0 前言
氨合成塔及系统是合成氨工业最重要最复杂的一个装置,其重要性是要将输入的合成气高效地转化为产品氨。在转化过程中,要求放空量少,有效气体利用率高;一次转化率高,循环量小,即氨净值高,系统压力低,阻力小;反应热利用率高,冷却水、冷冻量消耗少;在实际运行中,很难全部满足,正是如此,为更多的满足这些要求,要优化合成塔设计。综合氨合成反应理论和多年实践,根据不同工况,我们设计三种有特色的氨合成塔及系统,如低压低阻氨合成塔及系统、中压高产氨合成塔及系统、中压高净值氨合成系统已分别在山东华鲁恒升、河南心连心化工集团、山东鲁西化工集团投产,都取得很好的效果。本文着重阐述ⅢJDФ2200mm中压高净值氨合成系统。
1 mJDФ2200mm氨合成塔最适宜温度和设计温度曲线
氨合成是一个典型的放热可逆反应,其反应过程必须在平衡温度曲线下方进行。与平衡曲线相隔太近,反应温度高,则反应推动力小,反应需要时间长或催化剂用量大;与平衡曲线距离太远,温度低,则反应速度小,反应后氨含量低。考虑反应平衡和反应速度动力学两大影响因素,在理论上提出了最适宜温度曲线的概念,即在反应过程中,按最适温度曲线进行温度控制,其总反应速度最快,氨净值最高。实际上,不可能设计一个完全按最适宜温度曲线进行的反应器,只能设计一个接近最适宜温度曲线,或在最适宜温度两侧迂回进行的优化反应器。
ⅢJDФ2200mm氨合成塔正是按上述指导思想设计的。图1是ⅢJDФ2200mm的温度曲线,其中从上到下第一条是平衡曲线,第二条是最适宜温度曲线,第三条是设计(操作)曲线。
本设计的反应器“0”米即第一点a,就是未反应气进催化床层的工况:温度370℃,氨含量2.2%,经过绝热反应(ab斜线),即随着反应进行氨含量增加、温度上升至第二点b:温度488℃,氨含量达到10.2%。反应的第二个过程是间接降温(bc水平线)至第三点c:温度435℃,氨含量不变。第三个过程是第二次绝熟反应(cd斜线)至第四点山温度480℃,氨含量13.3%,第四个过程是反应和换热同时进行(de反斜线),即内冷反应段达到第五点e:温度425℃,氨含量16%,第五个过程是第三次绝热反应(ef斜线)达到第六点f,即反应终点:温度452℃,氨含量17.8%。
从增加氨净值观点分析高氨净值反应器设计。反应起点为a点,即“0”米点,由图可见“0”米温度低,进口氨含量低。低零米温度为第一段温升提供了区位,否则氨净值高,热点温度高,超出催化剂耐热值,因而限制净值提高。从“0”米开始绝热反应至b点,该点落在最适宜温度曲线上,这是最佳方案点。从图上看出,此点氨含量高(达10.2%),氨净值增加8%,增加量为总增量的49%。如果b点再往上移,即继续反应,温度继续升高,就会使催化剂受损,同时距离平衡越近,氨净值增加缓慢,推动力越小。反之,如果b点落在最适宜曲线的下侧,此时反应温度低,反应速度较小,反应后氨含量也低。所以b点落在最适宜温度曲线上是一个最佳点,在较短的催化床内,几乎完成50%的反应总任务,这是优化设计一个亮点。
其次,第一段反应得到高氨含量反应气,采用间接冷却方法,没有采用未反应冷气混合冷却,氨含量没有降低,保持了高氨含量,这是设计第二个优化点。
第三,通过间接冷却后,增设了第二绝热反应层,然后再串接内冷连续反应层。两者配合使反应基本上按最适宜温度指引方向在其两侧进行,因而保证了快速的反应,这是设计中第三个优化点。
最后,通过三段反应后反应气氨含量已达到16%,距离平衡较近,反应推动力比较小了,但工况点e仍在最适宜线的下侧,再绝热反应一次,使操作线穿过最适宜线,仍能保持快速反应。为此用较多的催化剂量做最后的“拚搏”,进行绝热反应,使氨含量增加1.8%左右,最终氨含量达到17.8%,这也是一个设计优化点。
2 合成塔结构及塔内流程描述
合成塔为三层四段,一段为轴向绝热段;二段包含两个段:内圈是径向绝热段,外圈是径向内冷段:三层即第四段,为径向绝热段。
一、二段间为间冷,换热器在第二层中心,三段由径向冷管束构成。第三段反应出来的热气,由上而下,经过第二层、第三层径向筐简体与内件简体间环隙,被经过塔外筒与内筒间环隙的由下而上的未反应气冷却。第四段反应后的热气经塔内下部换热器冷却出塔。
ⅢJDФ2200mm合成塔含二个列管式换热器和一个径向冷管束,两个列管换热器在二、三层中心,冷管束在二层的外圈。
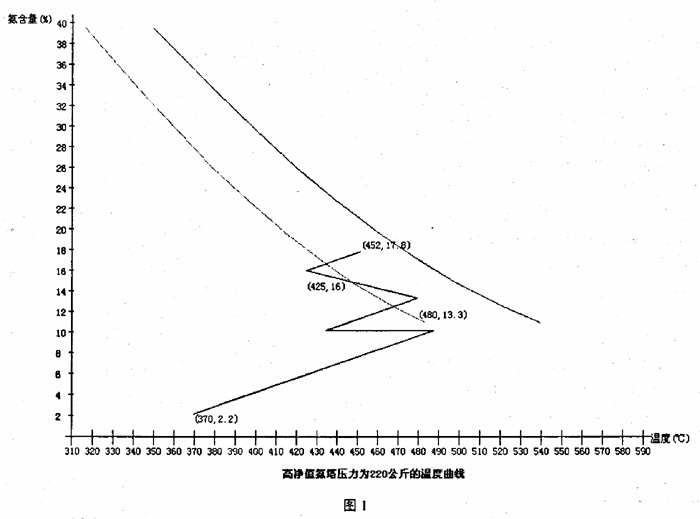
其次,第一段反应得到高氨含量反应气,采用间接冷却方法,没有采用未反应冷气混合冷却,氨含量没有降低,保持了高氨含量,这是设计第二个优化点。
第三,通过间接冷却后,增设了第二绝热反应层,然后再串接内冷连续反应层。两者配合使反应基本上按最适宜温度指引方向在其两侧进行,因而保证了快速的反应,这是设计中第三个优化点。
最后,通过三段反应后反应气氨含量已达到16%,距离平衡较近,反应推动力比较小了,但工况点e仍在最适宜线的下侧,再绝热反应一次,使操作线穿过最适宜线,仍能保持快速反应。为此用较多的催化剂量做最后的“拚搏”,进行绝热反应,使氨含量增加1.8%左右,最终氨含量达到17.8%,这也是一个设计优化点。
2 合成塔结构及塔内流程描述
合成塔为三层四段,一段为轴向绝热段;二段包含两个段:内圈是径向绝热段,外圈是径向内冷段:三层即第四段,为径向绝热段。
一、二段间为间冷,换热器在第二层中心,三段由径向冷管束构成。第三段反应出来的热气,由上而下,经过第二层、第三层径向筐简体与内件简体间环隙,被经过塔外筒与内筒间环隙的由下而上的未反应气冷却。第四段反应后的热气经塔内下部换热器冷却出塔。
ⅢJDФ2200mm合成塔含二个列管式换热器和一个径向冷管束,两个列管换热器在二、三层中心,冷管束在二层的外圈。
3 塔内气体流程(见图2)
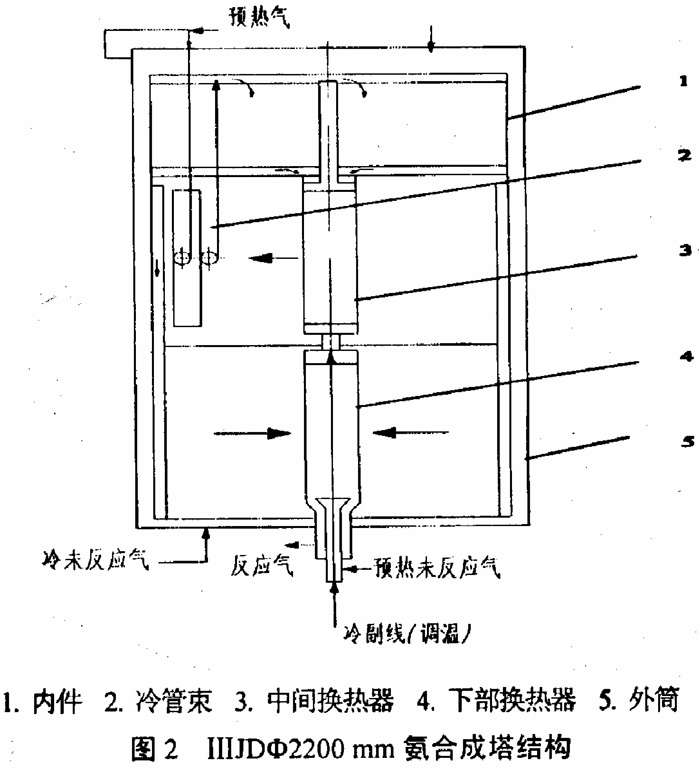
含氨2.2%未反应气分成两股,一股约70%~75%经塔外热交加热至200~230℃,50%~60%进入塔内下热交的管内,由下而上上升,再经塔内上热交(第二层中间),加热至360~370℃,经中心管到达催化床“0”米,与由冷管出来的40%~50%(370℃)未反应气混合,进入第一段反应,温升至488℃,氨含量增至10.20%,经过塔内上熟交管间冷却至435℃,进入第二段径向绝热反应,温度达到480℃,氨含量增至13.3%,径向进入内冷段反应,温度降至425℃,氨含量上升16%,然后进入第二、三层径向筐与内件内壁环隙,由上而下,进入第四段,径向绝热反应,温度上升至452℃,氨含量达到17.8%左右,再进入塔内下热交管间,被管内冷气冷至350℃左右出塔。
25%~30%未反应冷气由下进内外筒环隙,由下而上,与从热交出来已预热的10%~15%未反应气混合,再进入冷管,在冷管加热至360~370℃后,直接由上升管进入催化床“0”米。
4 系统流程(见图3)
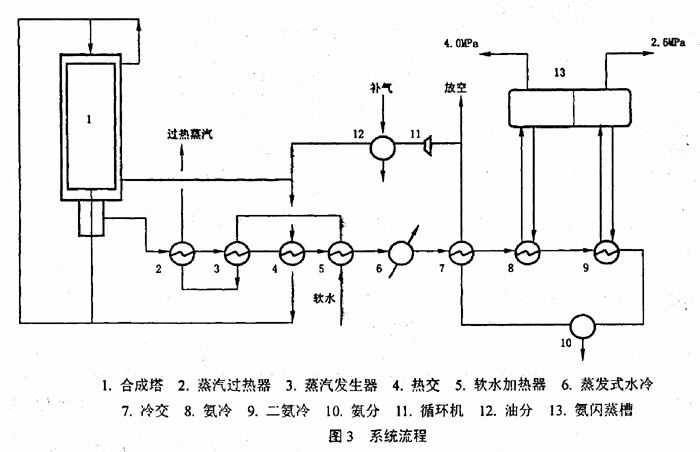
从合成塔(1)出来反应热气,氨含量17%左右,温度360~380℃,经蒸汽过热器(2),降温至360~340℃,经蒸汽发生器(3),产生2.5~3.9 MPa饱和蒸汽后,温度降220~260℃,进塔外热交(4)温度降至100~110℃,进入软水加热器(5)降温至60℃左右,进蒸发式水冷器(6),降温至40℃,经冷交(7),氨含量降至4.43%,进一氨冷(8)、二氨冷(9)降温至-11℃左右,进分离器(10)分离液氨后,氨含量为2.76%,进循环机(11)、油分(12)与补入新鲜气混合物,氨含量降至2.3%。混合气分两股:25%~30%进入合成塔环隙,70%~75%进塔外热交被加热至200~230℃,又分两股,一股进塔内下部换热器经第二层中间换热器至“0”米,另一股在塔顶与从环隙出来的气体混合后进塔内冷管束。两股进入中间换热器和冷管束的未反应气分别加热至360~370℃,在“0”米混合后,进入催化床层反应。
流程特点:
(1)反应气出塔温度高,达360~380℃,出塔气体反应热多级利用,并产生中压(2.5~3.9MPa)过热蒸汽(300~360~C),即出塔经过蒸汽过热器、蒸汽加热器、软水加热器,利用出塔气体热量将软水逐级加热最后产生过热蒸汽。软水加热器后,反应气降温至50~60℃,可采用风冷降温至40℃,达到节水的目的。
(2)采用两级氨冷:一级氨冷冷至3℃,二级氨冷降温至粉-11℃,氨含量可降2.76%,两级氨冷比一级氨冷,节约冷冻量40%以上。
(3)补气在氨冷之后:使进塔氨含量稀释至2.2%~2.3%,即系统只降温至-11℃就可使进塔氨含降至2.2%,对氨合成反应有利。
(4)放空点设置在循环机进口点,此处惰气浓度最高,系统中氨都已分离,氨含量最低,放空气量少,放空气中带走氨和有效气体少。
(5)设置20%未反应冷气经过内外筒环隙,使外筒处低温工况运行,安全可靠。
(6)未反应气三股分流进塔:20%从环隙,30%不经环隙,混合后形成50%进冷管,另外50%进塔内两个串接中间换热,系统阻力小。
5 应用
山东鲁西化工集团工业园采用ⅢJDФ2200 mm氨合成塔配套系统中,出塔反应热气没有设置蒸汽过热器,而用于加热甲烷化未反应冷气,废锅产生2.0MPa蒸汽,废锅后未设置软水加热器。该装置已于2007年6月13日在山东鲁西化工集团工业园投产,日产氨达820~830t,系统惰性气含量18%~20%,系统压力24.0~25.0MPa,出口氨含量15%~17%。
催化床层温度:
“0”米360℃,第一层出口475℃,第二层进口420~430℃,第二层热点450~460℃,第二层出口温度420~430℃,第三层山口温度440~450℃。
系统温度塔山温度365℃,废锅出口206℃,塔进192℃,热交出口88~C,水冷出口31℃,冷交出口12℃,一氨冷出口-3℃,二氨冷出口-6℃,冷交冷气出口29℃。
系统已经稳定运行4个月,产能达到250kt左右。
6 结论
ⅢJDФ2200 mm氨合成塔的设计,是以反应最适宜温度曲线为依据,优化反应器结构和参数,达到氨净值最大的目的。优化结果是反应结构为三层四段,各段之间采用间冷,进一段温度较低,一段出口温度高,充分利用反应初始状态推动人特点,适当提高第一催化层厚度,使之温升高、氨净值增加多,末端反应距离平衡状态近,以降低催化剂利用系数的方法,使终端氨含量尽量提高。按上述思维应配置低起活温度、高耐热温度即宽温催化剂,同时配置完善又便于操作的调节温度手段,本系统在鲁西化工集团工业园运行4个月,基本达到设计目标,即出口氨含量达到16.8%。目前正在为山西设计Ф2400mm氨合成系统,在Ф2200mm基础上进一步完善,估计效果更好。
