青岛碱业股份有限公司天柱化肥分公司(原山东平度化肥厂)具有合成氨生产能力13万吨/年,尿素生产能力16万吨/年,碳铵生产能力8万吨/年,2001因为甲醇市场看好,技改时上了一套Φ1200的甲醇装置(下面简称1#甲醇装置),2003年技改时又上了一套Φ1200的甲醇装置(下面简称2#甲醇装置),使甲醇生产能力达4万吨/年,其中1#甲醇装置中甲醇合成催化剂从2001年12月开车投用到2006年6月才更换,甲醇合成催化剂连续运行了4年6个月。2#甲醇装置中甲醇合成催化剂于2003年12月开车投用,至今还在使用,两套甲醇装置净化中的精脱硫采用的是湖北省化学研究院开发的JTL-4常温精脱硫工艺。
本文就应用常温精脱硫技术,提高甲醇合成气的净化度,延长甲醇催化剂的使用寿命,提高甲醇生产技术水平的实践作一简要总结。
1 生产工艺及设备情况
1#甲醇装置于2001年12月投入运行,其内件采用的是杭州林达的均温型内件,内装南京化学公司研究院的C207甲醇合成催化剂14.75吨,甲醇塔催化剂床层体积9.8m3,还原时采用的方法是高氢还原,以铜洗精炼气为介质,还原操作压力5.0~5.5MPa,整个还原过程同平面温差<5℃,轴向温差<10℃,出水量十分均匀,还原最终温度240℃。1#甲醇装置于2001年12月投用到2003年12月份,一直是全气量通过,通过气量为52000m3/h,热点温度初始为235±5℃,甲醇合成前气体组份如下:CO占3.0~6.0%,CO2占0.4~0.6%,甲醇合成后气体组份如下:CO占0.6~1.0%,CO2占0.1%,同平面温差<5℃,轴向温差<15℃。
2#甲醇装置于2003年12月投入运行,甲醇塔催化剂床层体积9.8m3,内装C207甲醇合成催化剂14.75吨,其内件采用的也是杭州林达的均温型内件,2#甲醇合成塔与1#甲醇合成塔并联运行,2#甲醇合成塔的内件与1#甲醇塔内件一样。两套系统共计生产甲醇12.8万吨,其中1#甲醇合成塔生产甲醇8万吨,2#甲醇合成塔生产甲醇4.8万吨,其生产情况如表1:
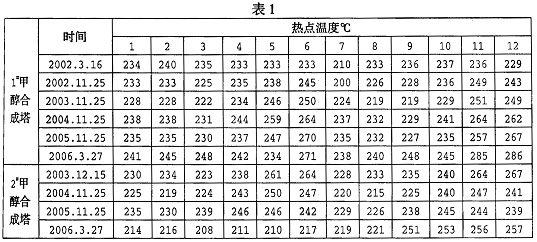
2 精脱硫工艺的选择与应用
由于联醇生产采用高活性且操作温度范围仅30~50℃的铜基催化剂,铜对硫十分敏感,据文献介绍1mol的铜基催化剂只需要0.000864mol的硫就能使其完全丧失活性。因此,原料气中硫含量的高低,就成为决定铜基催化剂的活性与使用寿命的关键因素,而且在全气量通过的联醇生产工艺中,进入甲醇合成塔的新鲜气量是单醇生产气量的2.5~3倍以上,故有许多联醇生产厂因原料气净化度差而导致铜基催化剂使用寿命很短,因此联醇生产时,必须在甲醇合成前上精脱硫。为了摸清原料气中硫化物的含量及分布,我公司邀请湖北省化学研究院的技术人员对我公司相关岗位的工艺气硫化物采用HC-2型微量硫分析仪进行了测定,最终采用了湖北省化学研究院开发的JTL-4常温精脱硫工艺,其工艺流程方块图如下:
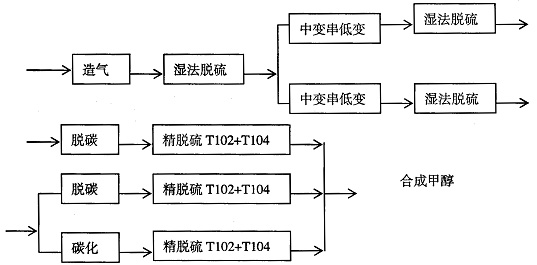
JTL-4常温精脱硫工艺是湖北省化学研究院开发的一种真正常温下精脱硫工艺,其主要由两部分组成,即T102活性炭精脱硫剂串T104有机硫转化吸收型精脱硫剂。常温下T102精脱硫剂主要脱除H2S,T104精脱硫剂脱除少量COS和CS2,这样将原料气中的硫化物(主要是H2S、COS和CS2)脱除至小于0.1ppm,彻底消除了硫化物的毒害作用,有效地保护了甲醇合成催化剂。通过我公司近五年的实际运行证明其效果是显著的,我公司1#甲醇塔甲醇合成催化剂使用了4年6个月,创国内最好记录。精脱硫工段硫化物分析情况如表2:
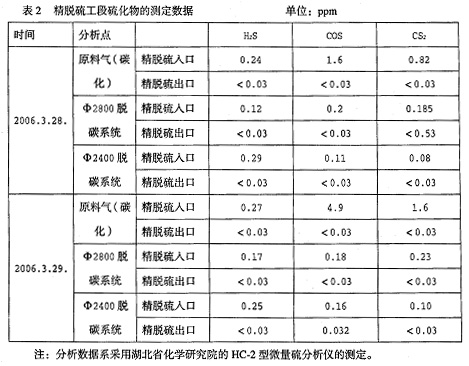
3 效益浅析
实践证明,应用常温精脱硫后具有显著的经济效益,单就延长甲醇合成催化剂使用寿命,减少甲醇合成催化剂的使用量而言,如青岛碱业股份有限公司天柱化肥分公司13万吨NH3/4万吨甲醇,每少更换一次触媒,则节省甲醇合成催化剂费用50万元,按应用常温精脱硫后4年的时间,少更换两次甲醇合成催化剂,则节省甲醇合成催化剂费用100万元,更换一次催化剂前后减少生产天数每次以l0天计,每天生产精甲醇以100吨计,两次更换催化剂的时间生产精甲醇2000吨,则增加效益150多万元,还有更换催化剂时开、停车费用等,而精脱硫剂费用约50多万元,使用寿命达5年以上,综合经济效益是可观的。
4 结束语
4.1 青岛碱业股份有限公司天柱化肥分公司(原山东平度化肥厂)在联醇技改中通过应用JTL-4常温精脱硫工艺和均温型甲醇合成塔内件,在工艺气中硫化物得以彻底脱除的同时,严格管理,精心操作,从而有效地保护了甲醇合成催化剂,甲醇催化剂生产强度达8160t/m3催化剂,并取得了联醇单塔合成催化剂使用寿命达4年6个月的业绩的国内最好记录。
4.2 JTL-4常温精脱硫工艺实现了真正常温(10~40℃)精脱硫,可同时精脱H2S、COS与CS2,具有流程简单,设备少,投资省等优点,精脱硫剂使用寿命达5年。实践证明,这一常温精脱硫工艺值得推广应用。
