产能控制 “十三五”原则不新增
不少三聚氰胺企业在接受中国化工报记者采访时都表示,产能过剩是导致三聚氰胺行业陷入当前困境的主要原因。据中国氮肥工业协会统计,过去十几年,我国三聚氰胺产能年均增长率20%,2014年达240万吨,约占世界产能的70%,产量约占世界总产量的50%,是名副其实的世界最大三聚氰胺生产国。目前,全国三聚氰胺生产企业约22家,主要集中在四川、山东、河南、河北、山西、重庆、新疆等主要尿素生产地。国内产能最大的企业为四川金象赛瑞化工股份有限公司,年产能近30万吨,昊华骏化、山东舜天、山东鲁西年产能也都在10万吨以上,这4家企业的产能占全国总产能的30%左右。
在产能快速增长的同时,三聚氰胺的市场需求也增长迅速。2002~2014年,我国三聚氰胺年需求增长率约20%,成为世界三聚氰胺需求量增长最快的地区之一。2014年,我国三聚氰胺消费量约70万吨,约占全球消费量40%左右,已成为全球最大的三聚氰胺消费国。
然而,市场容量的增长始终不及供给,目前国内三聚氰胺生产企业的开工率在45%左右。中国氮肥工业协会理事长顾宗勤表示,国内产能严重过剩引发了三聚氰胺价格大战,企业之间竞相压价,市场价格跌跌不休。2012年,国内三聚氰胺价格在8000~8600元,2013年在8000元上下波动,2014年在5500~7700元。今年以来,三聚氰胺市场主流价格更是跌至5400~6100元。从而导致三聚氰胺行业效益逐年下降,有的企业甚至成本与价格倒挂。
即便如此,三聚氰胺行业扩能的脚步也没有停止。今年3月,新疆奎屯5万吨/年装置投产;9月新疆宜化的8万吨/年装置已投产,目前正在试运行阶段;明年3月份还将有河南心连心公司的6万吨新增产能投产。届时国内三聚氰胺产能将达到260万吨,产能过剩将更加严重。
在此情况下,控制产能成为行业的共识。顾宗勤强调,鉴于目前国内三聚氰胺行业的产能过剩现象,应积极进行供给侧管理,尽快建立行业准入和退出机制,出台相关规定,建立行业准入制度,严格限制低水平、重复性建设,对退出企业积极争取政府给予相应的政策扶持,实现行业的健康发展。
中国氮肥工业协会制定的《三聚氰胺行业“十三五”发展思路》(初稿)明确,目前国内有效年产能190万吨,预计今年产量95万吨,表观消费量75万吨。“十三五”时期,国内三聚氰胺消费量年均增速预计5%~8%。因此,“十三五”时期原则上不再新建三聚氰胺装置。坚持等量或减量置换的原则,通过置换、改造建成技术水平先进、上下游综合利用、年产能8万吨及以上的三聚氰胺企业10家左右,年产能5万吨及以上的企业10家左右,淘汰技术装备落后、生产成本高、没有竞争力的企业。产品质量达到国际先进水平,综合加工成本降低15%~20%。
11月17日,由中国氮肥工业协会主办的三聚氰胺绿色材料发展高层论坛暨2015年三聚氰胺行业工作会在北京举行。 图为会议现场。 (本报记者 庞利萍 摄)
11月17日,由中国氮肥工业协会主办的三聚氰胺绿色材料发展高层论坛暨2015年三聚氰胺行业工作会在北京举行。 图为会议现场。 (本报记者 庞利萍 摄)
创新技术 汰旧推新更上一层
据顾宗勤介绍,我国三聚氰胺生产技术的发展主要经历了以下几个阶段:第一阶段为上世纪70~80年代,主要以两步法为主,以常州曙光化工厂、天津卫津化工厂、山东宁阳化工厂等为代表,装置单线年产能规模500~1000吨。第二阶段为上世纪80~90年代,在两步法生产技术基础上,开发出了一步法气相淬冷法技术,以南京栖霞山树脂厂和山东宁阳化工厂为代表,装置单线年产能规模3000~6000吨。第三阶段为1992~2003年,清华大学开发出了第二代(改良)气相淬冷法技术,装置单线年产能规模6000~15000吨。以美丰股份、川化股份、山东海化、四川美氰、河南骏化为代表。第二和第三阶段,我国有一些企业引进了欧洲的高压法生产技术。第四阶段为2003年至今,北京烨晶科技有限公司总结以往经验,开发出了节能节资型(第三代)低压气相淬冷法技术。开创性地解决了以前各代气相淬冷法技术生产易堵塞、运行周期短、品质不稳定、能耗高、难以大型化等问题。该技术装置单线产能规模可达5万~10万吨/年,技术水平和装置规模都取得了突破,尤其在装置投资上比国外的高压法优势明显。该技术在国内推广的同时,还先后获得了日本、美国、韩国、欧盟专利授权,并以技术知识产权许可给德国鲁奇公司,于2012年在俄罗斯欧洲化学公司新建年产5万吨装置投产成功。
虽然国内三聚氰胺生产技术有了很大的突破,但是较国外先进的高压法技术水平,仍存在差距:一是企业装置规模偏小。据协会统计,三聚氰胺生产企业约22家,共84条生产线,平均年产能2.85万吨,规模装置总体偏小。二是装置运行周期短,技术水平和管理水平有待提高。目前国内很多装置为二、三代技术,连续运行周期为30~60天,而国外高压法装置运行高达340天。三是产品质量指标波动大,质量不稳定,产品粒度分布宽,松堆密度小。
顾宗勤强调,创新能力决定企业竞争力,企业产能过剩、产品结构雷同、竞争力不强的一个深层次原因,就是技术创新活力不足,自主创新能力滞后。“别人会的,我也会;别人不会的,我也不会”。这样的企业发展只能是重复建设,只能是墨守陈规的缓慢跟进。提升自主创新能力,实现差异化发展,是三聚氰胺企业必须要突破的一个短板。我国提高三聚氰胺技术水平的课题很多,如产品质量、节能减排和下游产品研发等,都只能依靠技术创新加以解决。
他建议,尽快淘汰已经失去竞争力的一、二代技术。同时,三聚氰胺企业要加大技术创新力度,并通过技术改造,提高装置的运转周期,提高产品的优级品率以及装置产能规模,并逐步实现装备特种材料的国产化。
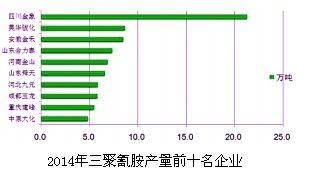
应用开发 紧贴生态文明建设
十八届五中全会将生态文明列入十大发展目标,把“美丽中国”写入“十三五”规划建议,并将“绿色发展”作为五大发展理念之一。可以说,十八届五中全会把生态环保放到了空前的高度。包括三聚氰胺在内的石油和化学工业不仅要实现自身绿色发展,更应紧跟生态文明建设新速度,为我国生态文明建设作出应有贡献。如何在当前严峻形势下把握机遇,主动作为,推动三聚氰胺绿色材料的发展,正是三聚氰胺行业共同关心的话题。
三聚氰胺本身是绿色产品,更能解决很多污染问题。顾宗勤建议,积极推进三聚氰胺甲醛树脂市场开拓,加大三聚氰胺泡绵的推广力度,推动三聚氰胺硬泡的工业化进程,加快三聚氰胺纤维的后加工与应用技术开发。他鼓励企业家们大胆拥抱终端市场。
三聚氰胺甲醛树脂方面,中国林产工业协会胶粘剂与表面加工专业委员会秘书长喻乐飞表示,当前国内人造板材生产耗胶量大,粗略估计年耗胶量在1696万吨左右。根据近年国家抽查情况看,胶黏剂因素是产品不合格的主要原因。国家室内车内环境及环保产品质量监督检验中心主任宋广生指出,当前,装饰装修和家具污染问题是影响中国人健康安全的主要问题。《乘用车内空气质量评价的强制标准》有望在年底出台,溶剂型胶将逐渐淘汰,热熔胶、水性胶等环保胶黏剂将获得更多应用。
据悉,当前国内板材使用的胶黏剂多为脲醛剂,其甲醛释放量较大,多数不符合国家标准,损害人体健康。而采用三聚氰胺胶黏剂的板材其环保性能、光泽度及磨损强度均远远好于使用脲醛胶的板材,能达到国际E0级环保标准,甲醛释放量远低于国内的标准。
为此,业内专家呼吁,希望政府相关部门能共同推动三聚氰胺胶黏剂在更大范围内使用,提高相关标准,改善我国室内、车内空气质量。
三聚氰胺泡绵是以三聚氰胺为原料生产的一种高开孔率、柔性好的新型泡绵塑料,具有吸音、阻燃、隔热、热稳定性、无烟毒性等多项优异特性。该产品在国际上已经大量应用于建筑、交通工具、航空、电子产品、家用电器、物品擦拭等行业。美国、德国等许多欧美国家已在大型场馆、太阳能集热器、各型客机、磁悬浮列车、火车机车、大型舰船、高级轿车等领域大量使用三聚氰胺泡绵。但在国内,三聚氰胺泡绵主要用于清洁领域,其他应用领域还有待开拓。值得高兴的是,河南中原大化集团有限公司2008年采用自主技术建成了国内首套三聚氰胺泡绵生产线,年产能10万立方米,其产品已用于世博展馆。2014年9月,成都玉龙化工股份有限公司的年产10万立方米三聚氰胺泡绵项目也顺利投产,产品已供给中国北车。
三聚氰胺硬泡是一种基于三聚氰胺甲醛改性树脂,经过烘箱或微波发泡并固化的闭孔硬质泡沫,具有轻质、隔音、防火、耐紫外线照射、导热系数低、尺寸稳定性好等优点,使用温度范围广(-120℃~220℃),是理想的保温节能材料。当前国内建筑保温市场用的聚氨酯、苯板、酚醛板等各种类保温材料存在阻燃效果差、价格高、稳定性差等缺点。而三聚氰胺硬泡具有永久阻燃、耐热性、可塑性等优势,且在相同阻燃性能等级上价格有明显优势。三聚氰胺纤维是三聚氰胺与甲醛树脂通过特有技术合成的产品,可生产出具有纺丝特性的高分子树脂,具有良好的耐热、防火特性和良好的透气、防霉和防螨性能、受热不熔滴、导热系数低、耐紫外线照射等特性,可应用于消防服、帐篷、手套、床上用品等。
据记者了解,四川金象赛瑞化工股份有限公司研发的三聚氰胺硬泡和三聚氰胺纤维产品已处于工业化实施阶段,其中三聚氰胺硬泡正就关键设备联合攻关;三聚氰胺纤维已经具备年产1000吨级规模短纤的生产能力。该产品具有明显的优势,若能实现替代,必将为三聚氰胺行业打开一个前景广阔的市场。顾宗勤建议,“十三五”期间要加快三聚氰胺硬泡的工业化进程,以及三聚氰胺纤维的后加工与应用技术开发。
此外,业内专家还提出了很多有建设性的三聚氰胺技术开发方向。譬如,顾宗勤介绍,RICE大学James Tour实验室的研究者用“蔗糖+三聚氰胺”生产出石黑烯,这可能将是一项前景光明的开创性科技创新,给三聚氰胺市场带来福音。南京工程学院高分子研究所所长杭祖圣提出了三聚氰胺甲醛树脂基阻燃纤维、三聚氰胺甲醛树脂基微球、三聚氰胺甲醛树脂空心微球、类石墨烯型氮化碳等方面的开发方向。
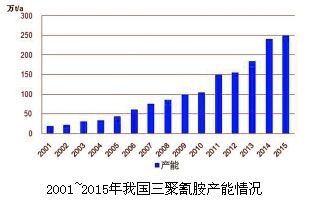
竞争力提升 打造循环经济产业链
三聚氰胺生产企业也是传统能源化工企业,近年来受到能源、资源、环境的制约因素越来越突出。随着经济的快速发展,能源供应日益趋紧,用水指标更加严格,碳减排压力不断增大,“三废”排放标准日趋严格,企业面临的资源环境约束矛盾更加突出。“十三五”期间,节能降耗和环保减排将是三聚氰胺行业的一项重要任务。
中国氮肥工业协会三聚氰胺分会会长、四川金象赛瑞化工股份有限公司副总裁唐印告诉记者,提升三聚氰胺产业竞争力,一方面要通过技术进步,让生产工艺清洁化、节能化;另一方面,要与其他产业结合起来,实现循环发展,让副产物变废为宝,减少无组织排放、过程副产物排放。这不但能减少排放,更能增加企业效益,增强企业应对市场变化的能力,提升我国三聚氰胺产业国际竞争力。
据介绍,按照目前工艺技术,以尿素为原料生产1吨三聚氰胺,大约产生近1吨氨和1.05吨的二氧化碳尾气。副产氨和二氧化碳尾气的利用方式是降低成本的有效途径,目前利用的方法主要有联产尿素、纯碱、乌洛托品等产品。
如果联产尿素,将三聚氰胺尾气转化为甲铵液,在高压条件下生成尿素。由于1吨氨可生产1.7吨尿素,尾气全部回收后,吨三聚氰胺的尿素消耗量就会由原来的3吨降低到1.6吨左右。不仅降低了生产成本,而且减少了废气排放。并且在联产过程中,直接利用熔融的尿素做原料,省去了尿素加热为尿液和三聚氰胺熔融工序,降低了蒸汽消耗,同时解决了碳化氨水排放污染问题。如果联产纯碱和氯化铵,省去了三聚氰胺装置氨碳分离装置,每吨三聚氰胺可节约蒸汽8吨,节电350千瓦时,并大幅度降低成本。
据记者了解,欧技公司的高压法生产技术已经基本实现无“三废”排放。
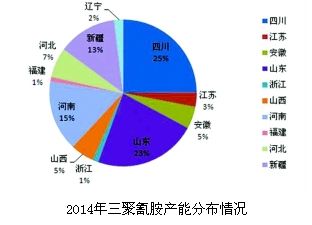
市场开拓 紧傍“一带一路”战略
对于三聚氰胺行业来说,出口是缓解国内市场压力的有效措施。“十二五”期间,三聚氰胺产品出口大幅增长,我国成为世界第一出口大国。2014年我国出口三聚氰胺23.56万吨,较2010年出口量13.4万吨增长76%。出口主要地区为欧洲、日本、美国、澳大利亚及东南亚地区。
不过,近年来我国三聚氰胺出口严重受阻。2014年12月9日,应美国基石化学品公司的申请,美国商务部对原产于中国的三聚氰胺进行反倾销和反补贴立案调查。今年11月2日,美国商务部发布公告,对原产于中国的三聚氰胺作出反倾销终裁,对中国认定普遍倾销幅度为:363.31%。同时,美国商务部作出反补贴终裁:山东青岛远达154.00%;四川美胺化工154.00%;青岛泛化国际贸易公司154.00%;山东联合化工股份有限公司156.90%;河南省煤业化工集团中原大化公司154.00%;中国普遍为154.58%。美国的反倾销、反补贴措施,致使我国出口美国的三聚氰胺大幅下降。
顾宗勤强调,美国的反倾销和反补贴可能导致其他国家效仿,将给我国出口带来很大的麻烦。因此,预计今后几年,我国三聚氰胺出口形势将会更加严峻。他建议各企业紧紧抓住国家“一带一路”政策带来的新机遇,加强国际市场合作,特别是要加强与“一带一路”沿线国家,如东南亚、欧洲、中亚和中东等地区之间的贸易合作。
《三聚氰胺行业“十三五”发展思路》(初稿)也提出,“十三五”期间实现海外投资建设1~2套拥有自主知识产权的三聚氰胺生产装置。