1 前言
水是生命的源泉,地球与其它星球之区别就在于地球上有水,依靠水的支持由低级生物进化到有高度文明的人类。人类创造了文明,进而人类享受文明创造的财富和美好环境,但是现代人过度的向地球索取,奢侈地用水和污染水,使水资源承载巨大的压力。水资源逐渐枯竭,最终人类会被自己创造的文明毁灭。氮肥工业为重点污染行业之一,是化工行业中主要排污大户,其废水排放量占全国废水排放量的10%左右,治理势在必行,这就是推广应用氮肥生产污水零排放技术从而实现氮肥生产污水零排放的意义所在。
2 氮肥生产环境现状
我国氮肥工业2006年生产合成氨4937.9万吨,氮肥3440万吨(折纯N),其中尿素4578.6万吨(实物量),氮肥产量和尿素产量均居世界第一位,在我国农业发展中发挥了重要作用。我国煤制合成氨占合成氨总产量的76%,这些装置的中间产品是合成氨,以氨加工碳铵、尿素,也有部分联产甲醇。
以年产10万吨合成氨、2万吨甲醇的氮肥生产装置为例,其主要产品为尿素、碳铵、甲醇,工艺流程及主要污染源情况如图一:
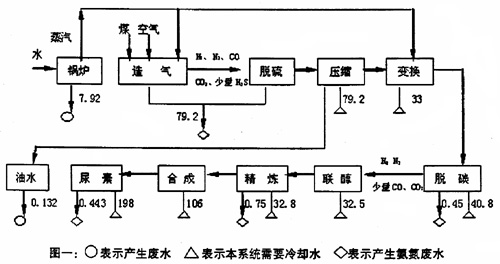
由图一看出,每生产1吨氨,需要冷却水522.3吨,产生氨氮废水80.84吨,其它废水8.05吨。废水来自造气的洗涤塔和冲渣,含固量高、温度高、成份复杂;锅炉电站的除尘和冲渣;脱硫液稀氨水;碳化稀氨水;尿素废液污水;脱盐水工段树脂再生的废水;铜洗精炼稀氨水及含铜液废水;甲醇精馏残液;冷却水排放等。
3 治理技术方案
做好氮肥生产装置的废水治理,实现污水零排放,必须从源头抓起,首先要节约用水,冷却水循环使用,提高循环倍数;采用清洁生产工艺,从源头消除污染源,不产生污水;用先进方法治理污水,因地制宜做到零排放。
3.1 建立三水闭路循环,在循环中对污水中氨、氮、氰进行处理。
3.1.1造气脱硫污水闭路循环处理系统
造气脱硫污水是洗涤冷却煤气的洗涤水和,氨水脱硫排出的脱硫氨水,其主要污染物是煤粉、氰、氨氮等。
减少污水量,选用先进造气工艺,提高蒸汽分解率达到44%以上;回收煤气、吹风气显热和潜热,副产蒸汽,减少冷凝蒸汽和冷却煤气的冷却水量;洗涤水采用平流沉淀、微涡流澄清,使悬浮物降至40mg/l~50mg/l;加入磷酸镁使之与氨进行反应生成磷酸铵镁沉淀,污泥处理后做肥料使用;采用微电解法使氰化物、硫化物与铁屑进行电化反应,生成不溶物,沉淀除去。
脱硫工艺必须淘汰落后的氨水脱硫,采用栲胶脱硫,消除一个氨氮污染源;采用戈尔膜液体过滤器及程序控制系统,进行硫泡沫处理;采用连续熔硫技术,收集硫磺产品,达到悬浮液硫含量≤5ppm,液体循环使用。
3.1.2建立锅炉污水循环系统
锅炉污水是水洗锅炉烟气形成的,烟气经过脱硫处理后,经麻石水膜除尘器喷水除尘,再经混凝处理,两级沉淀,一级过滤,形成闭路循环。
两个闭路循环系统在循环过程中,因蒸发需补充水以维持平衡。两个闭路循环的补充水不需一次水,利用冷却水循环系统的部分循环水补充到造气脱硫污水循环系统,造气脱硫污水系统的循环水经过回收油后补充至锅炉污水循环系统。
3.1.3建立冷却水闭路循环系统
氮肥生产的反应过程中必须将反应气体加热到一定温度,在反应过程中产生大量的热量,如变换反应、甲醇合成反应、氨合成反应,都有大量反应热放出形成高温气体,而在气体净化、精制、分离过程中又要将高温气体(包括压缩气体产生的高温气体)冷却,因此要提高热回收利用率和减少冷却水用量。
冷却水的特点是水量大,如果冷却水直流排放,吨氨需要522吨水,因此要单独建立闭路循环系统。为了减少循环水量,首先必须革新工艺技术,多回收热气体的热量以降低工艺气体的温度,一般都应降至60℃~70℃,再用冷却水间接冷却,采用这一措施,可使冷却水减少30%左右。为了保护水质并提高冷却效果,采用高效换热冷却设备;对循环水进行阻垢缓蚀、杀菌、灭藻处理,如采用物理法离子棒水处理器,可以达到上述目的或加入无磷降解水质稳定剂。
循环冷却水在循环过程中,部分蒸发,需要补充水,最好采用软水,提高循环倍数,减少一次水用量。
3.2 采用先进生产工艺,消除污染源
治污必须从源头消除污染源,即尽量减少水的污染。在氮肥生产中除了上述的造气、锅炉、脱硫污染源外,还有两大污染源,一是铜洗精制原料气,它有大量稀氨水排放和铜氨液的跑冒滴漏;另一个污染源是尿素工艺冷凝液,它含有大量的尿素和氨。
3.2.1用醇烃化精制工艺取代铜洗精制工艺。
醇烃化工艺,即用甲醇化、烃化将原料中少量的CO、CO2先转化成甲醇,剩余的CO、CO2转化低碳烃类,使原料气中CO+CO2≤10ppm。
醇烃化工艺获得了国家科技进步二等奖,是国家重点环境保护实用技术A类项目。
醇烃化的反应式如下:
醇化:CO+2H2=CH3OH
CO2+3H2=CH3OH+H2O
烃化:(2n+1)H2+nCO→4CnH(2n+2)+nH2O
2nH2+nCO→CnH2n+nH2O
2nH2+nCO→CnH(2n+2)O+(n-1)H2O
(3n+1)H2+nCO2→CnH(2n+2)+2nH2O
醇烃化工艺流程图如图二:
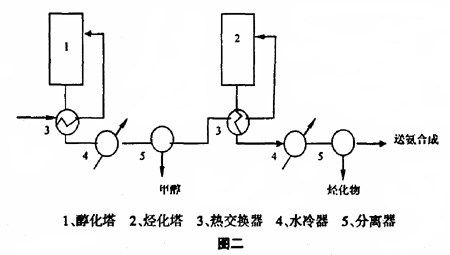
原料气预热后进醇化塔反应,反应后热气经冷却换热、水冷,甲醇冷凝为液体分离,分离后气体含有~0.1%的CO、CO2,经预热,进行烃化反应,反应后气体经换热冷却冷凝,分离出烃化物,出系统气体中CO+CO2<10ppm,送氨合成。
由图二可以看出,醇烃化工艺有甲醇和烃化物生成,这两种都是可利用的化工原料和燃料,能产生显著的经济效益。
3.2.2 尿素工艺冷凝液深度水解
尿素生产中,按反应式2个NH3与—个CO2反应生成—个尿素(NH2)2CO和—个水,每生产一吨尿素理论生成300kg水,加上蒸汽及冲洗水,约为350kg~400kg,形成含有大量NH3和(NH2)2CO的冷凝液。国内许多尿素生产装置只经过简单的解吸,其排出液含NH3量仍达到6000ppm~10000ppm,含尿素1.0%~2.0%,排放后严重污染环境。
用解吸深度水解法,经水解后,废液即成为精制水,含氨≤5ppm、尿素≤5ppm,可做锅炉给水。解吸深度水解法有中压法和低压法,图三为低压法工艺流程:
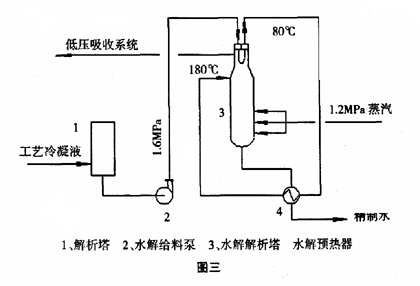
该法包括一个解吸塔(可用原塔)、一个水解解吸塔(操作压力为1.05~1.15MPa,温度170~190℃)和一台水解给料泵,处理后废液中氨和尿素分别为3~5ppm,做为精制锅炉给水。
3.3 终端处理
3.3.1 围堰和事故池
通过源头治理并实现了两个污水闭路循环和冷却水闭路循环之后,尚有一些分散的小股废水排放,如隔油后油水分离器排水、水封排水、泄漏水、水处理系统排污水、锅炉排污水、地面冲洗水、生活洗涤水、检修和事故状态下排出的废液、废水,以及两个污水循环系统排出水,为此,根据工段的特点设置围堰和事故池,清浊分流,分级利用,雨污分流,雨水直接外排;污水与初期雨水均收集于事故池中,集中进行终端处理。
3.3.2气升式环流生物处理技术
气升式环流反应器是一种单位体积COD、氨氮负荷大,操作弹性大,抗冲击能力强、操作费用低的一种有效的生化法处理反应器,其工艺流程图如图四:
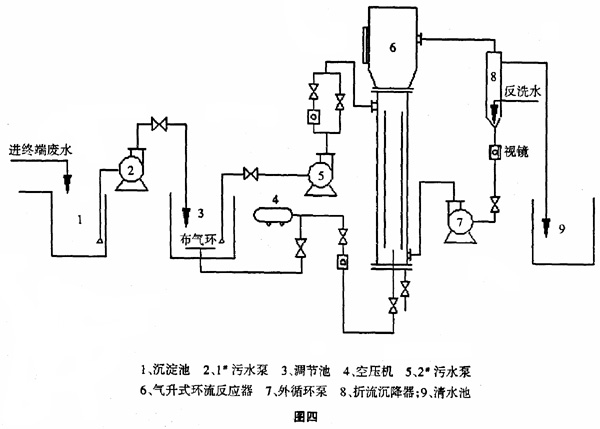
进入终端的废水由1#泵抽送到调节池,在调节池下布设一些曝气环,经过初步曝气后的废水由2#泵送入气升式环流反应器的上部,反应器的下部由空压机送入空气进行曝气,处理后的废水从上部自流进入折流沉降器中,沉降器中的清水部分溢流进入清水池,沉降器下部污泥用泵重新打入环流反应器中。
终端废水采用气升式环流反应器生物法处理,处理后的水质能达到《生活杂用水水质标准CJ/T48-1999》中城市绿化的水质要求(该标准的水质要求严于《合成氨工业水污染物排放标准GB13458—2001》中的一级排放标准,同时也严于《污水综合排放标准GB8978-1996)中的一级标准)。
3.4 水平衡
经过上述的处理,氮肥生产中补充新鲜水大为减少,吨氨废水排放量控制在2t以下,基本不向外排废水。按年产10万吨合成氨、2万吨甲醇的装置进行水平衡,补充新鲜水为172.1t/h,即吨氨补充新鲜水为11.36吨,其中循环过程蒸发水为101.6吨/h,生产过程化学反应消耗水为48.2t/h,冲渣带走水4.4t/h,经终端处理后的排放水(不含污染物)17.9t/h(1.18t/tNH3)可再生回用,基本上实现氮肥生产污水零排放。
4 应用情况
2003年,在中国氮肥工业协会的组织下,我公司组织技术人员深入企业进行了大量的调查研究和可行性论证,充分利用公司的技术优势,仅用4个月时间完成了技术先进、成熟、可靠的《氮肥生产污水零排放综合治理环保工程通用设计》的编制工作,同年年底该套通用设计通过了国家环保总局领导和专家的审查,得到了高度评价,建议在氮肥行业大力推广应用。
2004年至2006年纳入中央环境保护专项资金支持的29家氮肥企业,有25家采用了通用设计,2005年纳入国家发改委国债支持的淮河流域项目的22家氮肥企业全部采用了通用设计。47家氮肥企业通过实施污水零排放项目,取得了巨大的环保效益,每年减少一次水用量13065万吨,减少废水排放11437万吨,其中减排COD1.3万吨、SS9900吨、氨氮1.3万吨、氰化物118吨、硫化物158吨、石油类698吨、挥发酚34吨。
至今为止,我公司已为近80家氮肥企业提供了环保技术咨询,将通用设计与企业的具体情况相结合,坚持通用化的同时突出个性化,一厂一设计,厂厂各不同。今年召开的全国氮肥工业环保工作经验交流会参观的河南心连心化肥有限公司和石家庄正元化肥有限公司两个现场,均按通用设计实施,得到了环保总局和各级政府的认可,是实施污水零排放技术的示范。下面介绍几家企业在实施通用设计中的具体的做法。
实例一:河南心连心化工有限公司
①采用醇烃化精制工艺,砍掉传统的铜洗工艺
原合成氨生产系统原料其精致采用的是传统铜洗工艺,在铜洗再生过程中,产生解析废气,需用软水吸收产生稀氨水(年约3万吨),利用价值低并污染环境。2003年大胆采用湖南安淳公司技术,利用原Ф1000合成系统的主要设备,成功改造成为“醇烃化”工艺,取代了铜洗,根本解决了合成氨原料气净化精制系统NH3-N污染问题。年削减NH3-N总量65吨,副产甲醇,取得了经济与环境双赢的好成效。
②改造脱盐水工段,提高出水率,减少排放
原锅炉给水采用的是离子交换工艺,需要盐酸和烧碱对树脂进行再生,再生时排出酸、碱废液(约10m3/h)腐蚀性强,必须加碱、酸中和,中和后废液COD高达650mg/l,直接排放对水体污染严重。采用反渗透膜分离技术取代原有的离子交换工艺,该技术属无相变物理方法制取纯水,不用化学药剂和酸碱再生处理,所排浓水没有污染,可直接排放。该项改造每年可减少COD排放量约25吨,环境效益明显。
③完善造气废水处理,优化造气工艺,实现零排放
在稳定造气工艺的基础上,把微涡流塔板澄清技术应用干造气污水治理,提高水的重复利用率(99%以上)。与此同时把好入炉原料关,逐步进行炉体结构技术改造,稳定优化工况条件,提高蒸汽分解率,减少冷凝液富余带入造气循环水系统,攻克了造气污水闭路困难的技术难题。
④采用中压深度水解解吸新工艺,回收尿素、氨,实现氨氮零排放
由于尿素解吸液超标排放造成了排污水中NH3—N严重超标,为解决这一问题,结合本工司的工艺现状,对解吸液中的尿素、NH3-N采用深度水解、解吸技术,投入运行后,尿素解吸液中尿素、NH3—N的含量由改造前的1%、0.07%分别降至5ppm、15ppm以下,同时年回收尿素1000余吨,价值15万元,取得了理想的经济效益和环境效益。
⑤处理甲醇精馏残液
甲醇生产中精馏塔底部排放的残液,每生产1吨精醇产生300~500kg,其中COD含量高达10000mg/l,若直接排放,对水体污染严重。因公司污水终端处理采用生化技术,C/N比失调,影响处理效果,降甲醇残液送至终端处理系统,既稳定了微生物的生存条件,化害为利,又保证了处理效果。
⑥建立事故排放池,建立废水清浊分流、分级使用网络
压缩各段排油水(3m3/h、COD3000mg/l、NH3-N620mg/l)经隔油分离后直接送电站锅炉煤场喷洒煤灰使用;各主要工段与污水终端处理站建立污染事故排放池,正常高浓度工艺冷凝液与事故性排放全部排至岗位事故池,然后由管道逐渐送终端处理或作为造气循环冷却水补充水;生产区域所有地沟仅为清水排放和雨季使用;停车检修、冲塔清洗、清池置换的大量排污直接排入污水终端处的事故池,缓慢定量连续处理。
实例二:石家庄正元化肥有限公司
①改造造气废水处理系统,实现闭路循环
造气循环水分为两级循环,洗气塔分为两段,下段为除尘段,上段为降温段,除尘段由一级循环水供给,主要洗去半水煤气中的灰尘,控制下段洗气塔半水煤气出口温度,除尘后污水经沉淀池沉淀后,入热水池,由热水泵送入除尘段顶部;降温段由二级循环水供给,降温后热水入热水池,由热水泵送入凉水塔降温,再由凉水泵加压供降温段使用。本技术的关键是半水煤气中的饱和水在除尘段不冷凝,同时除尘水部分蒸发,该部分水在降温段以蒸汽冷凝液的形式随降温水冷凝,十二级降温水不断涨水,自其中取走富余水(水质接近蒸汽冷凝液)入终端处理,保证了造气循环水亏水,处于水平衡状态。除尘段补水由脱硫循环水补入,保证了脱硫循环水的置换,处于清水状态,同时由于控制了洗气塔除尘段温度,除尘段水随半水煤气带入降温段,将水取走,保证了其他工段的污水补入。
②清浊分流、分级使用
造气工段油冷却器、罗茨风机油冷、甲醇循环机油冷却器水为一次水,冷却后的水进入一次水池进行回收利用。
变换工段热水塔排放水、冷却器排放水,排入甲醇循环水作为补水。
甲醇水洗塔排放水、油进行回收,水排入锅炉循环水作为补水。
甲醇、合成、尿素、精馏、脱碳循环水均设有循环水旁滤器进行过滤,其反洗水为减少二次污染,均通过封闭管道直接排入终端池进行终端处理。
提H2岗位浓氨水经蒸氨后的残液(含极微量氨),带压送饱和热水塔作为补水,即得到了充分应用,由调节了饱和热水的PH值,有利于饱和塔的防腐。
③尿素解吸废液增浓回收
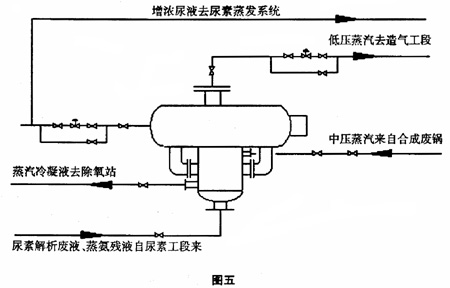
如图五所示的增浓装置,来自尿素工段的解吸废液,送入解吸废液增浓装置,利用合成废锅生产的0.5~0.8Mpa低压蒸汽进行加热增浓,产生的低压蒸汽通过压力调节阀送造气系统制取半水煤气,蒸汽冷凝液送除氧站回收利用;解吸废液经加热蒸发后,浓度不断增加,尿素含量达到20%左右,送尿素蒸发系统进行回收尿素。通过本装置的回收,一方面回收低压蒸汽,同时回收了尿素,闭路循环,不排放,实现了零排放。
④终端处理
经过前端的源头治理和水的梯级利用,到达终端的只有冷却水循环系统的置换水,由于循环水系统补入的是反渗透脱盐水,大大提高了循环倍数,置换水量少,终端也只用简单的处理。各循环水经旁滤器反洗水进入终端池,经集水池稳质后加药絮凝沉降进入清水池,由清水泵经过滤器送入合成、甲醇系统作为循环水补水。若锅炉造气水亏水可取部分甲醇循环水作为锅炉循环水补水,可以降低整套循环水钙镁离子、氯离子。
实例三:张家港市华源化工有限公司
该公司的搬迁技改项目15万吨/年合成氨、50万吨/年复合肥、15万吨/年尿素均为新建,区内还有热电工程。该项目在具备“三同时”的条件下于2005年10月投入运行,效果显著,在环保方面突出的做法是:
①选用先进、可靠的清洁生产工艺技术,源头把关,杜绝污染
合成氨流程:以白煤、水蒸气为原料,采用固定床造气、半水煤气栲胶脱硫、经中低低变换、DDS脱硫、MEDA脱碳、醇烃化精制,最后进入氨合成;尿素生产采用二氧化碳汽提工艺,尿素工艺废水采用深度水解,回收氨,处理后水中氨和尿素的浓度为10mg/l,不含其他杂质,可作为软水回用于锅炉。
②清浊分流、雨污分流、一水多用
厂区内规划建设了排水管网,清水排入护漕港再入长江;建立了污水终端处理系统(污水处理站),污水排放口安装了监测仪器。
设置专用的一次水净水站,对一次水进行净化处理,净水站的反冲洗水,主要污染物位SS和COD,送入污水处理站调节池与其它废水混合,一并处理。
每个生产单元设置不同类型、规格的围堰和事故池,排污水、冲洗水、初期雨水等收集后统一送污水处理站调节池。
③造气废水循环处理
造气循环水系统除设立常规的平流沉淀池和斜管沉淀池外,还设置了横流式混流生物塔,处理氰化物、硫化物、挥发酚等有毒有害物质,该生物塔式处理造气废水的新技术,处理效果好。
5 结语
氮肥生产污水零排放技术已在氮肥行业取得了成功应用,其环境保护和节能降耗效果显著。国内现有的氮肥企业生产装置规模、技术、管理水平参差不齐,各企业应根据实际情况,有的放矢地选择切实可行的工艺技术进行环境治理,搞好清洁生产,走循环经济之路,实现企业可持续发展。作为设计单位和技术拥有单位,我们将一如既往的为氮肥行业的进步和企业的发展而提供优质服务。
