1 概述
甲醇最早是在木材干馏中发现的,直至173年后,即1834年杜马(Duma5)等才用化学法合成纯甲醇,1923年BASF公司在高温高压下和锌铬催化剂床层用CO、H2合成甲醇实现工业化。近几十年,由于脱硫技术的进步,低压低温铜系催化剂开发成功,低压合成甲醇发展很快,逐步在取代高中压条件下生产甲醇,因为低压甲醇的质量好,原料气和能耗低,成本低,投资少。
在高铜锌铝催化剂床层用低压法合成甲醇在国内外已经普遍使用,但低压合成甲醇的合成塔形式在不断改进之中,按移走反应热的方式,有两大类:一类是气气换热式,包括冷激式、冷管式、间接气气换热式或混合式;二类是水气换热式,其中包括水管式(管内为水汽混合物)、管式床(管外为水汽混合物)。水管式低压甲醇合成塔是首次在山东省德齐龙化肥厂使用,一次开车成功,使用半年来,比其它形式合成塔有明显的优势。
2 甲醇合成反应基本理论及设计思想
主反应:CO+2H2=CH3OH+102.5KJ/mol
副反应:2CO+4H2=(CH3)2O+H2O+200.2KJ/mol
CO+3H2=CH4+H2O+115.6KJ/mol
4CO+8H2=C4H2OH+3H2O+49.62KJ/mol
nCO+2nH2=(CH2)n+nH2O+O
CO2+H2=CO+H2O-42.9KJ/mol
1、CO与H2合成甲醇是一个可逆减体积放热反应,其主反应是生成甲醇,也有生成二甲醇、变碳醇、烃类CH4的副反应,还有CO变换反应的逆反应。
2、压力高、温度低有利于反应的化学平衡,两者配合,应是高压高温、低压低温有利。
3、压力为50MPa~80MPa,温度200℃~300℃,反应热为97068.8J/mol~99370.0J/mol。
4、在铜基催化剂上的合成甲醇的反应过程为①扩散→②吸附→③表面化学反应(产物)→④解吸→⑤扩散,反应速度与五个过程有关,但控制过程为③(即化学反应)过程,因为其速度最慢,要提高总过程速度,关键是提高化学反应速度。
5、低压合成甲醇催化剂是铜含量达50%以上铜锌铝催化剂,其使用温度范围狭窄,为210℃~280℃,而最佳温度范围为220℃~260℃。
6、铜基催化剂大都用共沉冷法制成,结构疏松,内表面积大,这有利于加快反应速度,同时含有较多金属氧化物如氧化铝,因而其导热系数小,传热性能差,机械强度低,因而保持催化剂高活性,避免过热超温是至关重要的。
3 气冷式甲醇合成塔
CO与H2反应是强放热反应,与H2、N2气体合成为氨比较,生成每mol甲醇比氨几乎要多一倍,而合成甲醇的铜系催化剂的使用温度范围只有50℃左右,合成氨的铁系催化剂使用温度120℃~150℃,因此如何将甲醇反应热快速移走,使其温升<50℃是甲醇合成反应器设计的重要问题。
对气固可逆放热反应,一般用未反应冷气直接或间接被反应气加热,使未反应气多次加热至反应温度,反应气多次升温—降温,使之保持在催化剂活性温度范围之内,不超温,也不“熄灭”。因为气体的热容很小,反应放出热,温升大,即温度波动大,使升温—降温次数调温手段复杂化。例如用四段间冷绝热反应器,反应后甲醇净值为5.7%,如果一段进口为220℃,净值为增加1.43%,则出口温度达264.96℃,即温升为43℃,由此,剩下的每段净值增加1.42%,则每段温升保持43℃左右,对低压高铜催化剂如此大的温度变化,会使活性过早衰退,使用寿命缩短,对于大型装置频繁更换催化剂,不只是催化剂成本增加,而且升温还原占用生产时间,造成损失更大。
冷管气冷式甲醇反应床,其床层装有冷管束,冷管为小管径,根数多,管内末反应冷气与管外折流式,每根折流管中的下降管与反应气并流,上升管与反应气逆流。并流管内外传热温差上大下小,而逆流管下大上小,这就使床层上下传热趋于均匀和缓,折流式冷管束适用温区很狭窄的铜系甲醇催化剂的要求。但是气冷式用自身热循环,反应后热气体加热未反应冷气体,对反应床,使之保持在催化剂活性温度范围内,不至于超温,对未反应气,使之达到催化剂反应所必要最低温度:如此反就热除产生少量低压蒸汽外,主要被冷却水带走。
以全塔做热平衡的对象,进行热平衡计算:
Q未反应气=10000×1.38×40=552000
Q反应热:517.75×4134.44=2140606.31
Q反应气=9068.05×1.35t=12151.18
1000.00—进塔未反应气Nm3
9068.05—出塔反应气Nm3
517.75—反应生成粗醇Nm3
4134.44——每Nm3粗醇生成热KJ/Nm3
1.38—未反应气比热KJ/Nm3℃
1.34—反应气比热KJ/Nm3℃
t—反应气出塔温度
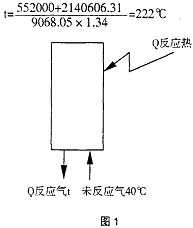
热气经废锅生产0.6MPa低压蒸汽,其饱和温度160℃,出废锅温度为168%。产生低压蒸汽W:

10000Nm3进塔=824.17kg/t粗醇
2713.84 0.6MPa饱和蒸汽热含KJ/kg
废锅出来热气(168℃),用32℃冷却水冷却,冷却水升温至40℃,耗冷水量:
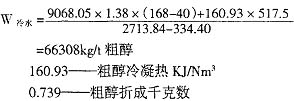
上述热衡算,说明气冷式热利用率低,只能产生少量低压蒸汽(0.6MPa,524kg/t粗醇),而冷却水消耗很大(66.30t/t粗醇)。
4 水冷式甲醇塔
所谓水冷式,即在反应床层之中布水(沸水)管,或把反应管置于沸水之中,反应热将沸水汽化为蒸汽。
仍以进塔气为10000Nm3,出塔气9068.05Nm3,产粗醇517.75Nm3,用简单热平衡计算副产蒸汽量、冷却水耗。
4.1 求出塔温度
以水冷前的塔外热交为热(直线框)平衡对象计算反应气进热交为t,
出热交设为60℃,
未反应气进热交为40℃,
出热交为210℃。
Q反应热=2140606.31KJ
Q冷进=10000×0.33×40=552000
Q冷出:10000×1.38×210=2898000
Q热进=9068.05×1.34t=12151.19t
Q热出=9068.05×1.34×60=729071.22
t=2898000+72907122-552000/1215U9=253℃
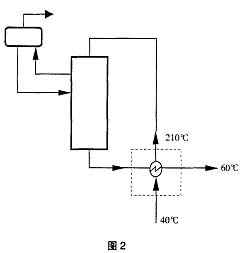
4.2 耗冷却水量
60℃反应热气经水冷至40℃,冷却水由32℃,升温至40℃,耗水量:
W={9068.05×1.38×(60-40)+(160.9× 517.7)}/.739×(40-32)×4.12=13695kg/t粗醇
4.3 副产蒸汽量
产生34.00MPa饱和蒸汽(240℃),热含2798.51KJ/kg,进水温度80℃,热含334.40KJ/kg,副产蒸汽:
w=Q冷进+Q反应热-Q热出/2798.51-334.40=780kg/1000Nm3进气/1055kgt粗醇
相当于每吨精醇1306kg
将上述热量计算列表:
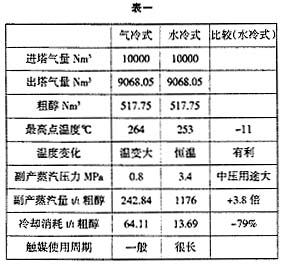
由表可看出,从节能的观点比较,水冷式比气冷节能,其中副产蒸汽压力高,蒸汽量多3.8倍,冷却水量少79%。
另外还有如下优势:
1、水冷式运行温度恒定,比气冷运行平缓,以副产蒸汽压力调控反应床温度比气冷式简单可靠。
2、水冷式用惰性气升温,还原时逐步增加H2%,升温还原安全可靠。
3、水冷式反应热回收与反应催化床融为一体,气冷式反应器与反应热回收器分置,不另占地,五连接管道。
4、水冷式不设电炉升温,气冷式设置电炉升温,可靠性好。
5 水管式与管壳式
水管式与管壳式甲醇合成塔,都属于沸水汽化为蒸汽移走反应热的反应器。其区别在水管式是水在管内,管外为催化反应床;管壳式是水在管外,管内装填催化剂。由此在结构细节和特性方面有很多的不同, 其基本结构(如图3、4),两者结构区别如表2。
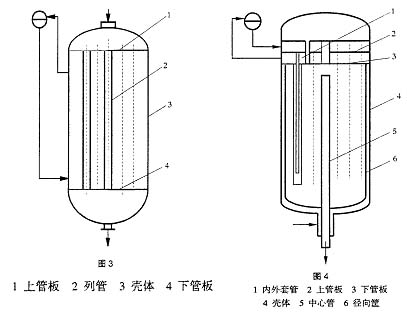
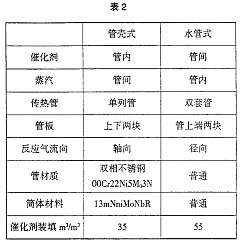
6 水管式甲醇塔的优点
1、沸腾水管形如刺刀和刀鞘,为悬挂式,即只焊一端,另一端有自由伸缩空间。管子受热伸缩没有约束力,无需用线膨胀系数小的昂贵SAF2205双相不锈钢,只用普通不锈钢管就可,壳体不受管子伸缩力的影响,壳体材质也要求不高,筒体上下厚度相同,无需设置加强筒体,无需用高强度20MnNiM0YbR等类特型钢材,筒体材质用复合钢板即可。
2、容积系数大,管壳式甲醇反应器的容积利用系数约为35%左右,JJD水管式甲醇塔或达55%以上,这意味着同样的压力容器空间中,水管式反应器将比管壳式反应器将多装填催化剂。如我公司设计的JJDΦ2800低压水管式甲醇塔催化剂装填可达58t(38m3)。
3、JJD水管式甲醇塔为全径向流程,即反应气垂直通过沸腾水管和被水管包围的催化剂柱层,从操作原理上讲曲线由多个反应放热—冷却锯齿形阶梯组成的“肚形”曲线(如图三),热点与起点,终点温差小于5℃。反应净值高,出口粗醇可达5~6%,单位催化剂产醇量高。
4、JJD水管式甲醇塔单位容积传热面积大。Φ2800塔传热面积比管壳式塔传热面积大23%,这就适应了甲醇合成反应热大、冷却负荷大、要求换热面积大的特征。
5、JJD水管式甲醇合成塔升温还原用蒸汽加热,惰性气还原,快速而安全。
6、JJD水管式甲醇合成塔为全径向塔,塔阻力非常小,为0.1MPa左右。
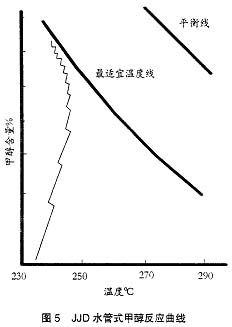
7、JJD水管式甲醇合成塔催化剂装填容易:如JJDΦ2800甲醇塔,装填58吨催化剂,24小时即装填完毕,比管壳式塔装填速度快得多。
8、操作弹性大:设计可控传热温差较大,适用催化剂不同活性阶段不同工况,例如初期操作温度220℃-230℃、合成压力3.0MPa至4.0MPa的工况,后期操作温度260℃~280℃、合成压力4.0MPa至6.0MPa的工况。第一个Φ2800塔在山东德齐龙化工集团投入使用初期:系统压力2.9MPa~3.3MPa,蒸汽压力1.8MPa,温度220℃运行,使用八个月后,日产量340t~350t,温度为230℃,压力3.2MPa3.5MPa。
9、JJD水管式甲醇合成系统简单,合成塔既是反应器,又是一个无需燃料的中压锅炉,在系统中不另外设置废热锅炉,进水冷的热气温度即降至50℃-60℃。
10、JJD水管式甲醇合成塔通过调整沸腾水管布局,适用于高CO%含量的工况变化,也适应惰性气含量高的工况变化(联醇或副产氨的工况)。
11、JJD水管式甲醇塔基本上不受高径比限制:能力大,直径不一定很大,即单塔能力增大。
12、设备更新时,只需更换内件部分部件,外壳继续使用。
13、设计工况温和—恒温等温低阻,催化剂使用寿命长,催化剂成本低。
7 结论
CO与H2合成甲醇是一个强放热可逆放热反应,合理地移走反应热是设计合成塔首先要考虑的问题,从移走热量方式类分:有气冷式与水冷式,水冷式比气冷式节能,控制运行平稳。水冷式中又有水管式和管壳式,水管式又比管壳式优势更多。经过第一套Φ2800JJD水管式甲醇合成塔运行表明,它有容积利用系数高、单塔能力大、无需昂贵的双相不锈钢管材、阻力小、副产中压蒸汽多、循环电耗小、冷却水耗小、升温还原容易、操作控制简单、运行弹性大、适用性强、装卸催化剂容易等优点,因此应用前景很好。
