0 前言
双甲(即甲醇化和甲烷化)工艺是一项取代传统铜洗、深度低变-甲烷化工艺的环保节能和实现合成氨清洁生产的新技术。在双甲工艺实践运行了近10年的基础上,湖南安淳高新技术有限公司于2001年又开发了醇烃化工艺,该技术是双甲的扩展和提升技术。
双甲工艺和醇烃化工艺,醇化部分是一样的,只是醇烃化工艺中以烃化(实质上是醇烃化)代替了双甲工艺中的甲烷化,在许多方面,大大优于第1代双甲工艺技术,得到了迅速推广应用。醇烃化工艺的优越性主要表现在其消耗的更低。本文就烃化和烷化工艺的气耗及热量消耗,通过物料热量衡算,进行分析比较。
1 气耗
气耗这里是指有效气体H2的消耗。
1.1 烃化反应的气耗
烃化反应是在铜铁系催化剂作用下主要进行醇化和烃化反应:
CO+2H2=CH3OH (1)
CO2+3H2=CH3OH+H2O (2)
nCO+(2n+1)H2=CnH(2n+2)+nH2O (3)
nCO+2nH2=CnH2n+nH2O (4)
nCO2+(3n+1)H2=CnH(2n+2)+2nH2O (5)
上述反应式中,可取n=4,并只用反应(1),(2),(4)和(5)进行简化计算,这样式(4)和(5)变为:
4CO+8H2=C4H8+4H2O (6)
4CO2+13H2=C4H10+8H2O (7)
当进入烃化系统的醇后气中CO体积分数为0.15%和CO2体积分数为0.08%时,按氨生产能力为100kt/a的精制气气量计,即进入烃化总气量为41990m3/h(标态),其中CO为62.985 m3/h(标态),CO2为33.59 m3/h(标态)。CO按式(1)反应掉60%,按(6)反应掉40%,CO2按式(2)反应掉40%,按式(7)反应掉60%。计算得:
式(1)耗H2为:
2×62.985×60%=75.582m3/h(标态);
式(2)耗H2为:
3×33.592×40%=40.310m3/h(标态);
式(6)耗H2为:
8/4×62.985×40%=50.388 m3/h(标态);
式(7)耗H2为:
13/4×33.592×60%=65.504 m3/h(标态)。
共耗H2为231.785 m3/h(标态)。以吨氨消耗H2 2220m3(标态)计算,则相当于少生产合成氨0.1044 t/h(751.7 t/a)。
同样,也可计算出副产物:式(1)和(2)共生成CH3OH 51.228m3/h(标态);式(6)和(7)共生成烃类物11.337 m3/h(标态);式(2),(6)和(7)共生成H2O 78.941 m3/h(标态)。醇烃混合物约165.4 kg/h,成分(质量分数)为:甲醇44.24%,水38.35%,其余为烃类物质。
根据多家应用企业的烃化分离物取样分析,液态分离物中40%~50%(质量分数)为甲醇、~30%(质量分数)为水,其余为杂醇、醚、烯烃类和烷烃类物质。上述计算基本与生产实践数据相符,只是没有计算杂醇、醚类等含氧生成物,故水含量计算值略高;并且,生成水量主要与CO2含量有关。
1.2 烷化反应的气耗
烷化(即甲烷化)反应是在镍系催化剂作用下进行,主要进行下列反应:
CO+3H2=CH4+H2O (8)
CO2+4H2=CH4+2H2O (9)
这(8),(9)反应式对比式(1),(2)和(6),(7):烃化反应中,1个CO分子和1个CO2分子分别消耗2个H2分子和3个多H2分子;而甲烷化反应中,1个CO分子和1个CO2分子则分别要消耗3个H2和4个H2分子。可简单看出烷化反应的耗H2较烃化多。
当进入烷化系统的醇后气中CO和CO2含量仍如1.1所述时,则从式(8)和(9)可计算出消耗的H2共为323.323 m3/h(标态),则相当于少产氨1048.6t/a。同时生成H2O为104.6 kg/h。
另外,甲烷化反应产物是气态CH4,要带入氨合成工序中,累积放空,还要损失H2。而烃化反应产物是水冷却后成液态的醇烃类物质,可作燃料或分离提取副产物,并在本工序即分离下来,不会带到合成氨工序。据烃化工艺使用企业反馈信息,现在已有公司收购其烃化物,从中提取杂醇、醚等多种精细化工产品。
2 热量消耗
虽然烃化和烷化反应都是放热反应,但由于进入烃化或烷化工序的CO和CO2量非常少,可根据反应热,进行热衡算。已有文献计算报道,每反应掉1%(体积分数)CO温升约72℃,反应掉1%(体积分数)CO2温升约59℃,所以总的温升只有15.52℃。而系统有热损失和水冷要带走热量,故这点反应热不足以维持烃化或烷化塔内反应的自热,必须引入工序外的高品位热量通过热交换来输入热量维持热平衡。这就有一个消耗补充热量(或称能量)的问题。下面用两种方法来计算补充热量的消耗量。
(1)烃化催化剂“零”米温度控制在220℃,入水冷的温度是69℃,将烃化塔和塔外热交换器作为一个封闭系统。烃化塔塔内热平衡示意图见图1。
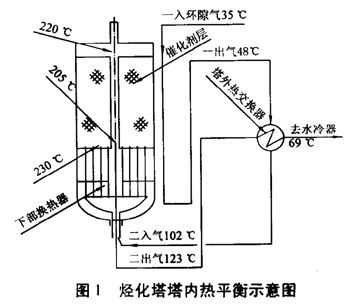
根据热平衡计算结果,电炉需提供205℃上升至220℃的热量Q:
Q=41990/22.4×32.651×(220-205)=918090.7(kJ/h)
即255 kW,相当于吨氨电耗18.35 kW·h。
(2)将烃化系统(不考虑氨冷器时)作为一个封闭系统,烃化系统热平衡示意图见图2。
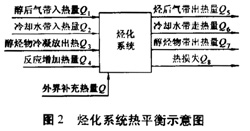
冷却水量120580 kg/h,换热后由24℃升到29℃;烃化物冷凝潜热按2010 kJ/kg计;反应热按218 kJ/mol计;烃后气量按41600 m3/h(标态)计;热损失约2%,作一个粗略的热衡算:
Q1=41990×1.53×35=2248564.5(kJ/h);
Q2=120580×4.186×24=12113949.1(kJ/h);
Q3=165.4×2010=332454(kJ/h);
Q4=218×(62.985+33.592)/22.4×1000=939901.2(kJ/h);
Q5=41600×1.42×35=2067520(kJ/h);
Q6=120580×4.186×29=14637688.5(kJ/h);
Q7=165.4×3.83×35=22171.9(kJ/h);
Q8=252135.7(kJ/h)。
进入此封闭烃化系统的热量:
Q入=Q1+Q2+Q3+Q4+Q补;
带出此封闭烃化系统的热量:
Q出=Q5+Q6+Q7+Q8=Q入;
故外界需向烃化系统补热量:
Q补=1344647.3 kJ/h。
若以电炉加热方式补充热量,则可折算成电炉功率373.5 kW,相当于吨氨耗电26.9 kW·h。
(3)上述计算是以烃化工艺并以电炉加热方式为例计算的,烷化工艺计算原始数据和计算结果略有差异。两种计算方法,结果也稍有差异。而生产实际情况,也大都在这两种计算结果之间。此外,烷化反应温度(-260℃)比烃化反应温度(~230℃)高,所以,烷化工艺对外界补充的能量,要求有更高的品位。
3 结语
根据上述计算分析可以看出,烃化的耗H2大大少于甲烷化,只有甲烷化的71.7%。另值得一提的是,随着对烃化工艺的副产物——醇烃混合物的处理回收技术的不断发展,醇烃混合物的应用前景将会越来越广阔,今后将不再单纯作燃料来处理了。
无论是烃化工艺还是烷化工艺,两者均不能实现自热,均需要消耗系统外补充热量(或者说补充能量)。从系统外补充热量的方式有多种,湖南安淳高新技术有限公司经过多年研究和工业实践,认为以利用塔内中心电炉直接加热最简单,以高温蒸汽间接加热次之,从氨合成二次出塔气或中变气取热最麻烦。
