据了解,该技术是由南京敦先化工科技有限公司开发成功的第五代升级版等温变换技术,该技术反应器换热管上下端采取球腔联箱、进出总水管与壳体的气水之间密封为焊接密封、依靠特制换热管消除热应力,不仅安全坚固,而且实现不卸催化剂前提下实现催化剂框检查检修任务;首次成功应用于大型化煤化工装置。
南京敦先公司总经理王庆新介绍说,自2012年底首套可控移热变换装置投入运行以来,该公司本着不断加大科技投入,大力实施技术创新与研究,在原Ⅰ~Ⅳ(第一至第四代)变换反应器基础上开发出了Ⅴ型可控移热变换反应器,并在山东华鲁恒升化工股份有限公司与6.9MPa水煤浆气化相配套单系列变换装置成功投入运行,标志着可控移热变换技术成功迈入大型化煤化工领域,为南京敦先公司已经承接宁夏宝丰220万吨甲醇、内蒙古伊泰200万吨煤制油等大型化煤化工的可控移热变换工程实施积累了丰富工程经验。
王庆新告诉中国化工报记者,该套变换装置为全新设计,2016年2月下旬工程开始实施,经过近两年的建设,今年3月上旬顺利投入运行,各项指标均达到或优于设计指标,Ⅴ型可控移热变换技术彻底解决了现有水移热变换承压部件易泄露、催化剂难自卸、存在露点腐蚀、单系列装置难以大型化等难题,为煤制氢、煤制油、煤制天然气、煤制甲醇、煤制烯烃、煤制乙二醇等大型现代煤化工变换装置及现有传统变换装置节能改造提供了一项投资低、运行稳定、节能降耗、利于大型化煤化工项目的新型变换技术。
用户反馈
山东华鲁恒升化工股份有限公司副总经理潘得胜:该套可控移热变换装置实现了预期目标,与传统绝热变换技术相比具有以下明显优势:一、单套变换装置不仅能够处理湿基气量950000Nm3/h,也可以根据乙二醇、甲醇及氨的市场价格波动任意调整乙二醇、甲醇及氨不同产能,使企业获得最大利润,调节简捷、安全、迅速充分体现了该装置工艺流程及工艺控制设计的全面、安全、稳定、实用、简捷、多元化等特点;二、以30万吨合成氨的传统两段绝热变换工艺对比,采取可控移热变换技术后,变换系统出口CO由原来的1.5%降至0.4%,在不增加原料气气量前提下,仅通过提高CO转化率则每小时多产4142Nm3氢气,合成氨全年增产1.668万吨,单位产品合成氨综合能耗降低约1.5%,年节能量达23000吨标煤。仅此一项企业全年可获得约4170万元的纯利润,目前水煤浆加压气化的绝热变换装置国内有近百套,可控移热变换技术应用成功将为这些企业节能增效提供了良好条件;三、可控移热变换技术主要利用埋设在催化剂床层内部移热管束中的水带走反应热量,终端催化剂床层出口温度是一个定值,对于水煤浆变换装置而言,不仅能产过热蒸汽、回收高品位热能多、低品位热能少、后续热能回收稳定、降低工程投资,而且可以有效延长各反应器催化剂使用寿命;四、一变径向绝热床层阻力≤0.036MPa、二变可控移热径向床层阻力≤0.021MPa,虽然变换系统设置了4级蒸汽蒸发器,系统总阻力仍≤0.37MPa,与传统两段轴向绝热变换系统相比降低了0.13~0.18 MPa,径向催化剂床层投入运行为单系列装置大型化奠定了良好基础;五、该套变换装置终端反应器选择可控移热变换反应器,为乙二醇、合成氨提供氢气过程中,气体一次性通过就实现变换系统出口CO≤0.40%,完全实现变换装置影响开车时间为零,有效降低开车费用;六、Ⅴ型可控移热变换反应器,上下球腔作为换热管束联箱有效解决联箱水侧等温、气侧不等温产生热应力难题,利于催化剂床层外围设置绝热层,不仅实现了外围高温反应内侧低温平衡、有效延长催化剂使用寿命、降低运行能耗,而且利于催化剂自卸。
专家观点
山东化肥工业协会高级顾问杨春升:创新是企业的发展第一动力,惟创新者进、惟创新者强、惟创新者胜,一个新的技术出现必定会存在诸多不足,需要创新者不断改进、完善才能够使得此项新技术始终处于领先位置。可控移热变换(俗称等温变换)是煤化工领域唯一一项国人独创领先于国际的专利技术,南京敦先在不足六年内开发出Ⅰ~Ⅴ可控移热变换反应器,并成功应用到尾气利用、煤制氢、固定床煤气化、粉煤加压气化、水煤浆加压气化等装置,充分说明该公司牢牢抓住创新及不断完善理念,更能说明水移热变换仍有诸多需要改进地方。变换技术应用范围广,原料气源多元化,希望专利技术公司一定要不断进取、勇于创新、戒骄戒躁将可控移热变换(俗称等温变换)进一步发扬光大。
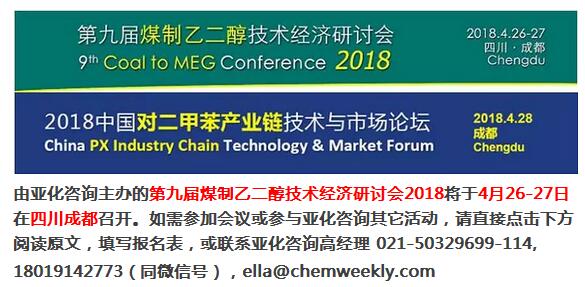