低H2S含量反应(A)为7%;反应(B)为10×10-6,远高于实际工况的0.1×10-6。
甲烷化的镍催化剂:
Ni+H2S→NiS+H2
热力学计算其最低H2S含量为60×10-6,而实际工况下H2S>1×10-6时就开始中毒。
中变铁铬催化剂:
Fe3O4+3H2S+H2→3FeS+4H2O
在350℃,汽气比为0.7,热力学计算其最低H2S含量(干基)为401×10-6(609mg/Nm3),但对某些纯Fe-Cr系中变催化剂在H2S含量为100×10-6时就活性下降,生成FeS。
氨合成铁催化剂:
Fe+H2S→FeS+H2
热力学计算其最低H2S含量为40×10-6,而实际工况下H2S>1×10-6时就开始中毒。
为什么实际工况与理论相差如此之大呢?其原因是H2S具有未共用的电子对(S元素最高可为+6价),可以和催化剂活性组分中过渡金属的可共用电子形成配价键而强烈地吸附在催化剂的表面上。从而使表面的H2S浓度大大高于气相中的H2S浓度,这方面不少学者作过研究,都证实了这一点。
同理,由于MoS2中的Mo还有2个可共用的电子(Mo元素可为+6价),H2S也会与MoS2形成配价键吸附在催化剂的表面,使表面的H2S浓度大于床层气相的H2S浓度。由于MoS2供共用电子的能力比Cu、Fe、M、Fe3O4要弱得多,其对H2S的吸附能力也较小,为此我们进行实验与计算,发现催化剂的活性组分比例、制备方法、硫化前的钴钼状态、添加剂的种类、硫化工艺的不同,其H2S吸附能力相差较大,吸附系数为1.5~4之间,正如不同的Fe-Cr中变催化剂由于制备方法的不同其H2S吸附能力相差较大,从而影响其耐硫性能一样。研究中又发现催化剂表面吸附H2S能力越大,抗低硫性能就越强,而其活性就越差,这可能是由于吸附的H2S覆盖了活性表面之故,所以不同的变换工艺(中串低或全低变)所采用的催化剂的吸附H2S能力也应有所差别。
2.3 B303Q催化剂的最低H2S浓度表
不同钴钼低变催化剂其最低硫含量也不同,现摘录湖北省化学研究院开发的B303Q催化剂的最低H2S浓度见表4、表5。
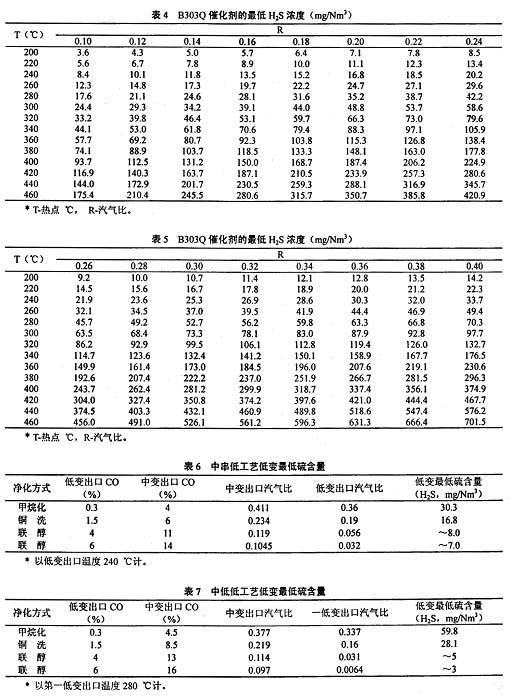
2.4 中串低工艺低变段最低硫含量(见表6)
2.5 中低低工艺低变段最低硫含量(见表7)
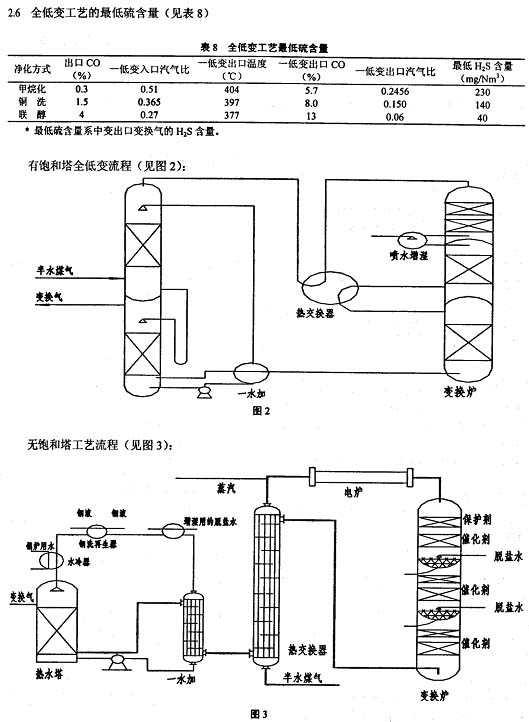
由于二次喷水增湿,与有饱和塔流程相比,进口的汽气比更低,最低硫含量为有饱和塔的80%,计算从略。
2.7 重新(二次)硫化
重新硫化的原理是使反硫化失活产生的Co-Mo氧化态再转化为硫化态,除此以外重新硫化的高温也会使床层冷却的氯化铁、铵盐、油污等固体杂质再行升华、挥发以恢复部份活性,有的厂重新硫化时出口管“冒白烟”就是氯化铵的气体,而对中变的粉尘却是无能为力,所以一般效果都不大。
当然,在低温下将催化剂卸下、过筛、重装,再硫化其效果要好一些,一则可以将粉尘固体杂质去除掉,解决偏流引起的失活,二则使催化剂中污染较少的“背风面”与污染较重的“迎风面”混合,也能提高活性,很多厂二次硫化效果不错的原因就在于此,而绝非有些供应商所宣传的“复活技术”。
2.8 抗毒剂与保护剂
很多文章认为半水煤气的氧是毒物,其实氧不是毒物,否则硫化就不能用半水煤气了,国外有专利报导可在硫化及开车时加入空气或氧气提温的做法,我研究所在在硫化升温或开车时为提高温度缩短时间也多次采用加空气或氧气的方法,对催化剂无任何危害。抗毒剂的作用主要消除半水煤气的各种有毒物质,但同时也有促进氧与氢与一氧化碳的反应,所以往往有一定的温升,“抗氧剂、除氧剂”的称谓也由此而来。
与各种催化剂一样,抗毒剂也有“中毒”的问题,这主要发生在工况不正常的情况下,此时半水煤气会产生“某种”毒物,这会影响抗毒剂的作用,为避免这种个别情况发生,我们研制了一种“保护剂”,当然生产正常时其作用是不大的。
3 结论
前面仅仅从硫中毒的概念讨论了各种变换流程中Fe-Cr系中变催化剂的最高耐硫含量,并从反硫化的概念讨论了Co-Mo系催化剂的最低需要硫含量。换言之,中变催化剂的含硫量愈低愈好而钴钼低变的含硫量却愈高愈好,使用时要恰当控制其变换气的硫含量的范围。当然降低操作指标,提高温度,增加蒸汽消耗其硫含量的指标也会‘宽松’,使用寿命也会延长,这就是有些中低低流程的操作水平于中串低相当的原因。根本的解决方法是采用全低变工艺,全部使用Co-Mo系催化剂。
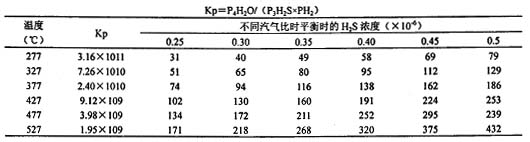
