氯及其某些化合物不仅对环境能造成污染,而且在工业上是常见的催化剂及吸附剂的毒物。由于氯有很高的电子亲和力和迁移性,易与金属离子反应,且常随工艺流体向下迁移,造成催化剂的永久性中毒,并且往往是全床层性的。近年来,各油田为了提高原油的产量,广泛使用各种采油助剂,如破乳剂、清蜡剂、酸化剂等,其中不少采油助剂含有各种类型的有机氯化物,这些有机氯化物不溶于水,热稳定性好,很难用脱盐的方法脱除,大部分存在于常减压产品的直馏石脑油馏分。我国从20世纪70年代开始研究脱氯剂,目前气相脱氯技术已发展较成熟,然而液相脱氯技术进展缓慢,尤其是液相脱除有机氯技术还没有取得实质性的突破。本文将综述液相脱氯剂及技术进展。
1 液相脱氯
1.1 水相中的有机氯化物及其脱除
水相有机氯化物常存在于水源、地下水及土壤中,而且难以生物降解给环境带来了很大负面影响。处理的方法有催化(加氢催化,金属还原催化,光、电催化等)脱氯,物理、化学吸附法等。在工艺上Rushan Bie等利用焚烧法将废水中含氯有机物烧掉,再在流化床中脱掉氯化氢。Ikuo Ab等研究了活性炭吸附剂脱饮用水中的氯仿。前者工艺相对复杂;后者实施相对简单,但不能从根本上解除氯的危害。
1.1.1 金属单质及二元金属系还原脱有机氯
目前,零价金属还原脱氯降解含氯有机化合物是一个非常热点的研究领域。Gillham R W等在1994年就提出了零价铁脱氯技术。国内也有很多人做了这方面的研究。
何小娟、吴德礼、马鲁铭等和陈宜菲、周红艺、何志桥等均报导了这方面研究。该法可使用的原料有金属铁、二元金属(Pd/Fe,Ni/Fe,Cu/Fe等)、FeS2及Fe2O3等,所降解的有机物目前主要有四氯化碳(CT)、氯仿(CF)、六氯乙烷(HCA)、三氯乙烯(TCE)、四氯乙烯(PCE)、氯乙烯(VC)、多氯联苯(PCBS)、五氯苯酚(PCP)等。Luca Perrone等报导了在温和条件下用Pa/C催化剂加氢脱废水中三氯乙烯(TCE)中的氯。
金属单质及二元金属系还原脱氯是一种简单、有效、廉价处理方法,但该方法也存在一些诸如零价铁对一些氯化物还原脱氯活性较差,降解不完全;零价铁表层容易形成惰性层,阻碍电子的有效传递,使得零价铁的反应性能大大降低等缺点。对二元金属系催化剂来讲,其处理效果虽然相对较好,但Pd和Ni等为贵金属元素,价格昂贵,使用起来有局限性。目前这类方法都还处在实验研究阶段,未见工业应用报道。
1.1.2 电催化法和光催化法
杨波、余刚等以Pd修饰Ti电极,对水相中2,4,5-PCB还原脱氯进行了研究,找到了优化的操作条件。
Sonoyama等报导了用银电极电解水溶液中的氯仿可使其降解为甲烷,但由于氯仿在水中的溶解低使得电流密度很小,如果使用有机溶剂就会明显提高电流密度。因此,Hori和Nagahiro Hoshi等很多学者研究了有机相中电解脱除有机氯及机理。郑璐、朱承驻等用石墨电极电解苯酚稀水溶液并研究了脱氯机理。
在光催化方面,罗仲宽等进行了利用二氧化钛溶胶进行光催化降解氯代甲烷水溶液的研究,并得出了随着氯取代度的增加脱氯效果依次降低的结论。MogyorosiK等用二氧化钛纳米粒子光催化水中的二氯酚。
1.2 水相中无机氯及余氯的脱除
水相中脱除无机氯和余氯主要出现在水处理工艺过程中,常见的是用活性炭和化学药剂处理。如在以Cl 2消毒的水中含有水解产物HclO,OCI—及氮化物NHCl2,NHCl2,R2NCI等,常用硫(1V)化合物脱氯,HelzRG等对此做了详细研究。在动力学方面黄翔峰、吴志超等研究了硫代硫酸钠脱除余氯的特性及动力学。
1.3 有机液相中脱氯
有机液相中含的氯主要是卤代烷烃和卤代芳烃及催化加氢后含有的HCl,脱除方法也不一样。
1.3.1 有机液相中卤代烷烃和芳烃的加氢催化脱氯(HDC)
液相催化加氢脱含氯有机废液被认为是最有发展前景的方法之一。国内外很多人都做了相关研究。报道较多的是Pd/AL2O3,Pt/AL2O3,Pd/C,Pt/C,Ni/C和Rh-Pt/C系催化剂催化加氢脱氯;但都还处在实验研究阶段。工业应用的也有Co-Mo催化剂。此过程中产生的氯化氢对催化剂有毒害,为此很多研究者以NaOH来脱除产生的HCI,还有不少学者研究了NaOH的加入对催化反应的影响情况。但是生成的NaCI在有些有机溶剂中不会溶解,会在催化剂上富集从而降低催化剂活性。Ukisu Y等以及夏传海等做了这方面的研究。也有研究者用KOH,CaO,Mgo,TiO2等来脱除HCI。另外,在工艺上国外有直接用活性白土脱除油中的氯化物;国内有些则先使有机液相气化,再在气-固相反应下催化加氢脱氯,其实质还是气相脱氯。
1.3.2 有机液相中HCI的脱除
从文献报导来看,目前主要是石脑油、轻质液态烃、液化石油气及混合二甲苯中脱除HCl。当前液相工业脱氯的研究主要集中在这方面,其中西北化工研究院、湖北省化学研究院、南京化工大学等科研单位已开发了相应的脱氯剂。国外则在三四十年代就有用矾土催化加氢将液态烃中的有机氯转化成HCl再用CaO脱除的专利报导。
2 脱氯剂脱除无机氯原理
氯化物的脱除机理有吸附法和化学吸收法。由于吸附法净化度和氯容均受到一定限制,一般采用化学吸收法来脱除氯化物。
2.1 吸附法
研究液相吸附时,除了考虑吸附剂-溶剂之间的相互作用外,还必须考虑溶质-溶剂之间和吸附剂-溶剂之间的相互作用。在吸附剂-溶剂之间存在van der Waals力、静电力和氢键力。溶质是非极性分子时主要是van der Waals力。吸附剂-溶质之间的亲利力越大,吸附力就越强。吸附剂一般采用比表面较大的活性氧化铝、分子筛、活性炭等。大部分烷烃中自由氯化物可以用活性氧化铝等除去。活性氧化铝吸附HCI同样适用于液相,如石脑油等,但使用时要注意吸附剂在工业装置中的高径比越大约好,一般大于3,在压力降允许的情况下最好使用较小粒径,尤其在液相时。
2.2化学吸收法
待净化原料中的HCI和脱氯剂中的有效金属组分M进行反应,生成稳定的金属氯化物而被固定下来常见的有第1,2族中的金属元素。如原料液中有有机氯时可先催化加氢将其转变为HCl脱除掉。
Mn+ +nHCI-MCln
其中M为活性金属,n=1、2、3……
常见的有第1、2族中的金属元素。如原料液中有有机氯时可先催化加氢将其转变为HCI脱除掉。
3 国内外工业用液相脱氯剂
国外脱氯剂的开发和应用早于国内,目前国外脱氯剂牌号很多,主要有英国的ICI、德国的BASF、美国的UCI等公司的产品,但应用于液相脱氯的产品也不多。ICI59-3以氧化铝为载体,氧化钠为活性组分可用于天然气或石脑油脱氯:UCI公司的G32-W以活性炭为载体,铜铬为活性组分用于液态丙稀原料的脱氯。
国外除了工业化的脱氯剂外,近年来在拓宽脱氯剂的开发研究领域做了更进一步的:厂作,脱氯剂的活性组分研究已扩展到Fe2O3,K2O,Cu,Mn,Mg,V,Ni,NaOH,KOH,Na2O,Na2CO3等。
近年来,国内在石油化工领域广泛使用的液相脱氯剂主要是无机脱氯剂。国内无机脱氯剂的研究始于20世纪70年代,以取代进口为目的。用于液相脱氯的主要有T406,ET-1,NC—1等脱氯剂,但主要是脱液相中的HCI。
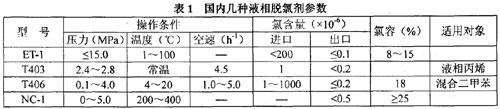
4 液相脱氯剂载体及活性研究
4.1 载体
据文献报导,液相脱氯剂载体研究较多的是氧化铝、活性炭、分子筛、硅藻土硅酸铝等。近来也有以二氧化硅、金属钛为载体的报导。由于氧化铝具有较大的比表面积(325m2/g),其孔道是高极性的,对极性分子有较大的吸附力,而HCl极性很强,因此在脱氯剂中使用较多的也是氧化铝。冯续在研究T406脱氯剂时发现:以活性炭为载体时氯容较高,而且对有机溶剂也很稳定;而使用氧化铝为载体时,在脱氯过程中有时会有少许副反应发生,由此确定了以活性炭为载体。但活性炭负载型脱氯剂的缺点是使用场合因活性炭的性能而受到限制。另外,特别值得注意的是液相有机原料一般是较好的溶剂,对很多物质可能有一定的溶解性,因此对载体与活性组分的选择就要尤为注意。
4.2 活性组分
从文献报导来看,活性组分主要是活性金属(第1,2主族)及碱土金属的氧化物、氢氧化物和碳酸盐。国内报导的有CaO,Ca(OH)2,CaCO3,Na2O,Na2CO3,MgO,ZnO等。国外液相脱氯活性组分还有Cu-Cr。日本有用CaCO3和CaO除甘油中氯。美国专利很早就报导直接以NaOH利CaO或CaCO3的混合物作为液相脱氯剂。CaO-ZnO型液相脱氯剂报导较多。
5 液相脱氯剂工业应用
5.1 液化石油气
尤留芳报导上海石化总厂芳烃厂采用T403型脱氯,在压力2.4~2.8MPa、常温、液相空速4.5h—1将含氯1×10—6液相丙稀脱至含氯<0.2×10—6。
秦南等报导研制出选择性强、吸附速率快、氯容高且具有防水功能的常温型脱氯剂,用于处于常温液态的石油气脱氯时可将氯化氢含量降至0.5×10—6。
5.2 混合二甲苯原料净化
冯续报导巴陵石化公司涤纶厂混合二甲苯分离装置装填脱氯剂2.5t,常温下可将二甲苯中65×10—6氯脱至0.2×10—6,氯容>18%。试验研究时,脱氯前、后氯的分析均采用硫氰酸汞比色法。
6 结语
目前,国内外在工业脱氯技术研究方面投入了较多力量,也取得了显著成效。但目前科研部门对液相有机氯的脱除还停留在实验室阶段,对液相脱氯动力学模型及机理的研究有待加强。对于当前液相脱氯来说,还存在以下问题:其适用对象较窄;使用中一般要求较大的高径和径径比,对动力要求大;活性物反应后离子易流失,结构发生变化导致强度发生变化;氯容不高等。因此开发廉价环保、氯容较高、性能稳定、低进口下仍有高脱除率的脱氯剂必将赢得市场。随着世界各国环境保护意识的加强,能源节约意识的树立,液相净化技术即面临挑战也迎来机遇。
