湖北省化学研究院于1984年开始研究球形耐硫变换催化剂,即B302Q。该催化剂首先应用于中小型化肥厂的中串低工艺,于1988年完成了国内第1个中型厂的中串低工艺改造。在下一步是研究串2个低变的中低低工艺还是3个低变的全低变工艺的问题上,经比较后认为中低低本质上仍然是中串低工艺,故将下一个研究目标确定为全低变工艺。该项研究于1989年开始工业试验,经过18年的开发和改进,全低变工艺技术逐步从不成熟走向完善,目前已成功地应用于国内外200多套大小不同的装置中,为化肥等行业的节能降耗及甲醇工业的发展做出了积极的贡献。笔者作为该项技术的发明人之一,拟在全低变工艺成功实施200例之际,对该工艺改造的理论基础和技术优势进行总结,以供业界决策者和技术人员参考。
1 全低变工艺研发过程
全低变工艺的研究开发过程大致可分为以下4个阶段。
(1)第1阶段为理论研究、保护剂研究以及工业实验阶段,时间为1989年,在湖北郧县化肥厂进行了第1次工业试验,取得阶段性成果。
(2)第2阶段为工业应用初级阶段,时间为1990~1991年,在湖北利川市化肥厂进行第1次工业应用,同年又在湖北的武昌、蕲春,江苏淮阴、盱眙、金湖等11个化肥厂进行了工业应用。上述各厂均是在原中串低或中变流程基础上进行简单改造完成的。虽然通过了技术鉴定,但当时该技术仍存在3个问题:①设备不配套;②工艺不完善;③催化剂存在失活问题。
(3)第3阶段为技术完成阶段,时间为1992年,在江苏丹阳化肥厂实施第1套标准设计的全低变工艺。该厂有1炉催化剂连续使用了12年,吨氨耗蒸汽≤250kg。江苏丹阳化肥厂全低变工艺的成功实施,标志着全低变技术从工艺设计、设备配套到催化剂的失活等问题全部得到解决,同时还证明全低变技术从不成熟走向了完善。
(4)第4阶段为技术推广阶段,时间为1993年迄今,全低变技术开始大范围地在中小型氮肥企业推广运用。近5年来随着甲醇行业的发展,全低变技术在这一领域得到了普遍采用。该技术在大量的工艺实施中,技术本身也得到了不断完善,如全部取消调温水加热器的喷水增湿技术,无饱和塔流程,部分变换串中温水解技术等。这一阶段存在主要问题有:①不具备开发全低变技术的催化剂生产单位也开始推广全低变工艺。据不完全统计,先后有5个生产耐硫变换催化剂的单位在10多家中小型企业进行全低变工艺的工业应用实施工作,均以失败告终;②在这些失败的案例发生以后,少数技术人员在不明白失败真实原因情况下对全低变技术作出了一些不科学的评价,在行业内造成不良影响;③有些企业对全低变工艺的一些技术细节重视不够,操作控制不严也影响了全低变技术的经济效益。
2 铁铬中变催化剂的不足之处
近20年来,在变换催化剂和变换技术的工业实践中经常有企业反映Fe-Cr系中变催化剂的一些问题,最普遍的问题是相当多的中小型化肥厂每年大修时都对中变催化剂进行1/3~1/2不等的更换处理,不仅劳动强度大,而且增加了购买催化剂的费用。经调查研究发现,无论是中串低工艺还是中低低工艺,Fe-Cr系催化剂都会表现出以下4个突出的缺点:①活性温度高,导致热损大,蒸汽消耗高,阻力相对也大;②相对于耐硫低变催化剂而言,易粉化,易被硫等毒物中毒,使用寿命短;③在相同的生产能力前提下,使用Fe-Cr催化剂需要较大型的设备,因此一次性投资和维修费用均高于全低变工艺;④费托反应问题。笔者针对这4个问题产生的原因分析如下。
2.1 Fe-Cr催化剂打片成形
目前工业中使用的Fe-Cr催化剂均是采用物理方法打片成形,一直存在着“活性较好,强度较差”的问题。虽然催化剂牌号不断涌现,但这一“老大难”问题至今未能得到彻底解决,对催化剂的粉化留下了隐患。
2.2 费托副反应与硫的影响
当CO/CO2摩尔比在1.6以上,进口汽气比小于0.6时,副产物的生成量可达到百万分之数百(见表1)。虽然在0.8 MPa条件下情况会有所改善,但也要引起足够注意。国产中变催化剂的进口汽气比一般不宜小于0.4。
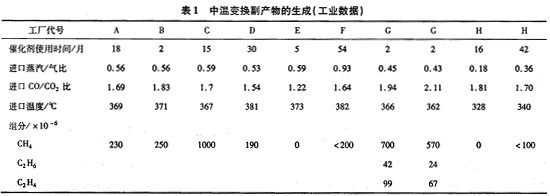
这个问题在国内多个甲醇企业发生过,具体表现为催化剂的使用寿命≤0.5年,且粉化明显。当气体中有硫(如国内的固定床间歇造气)过度还原生成的铁将发生化学反应:Fe+H2S→FeS+H2。该反应的平衡H2S很低,极易生成FeS,见表2。
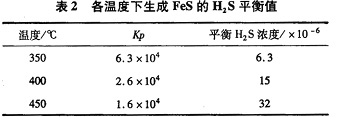
此时被还原的铁与变换气中的H2S反应生成低活性的FeS。该情况下虽无烃类生成,但影响催化剂的活性,国内企业多属此类工况。生成的FeS与蒸汽发生下列化学反应:
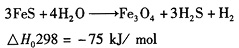
在H2O及H2S含量波动的情况下,特别是在平衡线上下波动时,催化剂在FeS与Fe3O4之间反复进行相变。尽管催化剂活性会较好(介于FeS与Fe3O4之间),但会使催化剂的强度受到严重影响,出现粉化而使床层阻力增加,甚至将破碎的粉尘带入低变段,造成低变催化剂的失活。
2.2.1 气体含硫量较低
当气体的含硫量较低时,有可能发生上层还原的铁作“脱硫剂”,下层的催化剂处于“无硫气体”工况。此时有可能发生费托副反应,通常的表现是变换后甲烷含量提高,严重时也会生成乙炔,导致铜洗带液。
2.2.2 汽气比过低
当汽气比过低(≤0.3)时,可能直接引发以下化学反应。
Fe3O4+6CO→Fe3C+5CO2
5Fe3O4+32CO→3Fe3C2+26CO2
发生工况为单醇、联醇工艺,或者开车初期负荷很低情况下,如在合成催化剂升温还原时或为提高铜液的铜比时。此时变换出口一氧化碳含量提高,汽气比非常低,极易引起“过度还原”继而生成可引起费托反应的碳化物。一旦生成可引起费托反应的碳化物,在正常的工况下是不可逆的,这就是有些用户长期产生铜洗带液的原因。
2.2.3 较高压力的变换反应
铁铬催化剂的活性组分Fe3O4与CO发生下列化学反应:
Fe3O4+6CO→Fe3O+5CO2
5Fe3O4+32CO→3Fe3O2+26CO2
该反应为体积缩小反应,当反应压力较高(≥2.0MPa),n(CO)/n(CO2)之比较大时,容易生成铁碳化合物,从而产生F-T反应,既影响活性又影响强度。
2.2.4 低汽气比下的硫中毒
铁铬催化剂的活性组分Fe3O4与H2S可发生下列化学反应:
Fe3O4+3H2S+H2→3FeS+4H2O
△H0298=-75 kJ/mol
显然与气体中的蒸汽含量(汽气比)有关,其各汽气比下的H2S平衡浓度见表3和图1。
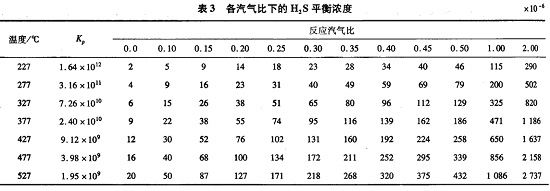
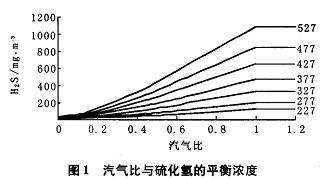
中变催化剂的产品说明书都有耐硫指标,一般在400mg/m3左右,但都无相对应的汽气比要求。从表3及图1中可见,H2S与汽气比关系很大,当汽气比小于0.5时其平衡的H2S急剧减少。国内催化剂的硫中毒(或耐硫)指标都是在某一汽气比下才有意义。目前企业或行业标准的活性检测的汽气比为1.0或2.0,测试温度为300℃。从表1可知其硫平衡值为300×10-6~700×10-6,即455~1 000mg/m3,活性检测时耐400 mg/m3硫是没有问题的,因此,这种耐硫指标对实际应用是没有意义的。有的中变催化剂即使在活性检测时能耐高硫,其实也是暂时的,当然有的催化剂添加了别的活性组分,如MoS2那就另当别论了。
2.2.5 实际工况下的硫中毒
大部分有机硫化物在CO变换反应过程中很快转化为H2S。COS和CS2接近于全部转化为H2S。
COS+H2→CO+H2S,△H0298=9.2kJ/mol
COS+H2O→CO2+H2S
△H0298=-34.7 kJ/mol
CS2+2H2O→CO2+2H2S
△H0298=-60.4 kJ/mol
硫含量一般是对总硫而言,H2S在平衡线上下大幅度波动是危险的,催化剂会在Fe3O4和FeS之间反复相变而破碎。随着反应的进行,床层汽气比逐步下降,其平衡状态下的H2S含量也随之下降,即抗硫性能随之下降,出现下部催化剂硫中毒,而上部催化剂比较完好的现象。
2.2.6 各汽气比下安全操作的硫浓度
与其他催化剂类似,由于H2S在催化剂表面发生化学吸附,尽管浓度还不足以使催化剂生成FeS,但催化剂活性却已下降。因此,实际上引起中毒的H2S浓度应低于平衡的H2S浓度。此外,随着变换反应的进行,虽然温度逐步升高,但床层中的汽气比却愈来愈低,有机硫转化为无机硫愈来愈多,H2含量愈来愈高,其相应允许的最高H2S含量也愈来愈少,即耐硫性能愈来愈差。由于缺乏各种铁铬变换催化剂的最高H2S中毒实验数据,按传统的经验方法取平衡温矩50℃。其在各汽气比下的操作安全总S浓度见表4。
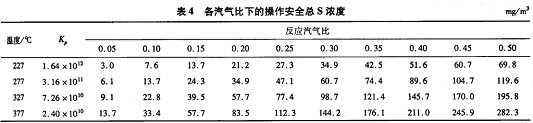
2.2.7 中低低工艺中最高耐硫含量
目前,中低低工艺出口CO体积分数为1.5%,中变催化剂的入口温度约为300℃,汽气比约为0.45,则总硫应为≤50×10-6,即≤76mg/m3。此值相当于变换气H2S浓度≤60 mg/m3,显然不是所有的用户都能够达到的。
当流程设置不合理,半水煤气的CO较低,中变催化剂入口汽气比约为0.35,则总硫应为≤38×10-6,即≤57 mg/m3。此值相当于变换气H2S浓度≤44mg/m3,显然大多数用户都难以达到。
当采用联醇工艺时,出口CO体积分数为7%~5%,中变催化剂入口汽气比约为0.30,则总硫应为≤30×10-6,即≤45 mg/m3。此值相当于变换气H2S浓度≤36 mg/m3。当流程设置不合理,进中变的汽气比更低时,总硫则更低,这对半水煤气脱硫来讲是难以达到的,而且与后续的耐硫低变催化剂的需S工况相矛盾。
针对铁铬催化剂的过度还原,国外所开发的低汽气比铁铬催化剂,其核心是从动力学上阻止或降低Fe3O4与CO过度还原反应的速度,低汽气比一般≥0.8。对于铁铬催化剂S中毒问题国外很少报道,在此情况下一般都采用全低变工艺或在高汽气(≥1.0)下采用中串低工艺。
综上所述,中变催化剂在含硫气体及低汽气比下会发生的“过度还原”,而硫的存在避免了费托反应。从某种意义上讲,无硫气体的低汽气比会引起费托反应,使变换反应难以进行,而含硫又确保了低汽气比操作的可能性。但是“不高不低”的硫含量不仅会导致催化剂活性下降,而且会使催化剂的强度受到严重影响,使床层阻力上升,甚至使破碎的粉尘带入低变段,造成低变催化剂的失活,影响正常生产。解决的办法是使反应离开FeS被H2O氧化的平衡线,以免在Fe3O4和FeS之间反复相变而破碎。对于低汽气比下的硫中毒解决办法同样如此。
2.2.8 在Fe3O4活性相操作
在流程的设置上,采用高汽气比的变换工艺,如出口CO≤0.3%的甲烷化净化或脱碳(如MDEA)可以避免催化剂的过度还原问题。为防止硫中毒,可根据本文提供的安全操作的S浓度指标进行半水煤气脱硫,使总硫降至所要求的浓度指标,以确保在Fe3O4活性相操作。
2.2.9 在FeS活性相操作
为保持中变催化剂的强度,防止工况波动而引起反复相变导致催化剂破碎,建议提高总硫含量,远离平衡线(高于平衡线温度50℃),以稳定的FeS作中变催化剂活性相,但要增加催化剂的用量1倍左右。对于变换出口CO体积分数的1.5%的中低低工艺,中变入口汽气比为0.45,则总硫应≥200mg/m3;对于变换出口CO体积分数约5%的中低低联醇工艺,中变入口汽气比为0.35,则总硫应≥150mg/m3。
有的工厂长期使用高硫煤,变换总硫相当高,而催化剂的寿命却不短,其理由就在于此。从中低低工艺到所谓的“中中低低工艺”,实际上就是增加中变催化剂的用量,其效果也在于此。值得注意的是变换工况一定要稳定,汽气比及总硫波动会使反应Fe3O4+3H2S+H2→3FeS+4H2O反复进行,严重影响催化剂强度。
2.3 蒸汽用量过大导致阻力增加
有人以吨氨消耗蒸汽800 kg和300 kg作对比进行了计算,以产氨5 t/h计,则每小时多耗蒸汽2.5t。以标准流量计,每小时系统体积增加3111m3,相当于在15 000m3/h流量的基础上增加了20%以上的体积,因此将会明显增加系统的阻力。当中变氧含量跑高时,生产操作上习惯采用加大蒸汽用量的办法以压低温度。随着中变催化剂使用时间的延长,其活性不断衰退,此时为了保证工艺指标,一般采用提高中变进口温度和加大蒸汽用量的办法,易造成工况恶性循环。
2.4 投资问题
(1)投资省(均以工业实施当时的价格计)以丹阳化肥厂为例,若使用中变串低变工艺需投资350万元,而同等能力的全低变工艺仅需投资200万元,节省150万元。
(2)维修费用低 全低变工艺不仅反应温度低,所需换热面积小,而且CO-MO系催化剂活性高、寿命长,所需更换催化剂数量较少,故维修费用比中串低工艺低得多。
(3)运行费用低 淮阴县化肥厂是年产2万t氨的小厂,年产化肥8.4万t。与中串低工艺相比,全低变工艺在以下方面具有明显效益:①汽耗节约(0.911-0.484)40×2=3.416(万元);②阻力降低,吨氨节电8 kW·h,电以0.15元/kW·h计,则全年节约2.4万元;③每年开车、停车10次,以每次节省时间10h计,增产化肥84 000×10×10/7 200=1 166(t);吨肥固定成本按100元计,利税30元计,1 166×130/10 000=15.16(万元);④省去1次脱硫后节省的电、氨、药剂等费用约8.0万元。
上述各项效益每年共计约60万元,管理较好的厂效益更加明显。丹阳化肥厂仅节约蒸汽一项半年的经济效益就可达到66万元之多。实施全低变工艺所取得的经济效益是十分显著的。
3 全低变工艺的优点
全低变工艺是将原中温变换系统热点温度降低100℃以上,从而非常有利于一氧化碳变换反应的平衡,实际吨氨蒸汽消耗量仅为250 kg左右,且热回收设备面积小。该工艺带来的效益是显而易见的,具体优点如下。
(1)原中变催化剂用量减少1/2以上,降低了床层阻力,提高了变换炉的设备能力。
(2)床层温度下降100~200℃,气体体积缩小25%,降低系统阻力,减少压缩机功率消耗。
(3)无费托副反应,杜绝了生成乙炔的反应,减少铜液的消耗,从而也防止了“带液”现象。
(4)换热面积减少1/2左右。
(5)从根本上解决了中变催化剂的粉化问题,改善了催化剂的装卸劳动卫生条件。
(6)提高了有机硫的转化能力,在相同操作条件和工况下全低变工艺比中串低或中低低工艺有机硫转化率提高5%。
(7)操作容易,启动快,增加了有效运行时间。
(8)降低了对变换炉的材质要求。
(9)催化剂使用寿命长,一般可使用5年左右,最长的已使用了12年;
(10)可放宽1次脱硫指标,从而降低了脱硫费用。
近年来开发的无饱和塔全低变流程的优点更为明显:从根本上杜绝了设备的腐蚀,减少因变换腐蚀而导致的停车,设备减少,系统的阻力降低,压缩机出力率提高,节省了原饱和塔循环热水泵的用电、热水排放的能耗,降低了对设备材质的要求。更重要的是提高了有机硫的转化能力。因为在传统的饱和热水塔工艺中,煤气中的各种有机硫通过循环热水溶解,再通过变换气释放出来,循环热水成为有机硫的‘绿色通道’。有些工厂变换气中存在较高的“非COS有机硫”的原因就在于此。无饱和塔流程可以解决这个问题,不仅精脱硫中的有机硫转化部分可以去掉,同时煤气中非COS有机硫(常用的水解方法难以脱除)也不会串到后工段,对甲醇或合成催化剂是极为有利的。
