1.0 前言
山东久泰科技有限公司是以生产甲醇、二甲醚为主要产品的大型化工能源企业。公司自主研发的“液相复合酸法催化脱水生产二甲醚”工艺,已获得国家专利,其工艺技术达到领先水平,现已形成了年产25万吨甲醇、15万吨二甲醚的生产能力,是目前世界上规模最大的二甲醚生产企业。一期工程年产8万吨甲醇、5万吨二甲醚于2003年12月建成投产,二期工程年产17万吨甲醇、10万吨二甲醚于2005年5月建成投产。其中8万吨/年甲醇装置的甲醇催化剂已连续运行4年2个月,甲醇催化剂装填量 24.6m3,甲醇总产量累计已达到36.5万吨甲醇,生产强度14837吨甲醇/m3催化剂,达到国内先进水平。本文就8万吨/年甲醇装置采用湖北省化学研究院精脱硫技术,保护甲醇催化剂的情况进行回顾和总结。
2.0 精脱硫工艺的选择
2.1 久泰公司甲醇生产造气采用固定床气化、部分变换和变压吸附脱碳、GC型轴径低压甲醇合成反应器。变换出口CO为23~26%,变压吸附脱碳出口CO2为3~6%。因CO变换率(~30%)低,导致变换气中COS含量高达30~50ppm,进变压吸附不仅会污染环境,还因CO2脱除率低而导致脱碳气中有机硫含量高,加重了脱碳后常温精脱硫的负荷。为脱除较高含量的有机硫,公司经过调研,决定采用由湖北化学研究院开发的在变换气中加设EH-2中温耐硫水解催化剂与脱碳后设置JTL-1“夹心饼”精脱硫工艺组成的单醇精脱硫技术。
2.1.1变换气中有机硫COS含量高达30~50ppm,进变压吸附后会将COS解吸到CO2气中污染环境,同时也会增加脱碳后常温精脱硫的负荷,故需要在变换过程中将大量COS降至最低。
2.1.2变换气中H2S、COS含量高, T504水解催化剂在较高温度下很容易发生硫酸盐化而失活,为避免硫酸盐化作用,必须在低于100℃下使用T504水解催化剂。
2.1.3变换气中高含量CO2的竞争吸附导致T504水解催化剂的转化率显著降低,需大幅增加T504催化剂的装填量,增加了经常运行费用。
2.1.4 EH-2中温耐硫水解催化剂不仅可以水解COS,而且对CS2也有较高的水解率。该产品已在河南安阳、新郑、山东鲁南、浙江巨化等多个甲醇厂使用,收到了良好的效果。故在变换后采用EH-2中温耐硫水工艺将COS、CS2进一步转化成H2S。
2.2 脱碳后的常温精脱硫选择了技术成熟的JTL-1常温精脱硫工艺,这是因为:
2.2.1 脱碳后还有较高含量有机硫COS。
2.2.2 T504水解催化剂活性好,COS转化率高,使用寿命长,运行成本低。
2.2.3 T703和T103脱硫精度高(H2S<0.03×10-6),反应速度快(空速1000~2000h-1),硫容大。
基于上述理由,8万吨/年低压甲醇合成,配套相关工艺为:

3.0 主要工艺指标
3.1 气体组成
变换气组分

变换气气量 27000Nm3/h
系统压力 0.7~0.8Mpa
脱碳气组分

脱碳气气量 25000Nm3/h
3.2 中温耐硫水解流程
侧流试验与其它几套中温耐硫水解工业运行表明,160~230℃EH-2中温耐硫水解催化剂使用效果最佳,如图1所示,在变换气与水煤气换热后的变换气中设中温耐硫水解炉。
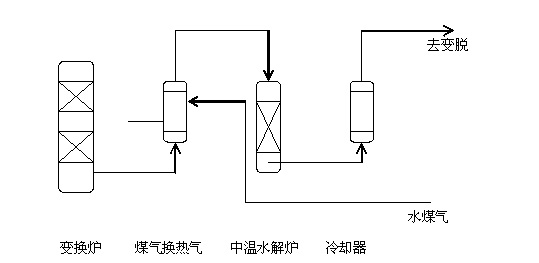
图1 中温水解工艺流程图
经过四年多的工业运行,取得满意的效果,有机硫转化率大于85%。
3.3 常温精脱硫工艺流程
脱碳后有机硫主要是COS,因此采用JTL-1常温精脱硫工艺。T504水解催化剂在60~90℃使用,为简化流程及设备投资,选择T103精脱硫剂,并将T103精脱硫剂与T504水解催化剂装在同一塔内。JTL-1精脱硫工艺流程如图2。
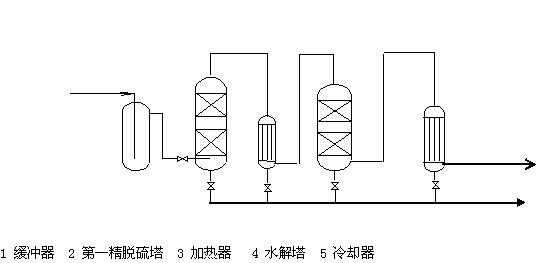
图2 JTL-1常温精脱硫新工艺流程图
4.0 精脱硫运行情况
常温精脱硫主要设备规格和精脱硫剂装填见表1。
表1 主要设备规格和精脱硫剂装填
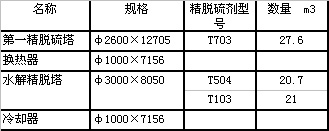
精脱硫装置2003年12月投入应用以来,运行稳定、操作简单,从表2中可以看出,四年多以来精脱硫后的总硫含量全部<0.1ppm。
表2 JTL-1工艺运行数据
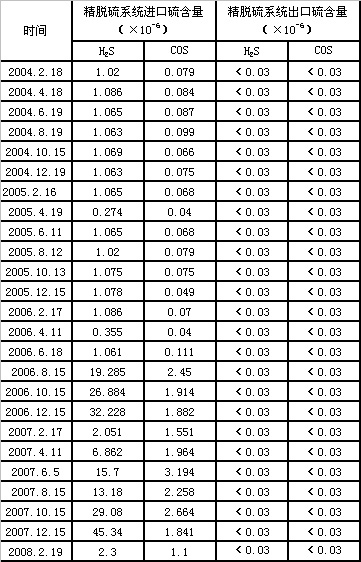
注:微量硫的最低检测限为0.03×10-6。
5.0 甲醇催化剂运行情况
开车初期合成催化剂低温活性较好, 190℃就能表现出相当好的活性,合成反应情况较好,合成塔热点温度指标确定235±5℃,因是新厂新人,炉温操作不熟练,导致合成炉温在10℃范围内波动。
运行一年后,员工操作水平有所提高,管理各方面也提高到一个新的高度,工艺管理、生产管理、设备管理制度全面落实到位,生产变的稳定有序,产量由以前满量240T/d提高到270T/d以上,最高班产达到276T/d。合成塔温度控制较好,波动范围稳定在3℃以内,合成新鲜气气体成份也无大的波动。
目前,随着各项管理的深入系统运行进一步优化,系统运行也变的更加稳定,变换出口CO成份波动范围0.5%以内,合成催化剂仍具有较高的活性,合成炉温波动在2℃范围内波动,系统压力波动仅为0.05Mpa内波动,但随运行时间加长及生产负荷提高,催化剂逐渐老化活性有所降低,合成催化剂温度由240℃提高到260℃,合成催化剂热点温度具体控制情况见表3。
四年多以来精脱硫后的总硫含量全部<0.1ppm,目前甲醇催化剂运行良好,预计保持目前工艺状况仍能再连续运行半年左右。
表3 合成催化剂热点温度
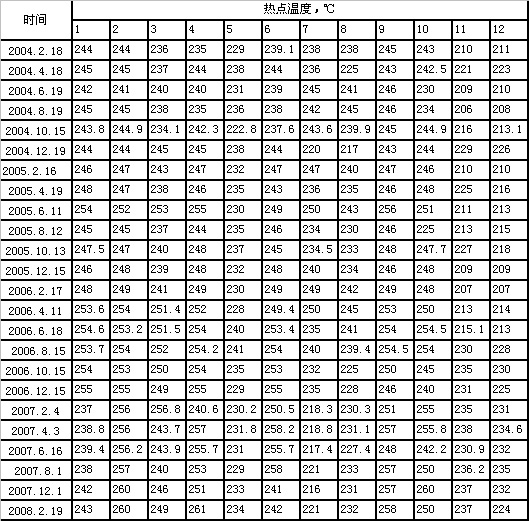
6.0 经济效益估算
通常在精脱硫保护下,甲醇催化剂使用寿命平均2年,久泰公司甲醇催化剂在精脱硫的严格把关下,加上精心操作和科学管理,其寿命超过了4年,等于少换了一炉催化剂,所产生的效益如下:
①少换一炉甲醇催化剂,节省费用约250万元。
②更换催化剂的时间约为7天,按每天产醇250吨,每吨纯利润800元计,产生的利润为140万元。
③更换催化剂开停车费用(含耗煤、电、水)约10万元。
减掉4年来更换精脱硫剂的费用50万元,实际产生的直接经济效益为350万元。
7.0 结语
久泰的甲醇生产表明:单醇厂在部分变换后加设EH-2中温耐硫水解催化剂,脱碳后采用常温精脱硫把关,可将总硫脱除至<0.1ppm,为甲醇催化剂稳定、长周期运行提供了有力保证。再加上优化的工艺配置和良好的管理水平,甲醇催化剂的使用寿命能够从2年左右提高到4~5年,经济效益显著。
参考文献
1 孔渝华等.EH-2中温耐硫水解催化剂的开发与甲醇中的精脱硫工艺.
2 张庆海,林祥权.《氮肥与甲醇》2007,(1).甲醇合成催化剂长寿命、高生产强度经验总结.
3 张清建,王先厚等.《氮肥与甲醇》2007,(3)常温精脱硫在醇烃化合成氨流程中的应用.
