煤制氢优点与实例
氢气是目前石油化工领域中用量最大的一种化工原料,广泛用于生产合成氨、油品、甲醇以及石油炼制过程的加氢反应。氢能作为一种洁净、高效可储存、可再生的能源受到人们越来越多的关注。我国是以煤炭为主要能源的国家,以煤炭为原料制取氢气供给终端用户使用,集中处理有害废物将污染降低到最低水平,是一种相对环保的制氢路线。
煤炭制氢涉及复杂的工艺过程。煤炭经过气化、一氧化碳耐硫变换、酸性气体脱除、氢气提纯等关键环节,可以得到不同纯度的氢气。一般情况下,煤气化需要氧气,因此煤炭制氢还需要与之配套的空分系统。
煤制取氢气优点是技术日臻成熟,原料成本低,装置规模大。缺点是设备结构复杂、运转周期相对短、投资高、配套装置多。
随着我国成品油升级,各种加氢工艺应用越来越广,煤气化制氢相比干气和轻油制氢具有成本优势。
对蒸汽转化制氢、水煤浆气化制氢、干粉煤气化制氢及渣油气化制氢的成本进行分析比较后可以认为,利用煤和石油加工过程中得到的低值产品石油焦制氢,改变了传统的制氢原料路线,可以解决制氢成本高的问题。
同时,替代出来的炼厂石脑油、干气、天然气等原料用于生产经济效益更高的石化产品。例如:轻油一般可作为乙烯裂解原料,生产乙烯、丙烯等高附加值产品;干气根据组成不同,可用作乙烯装置原料或低硫工艺炉燃料。
由中石化南京工程公司EPC总承包九江煤制氢项目启动。该项目总投资14亿元,采用GE水煤浆气化技术,年产氢10万吨,于2014年投料试车。九江石化煤制氢项目选用的低温甲醇洗工艺采用半贫液技术,以冷甲醇作为溶剂脱除酸性气体,是中国石化自有专利技术的首次国产化实践,具有能耗低,工艺气体净化度高,吸收选择性高,甲醇的热稳定性和化学稳定性好,能够有效脱除原料气的硫化氢、二氧化碳和COS组分等优点。
2014年1月23日,中石化集团茂名石化油品质量升级改造工程煤制氢装置成功生产出合格氢气。该套装置是目前中国单产能力最大的煤制氢装置,它的建成投用,既可满足茂名石化汽柴油质量从国四升级至国五的用氢需求,又可缓解炼油扩能后氢气资源不足的压力,对于茂名石化优化资源、调整结构、绿色生产、节能降耗具有重要意义。据了解,该煤制氢装置总投资30亿元人民币,于2011年9月动工建设,是茂名石化油品质量升级改造工程的重要配套项目,也是中国石化重点工程建设项目,主要包括水煤浆气化装置、合成气净化装置以及配套设施,以煤、炼厂副产的高硫石油焦和纯氧为主要原料,每小时可生产出20万标立方米、纯度为97.5%以上、4.8兆帕的工业氢气。该装置水煤浆气化单元采用美国GE公司水煤浆气化技术,合成气净化单元耐硫变换及甲烷化采用中国石化自主技术,酸性气体脱除采用德国鲁齐(Lurgi)低温甲醇洗技术等先进的工艺技术。装置设备材料国产化率99%,高98米的吸收塔是目前全国同类装置最大的设备,低温甲醇洗吸收塔塔体材料首次实现了国产化。
截至2014年7月5日,长岭炼油厂加氢炼油装置连续45天试用巴陵煤制氢气1100万标准立方米,安全及各项工艺指标均达到生产要求,标志着长炼首次大规模试用煤制氢气获得成功。长炼800万吨炼油项目有7套加氢装置,氢气主要依靠5万标准立方米每小时制氢和70万吨重整装置提供,需要消耗大量的炼厂干气,每年损耗乙烯资源4万多吨,氢气生产成为影响该企业成品油加工成本的重要因素。2013年,为了实现区域资源优化,总部在岳阳地区建成“巴陵-长岭”氢气管线,将巴陵石化煤制气装置甲烷化后含氢量85.84%的原料气提纯至99.5%的氢气,以每小时3000多标准立方米的流量输送量至巴陵石化云溪片区及长炼氢气管网。综合数据表明,长炼试用煤制氢后,用氢总体成本下降33%至35%。
2014年7月14日,巴陵石化合成橡胶事业部首次采用长输管线输送的煤制氢气生产热塑橡胶SEBS获得成功。至7月17日,两套SEBS装置平均每小时用氢量约2000标准立方米(180千克),累计用量达9.32吨,已采用煤制氢生产SBES产品260多吨,合格率100%,目前日产120吨左右。氢气是热塑橡胶SEBS生产的重要原料之一,巴陵石化合成橡胶事业部自2006年实现SEBS工业化生产以来,一直使用电解氢气。近年来,随着装置扩能改造,低负荷电解氢气供应“吃紧”,影响SEBS装置稳产高产及市场开拓。2014年4月20日,巴陵石化建成的国内最长煤制氢气输送管线顺利投用,首站至分输站引入氢气。与此同时,公司内部原有的电解及干气制氢装置关停。为优化氢气资源利用,公司合成橡胶事业部将煤制氢气引入热塑橡胶装置生产。试用煤制氢与干气制氢的掺混氢生产SEBS,经分析检测,产品加氢度达97.5%,各项指标均满足生产要求。巴陵石化煤制氢不仅量大,能充分满足SEBS生产需求,且相比电解制氢,品质更高,有利于SEBS关键指标加氢度稳定。氢压机停运后,每天可节电近3200度,价值约1800元。目前,合成橡胶事业部继续对氢气外管系统和煤制氢使用情况进行跟踪,并做好将煤制氢引入聚丙烯装置的准备工作。
由华东理工大学开发的多喷嘴对置式水煤浆气化技术,2014年11月13日将用于江苏恒力集团在大连建设的国内单产能力最大的煤制氢装置。该水煤浆气化装置设计为4开2备,总生产能力为46万立方米(CO+H2)/时。江苏恒力集团是全球最大的织造企业,同时也是全球最大的超亮光丝和工业丝生产基地,该集团在大连建设的炼化一体项目选择多喷嘴对置式水煤浆气化技术用于煤制氢气,氢气生产能力为32.1万立方米/时,是目前我国最大的煤制氢系统,该装置还同时生产50万吨甲醇/年,醋酸35万吨/年,以及燃料气3万立方米/时。
荆门英德气体有限公司(中国荆门)是工业气体供应商英德气体集团(香港)的子公司,该公司已于2017年10月20日开始在湖北省荆门化学品回收工业园区建设煤制氢和综合利用项目的主要生产设施。该项目将建设一个气体岛,为该工业园区的邻近装置提供氨和甲醇等工业气体和某些化学原料,特别是为中国石化子公司炼油公司中石化荆门公司提供升级和扩容项目。该项目将通过水煤浆夹带式流化床气化技术将煤炭转化为气体混合物,然后通过三种过程:变压吸附分离氢气、液氮洗涤分离氨和甲醇合成和蒸馏生产甲醇。该项目的氢气能力为5.3万立方米/小时、氨能力为20万吨/年、甲醇能力为40万吨/年,副产氧、氮、氩和硫。该公司表示,新装置将于2018年9月底开始向中国石化荆门公司供应氢气。
“
神华集团已经建成的世界上第一套百万吨级煤炭直接液化示范工厂,采用两套荷兰壳牌(Shell)公司的SCGP粉煤加压气化工艺,为煤液化、加氢稳定、加氢改质等装置提供氢气原料,单套日产氢能力为313吨,氢气纯度为99.5%(mole),CO+CO2≤20μg/g。
煤制氢在炼厂的应用
炼油厂制氢原料主要有炼厂干气、天然气、煤、石脑油和重油等,制氢原料路线的选择主要取决于原料的可获得性和成本。在高油价的现状下,中国炼厂石脑油和重油制氢已不具经济性,逐步被淘汰。目前国内炼化一体化项目典型氢源包括:天然气或煤制氢、干气制氢、重整装置副产氢、PSA回收氢及乙烯装置产氢。
中国外购天然气制氢的炼厂,天然气价格一般超过3元/立方米,而沿海地区使用进口LNG的炼厂,天然气成本高达4元/立方米左右,在此条件下,炼厂以大规模煤气化装置制氢更具经济性,有以下一系列优点。
1. 煤制氢成本低。以9万Nm3/h制氢规模为例,水煤浆气化和天然气制氢装置投资分别为12.4亿元和6亿元。虽然煤制氢投资高很多,但在氢气价格(成本+10%投资回报)为1.5万元/吨(1.36元/ m3)时,对应的煤和天然气成本分别为805元/吨和2.58元/ m3,而且还没计算煤制氢副产大量蒸汽的价值。
2. 煤气化装置(废热锅炉流程)副产的大量蒸汽,可节省炼厂燃料油。节省出来的燃料油可作为焦化装置原料增产成品油。
3. 廉价的煤制氢可替代干气制氢。节约的干气可用于提取乙烯等化工原料,增加经济效益。
4. 水煤浆气化制氢原料灵活,可接受石油焦和煤在相当宽的比例范围内混合进料。在煤价高而石油焦价格低的时候,解决石油焦销路问题;而煤价低,石油焦市场价格高的情况下,可全部气化煤,以实现效益最大化。
由于上述优势,煤制氢在炼厂正在取得越来越广泛的应用。从2009~2013年,中国炼厂新建煤/石油焦制氢项目如下表所示。
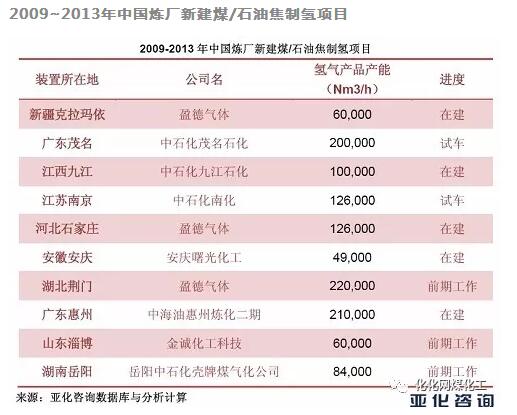
不仅是在中国,煤制氢也被印度企业所选择。
2012年5月,印度最大的私营企业信诚工业公司建设全球最大的石油焦/煤气化多联产项目,项目位于该公司拥有的世界最大炼油厂区——贾姆纳加尔——总炼油能力为130万桶/天(6200~6500万吨/年)。据印度媒体报道,该项目总投资40亿美元,采用E-Gas气化技术(气流床两段水煤浆气化),根据公开数据,该项目采用10台进料量约3000吨/天的气化炉,多联产产品方案将包括氢气、电力、蒸汽、合成天然气(SNG)和醋酸等乙酰基化工产品。
总的来说,在油价和天然气价格高企,而煤炭价格相对平稳的现状下,大规模煤气化制氢不仅具备成本优势,而且可以优化炼厂的物料平衡,已经成为中国炼厂制氢的重要发展方向。
将煤炭或焦炭原料转化为氢气,该项技术已在中国石化下属金陵石化、齐鲁石化、南化公司成功应用。与传统干气制氢工艺相比,煤制氢装置的水煤浆制氢工艺可节约成本20%到25%。
由中石化南京工程公司EPC总承包九江煤制氢项目启动。该项目总投资14亿元,采用GE水煤浆气化技术,年产氢10万吨,于2014年投料试车。九江石化煤制氢项目选用的低温甲醇洗工艺采用半贫液技术,以冷甲醇作为溶剂脱除酸性气体,是中国石化自有专利技术的首次国产化实践,具有能耗低,工艺气体净化度高,吸收选择性高,甲醇的热稳定性和化学稳定性好,能够有效脱除原料气的硫化氢、二氧化碳和COS组分等优点。
2014年1月23日,中石化集团茂名石化油品质量升级改造工程煤制氢装置成功生产出合格氢气。该套装置是目前中国单产能力最大的煤制氢装置,它的建成投用,既可满足茂名石化汽柴油质量从国四升级至国五的用氢需求,又可缓解炼油扩能后氢气资源不足的压力,对于茂名石化优化资源、调整结构、绿色生产、节能降耗具有重要意义。据了解,该煤制氢装置总投资30亿元人民币,于2011年9月动工建设,是茂名石化油品质量升级改造工程的重要配套项目,也是中国石化重点工程建设项目,主要包括水煤浆气化装置、合成气净化装置以及配套设施,以煤、炼厂副产的高硫石油焦和纯氧为主要原料,每小时可生产出20万标立方米、纯度为97.5%以上、4.8兆帕的工业氢气。该装置水煤浆气化单元采用美国GE公司水煤浆气化技术,合成气净化单元耐硫变换及甲烷化采用中国石化自主技术,酸性气体脱除采用德国鲁齐(Lurgi)低温甲醇洗技术等先进的工艺技术。装置设备材料国产化率99%,高98米的吸收塔是目前全国同类装置最大的设备,低温甲醇洗吸收塔塔体材料首次实现了国产化。
截至2014年7月5日,长岭炼油厂加氢炼油装置连续45天试用巴陵煤制氢气1100万标准立方米,安全及各项工艺指标均达到生产要求,标志着长炼首次大规模试用煤制氢气获得成功。长炼800万吨炼油项目有7套加氢装置,氢气主要依靠5万标准立方米每小时制氢和70万吨重整装置提供,需要消耗大量的炼厂干气,每年损耗乙烯资源4万多吨,氢气生产成为影响该企业成品油加工成本的重要因素。2013年,为了实现区域资源优化,总部在岳阳地区建成“巴陵-长岭”氢气管线,将巴陵石化煤制气装置甲烷化后含氢量85.84%的原料气提纯至99.5%的氢气,以每小时3000多标准立方米的流量输送量至巴陵石化云溪片区及长炼氢气管网。综合数据表明,长炼试用煤制氢后,用氢总体成本下降33%至35%。
2014年7月14日,巴陵石化合成橡胶事业部首次采用长输管线输送的煤制氢气生产热塑橡胶SEBS获得成功。至7月17日,两套SEBS装置平均每小时用氢量约2000标准立方米(180千克),累计用量达9.32吨,已采用煤制氢生产SBES产品260多吨,合格率100%,目前日产120吨左右。氢气是热塑橡胶SEBS生产的重要原料之一,巴陵石化合成橡胶事业部自2006年实现SEBS工业化生产以来,一直使用电解氢气。近年来,随着装置扩能改造,低负荷电解氢气供应“吃紧”,影响SEBS装置稳产高产及市场开拓。2014年4月20日,巴陵石化建成的国内最长煤制氢气输送管线顺利投用,首站至分输站引入氢气。与此同时,公司内部原有的电解及干气制氢装置关停。为优化氢气资源利用,公司合成橡胶事业部将煤制氢气引入热塑橡胶装置生产。试用煤制氢与干气制氢的掺混氢生产SEBS,经分析检测,产品加氢度达97.5%,各项指标均满足生产要求。巴陵石化煤制氢不仅量大,能充分满足SEBS生产需求,且相比电解制氢,品质更高,有利于SEBS关键指标加氢度稳定。氢压机停运后,每天可节电近3200度,价值约1800元。目前,合成橡胶事业部继续对氢气外管系统和煤制氢使用情况进行跟踪,并做好将煤制氢引入聚丙烯装置的准备工作。
由华东理工大学开发的多喷嘴对置式水煤浆气化技术,2014年11月13日将用于江苏恒力集团在大连建设的国内单产能力最大的煤制氢装置。该水煤浆气化装置设计为4开2备,总生产能力为46万立方米(CO+H2)/时。江苏恒力集团是全球最大的织造企业,同时也是全球最大的超亮光丝和工业丝生产基地,该集团在大连建设的炼化一体项目选择多喷嘴对置式水煤浆气化技术用于煤制氢气,氢气生产能力为32.1万立方米/时,是目前我国最大的煤制氢系统,该装置还同时生产50万吨甲醇/年,醋酸35万吨/年,以及燃料气3万立方米/时。
荆门英德气体有限公司(中国荆门)是工业气体供应商英德气体集团(香港)的子公司,该公司已于2017年10月20日开始在湖北省荆门化学品回收工业园区建设煤制氢和综合利用项目的主要生产设施。该项目将建设一个气体岛,为该工业园区的邻近装置提供氨和甲醇等工业气体和某些化学原料,特别是为中国石化子公司炼油公司中石化荆门公司提供升级和扩容项目。该项目将通过水煤浆夹带式流化床气化技术将煤炭转化为气体混合物,然后通过三种过程:变压吸附分离氢气、液氮洗涤分离氨和甲醇合成和蒸馏生产甲醇。该项目的氢气能力为5.3万立方米/小时、氨能力为20万吨/年、甲醇能力为40万吨/年,副产氧、氮、氩和硫。该公司表示,新装置将于2018年9月底开始向中国石化荆门公司供应氢气。
煤气化制氢是工业大规模制氢的首选方式之一。虽然传统煤气化制氢工艺成熟,但其投资成本大、需用纯氧、气体分离成本高、产氢效率偏低、CO2排放量大。降低煤气化制氢工艺CO2排放的关键在于提高过程热效率、避免复杂的气体分离过程。借助于氧载体的传递作用,化学链制氢技术可实现氧和热在燃料反应器、蒸汽反应器和空气反应器之间的转移,从而使CO2、H2、N2内在分离,既直接利用空气、也能获得高浓度的CO2和H2。铁基氧载体是化学法制氢的理想氧载体之一,然而在燃料反应器中,铁基氧载体与煤的直接反应速率很慢且该反应器吸热。如何促进氧载体与煤的直接反应速率且使燃料反应器自热是该制氢技术的关键。
在前期研究的基础上,山西煤炭化学研究所提出添加碱金属催化剂来促进Fe2O3与煤的直接反应速率。他们通过添加Al2O3,一方面作为惰性组分防止氧化铁的烧结,另一方面与FeO反应生成铁铝氧载体,释放反应热为燃料反应器提供部分热量。模拟结果表明,采用该技术过程各反应器都能实现自热,制氢热效率可达75%,生成的铁铝氧载体则能被空气氧化回到初始相态,实现氧循环。
2016年12月25日,西安交通大学首个重大科研成果产业化项目——“煤炭超临界水气化制氢发电多联产技术”产业化工作正式启动。西安交大研究团队经过20年攻关,研发的这项技术,提出了一种煤炭在超临界水中完全吸热-还原制氢的新气化原理。它利用温度和压力达到或高于水的临界点(374.3℃、22.1MPa)时水的特殊物理化学性质,将煤中的碳、氢、氧元素气化转化为氢气和二氧化碳,同时热化学分解了部分超临界水制取氢气,将煤炭化学能直接高效转化为氢能。气化过程中煤所含的氮、硫及金属元素及各种无机矿物质及灰分,由于不被氧化,会在反应器内随着气化而逐步净化沉积于底部,以灰渣的形式排出反应器,从源头上根除了二氧化硫、氮氧化物等气体污染物和PM2.5等粉尘颗粒物的生成和排放。与传统“一把火烧煤”相比,该技术发电和制氢的效率显著提高,大型化后的一次性投资和运行成本则显著降低。气化产物可发电、供热、供蒸汽,还可生产高附加值化工产品,实现了煤炭能源的高效、洁净、无污染转化和利用。
西安交通大学研发的攻关研发的这项技术,提出了一种煤炭在超临界水中完全吸热一还原制氢的新气化原理,被称为“超临界水蒸煤”,具有完全自主知识产权。该技术适用于无烟煤、烟煤、褐煤、兰炭等不同的煤种,碳转化效率可达96%~99%。据测算,该技术实现大型工业化后,每标准立方米氢气成本不到0.58元,比常规煤气化制氢低0.05元。
为深化产学研合作,推动学校科技成果转移转化,中核全联投资基金管理(北京)有限公司、香港日富投资有限公司和西安北奇能源科技发展有限公司共同发起成立混合所有制的技术产业化投资公司——陕西中核交大超洁能源技术有限公司,推动该项技术产业化。西安交大将该技术成果知识产权及相关技术作价1.5亿元人民币转让给产业化投资公司。该公司将在初期筹资10亿元进行技术产业化的工程示范。据了解,项目产业化公司三年内力争完成该技术首个产业化示范项目的建设和运行,加速推动该技术在煤炭高效清洁利用、环境保护等方面的推广应用。目前已确定先将50MW发电及热电联产机组、燃煤工业供热蒸汽锅炉替代产品等作为工程示范的切入点。
中国拟在建十五个炼化一体化项目,已有11个采用煤制氢!
随着成品油质量升级的推进,国内新建炼油厂大多选择了全加氢工艺路线,以满足轻质油收率、产品质量、综合商品率等关键技术经济指标要求,这极大增加氢气需求和制氢技术的市场。
在高油价时期,具备成本优势的煤/石油焦气化制氢成为中国炼厂制氢的发展趋势。随着原油和天然气价格持续走低,油制氢、天然气制氢和煤制氢的成本差距在缩小。
研究发现,煤/石油焦制氢仍然是中国炼厂制氢的主流工艺路线,已确定采用煤制氢的项目有11个,确定采用天然气制氢的只有1个。
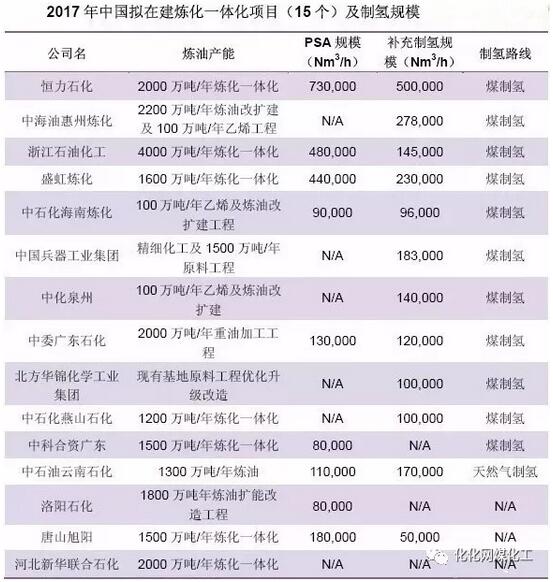